Introduction to Ultra-Thin PCB Technology
Ultra-thin PCB, also known as thin printed circuit board or micro PCB, is a type of printed circuit board that is significantly thinner than traditional PCBs. These boards are designed to meet the growing demand for smaller, lighter, and more compact electronic devices. Ultra-thin PCBs are typically less than 0.4 mm thick, with some advanced designs reaching thicknesses as low as 0.1 mm.
The development of ultra-thin PCB technology has been driven by the miniaturization trend in the electronics industry. As devices become smaller and more portable, there is a need for PCBs that can fit into these compact spaces while still providing the necessary functionality and reliability. Ultra-thin PCBs offer several advantages over traditional PCBs, including reduced weight, improved flexibility, and enhanced thermal management.
Key Characteristics of Ultra-Thin PCBs
-
Thickness: Ultra-thin PCBs are defined by their thickness, which is typically less than 0.4 mm. Some advanced designs can be as thin as 0.1 mm.
-
Material: Ultra-thin PCBs are usually made from polyimide or other flexible substrate materials that can withstand the stresses of bending and folding.
-
Layer count: Due to their reduced thickness, ultra-thin PCBs typically have fewer layers compared to traditional PCBs. Most ultra-thin PCBs have between 1 and 4 layers.
-
Trace width and spacing: To accommodate the reduced thickness, ultra-thin PCBs often have smaller trace widths and spacing compared to traditional PCBs.
-
Flexibility: Many ultra-thin PCBs are designed to be flexible, allowing them to conform to the shape of the device or enclosure in which they are installed.
Applications of Ultra-Thin PCBs
Ultra-thin PCBs find applications in a wide range of industries and devices where space is at a premium and weight reduction is crucial. Some of the most common applications include:
Consumer Electronics
- Smartphones and tablets
- Wearable devices (smartwatches, fitness trackers)
- Portable audio devices (earbuds, headphones)
- Digital cameras and camcorders
Medical Devices
- Implantable devices (pacemakers, neurostimulators)
- Wearable medical monitors
- Portable medical equipment
- Medical imaging devices
Automotive Electronics
- In-vehicle infotainment systems
- Advanced driver assistance systems (ADAS)
- Vehicle control modules
- Sensor integration
Aerospace and Defense
- Unmanned aerial vehicles (UAVs)
- Satellite communication systems
- Portable military equipment
- Avionics systems
Industrial Applications
- Portable test and measurement equipment
- Industrial control systems
- Robotics and automation
- Portable data acquisition devices
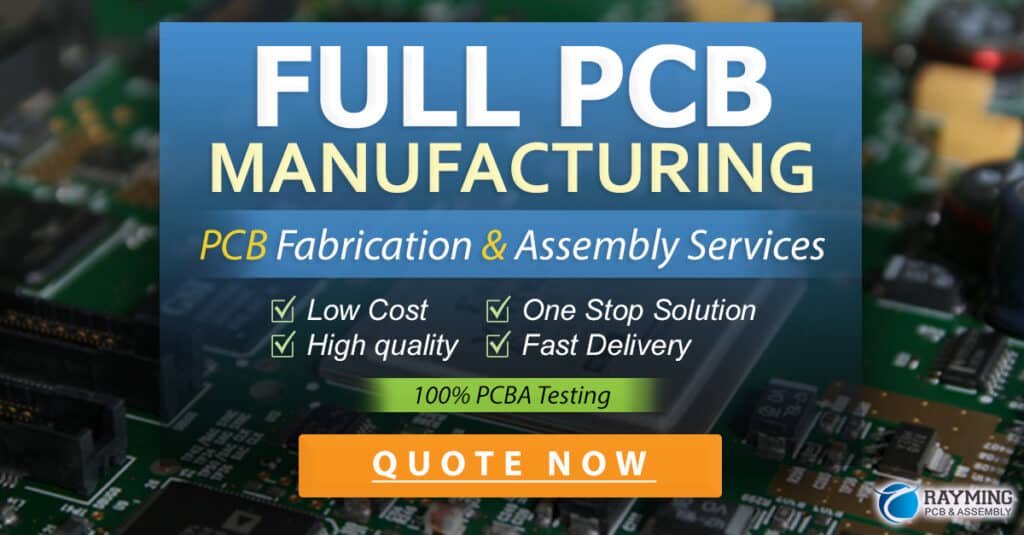
Advantages of Ultra-Thin PCBs
Ultra-thin PCBs offer several advantages over traditional PCBs, making them an attractive choice for many applications.
Reduced Weight and Size
One of the primary advantages of ultra-thin PCBs is their reduced weight and size. By using thinner substrate materials and minimizing the number of layers, ultra-thin PCBs can be significantly lighter and more compact than traditional PCBs. This is particularly important in applications where weight and size are critical factors, such as in portable devices or aerospace systems.
Improved Flexibility
Many ultra-thin PCBs are designed to be flexible, allowing them to conform to the shape of the device or enclosure in which they are installed. This flexibility enables designers to create more ergonomic and space-efficient devices, as the PCB can be bent or folded to fit into tight spaces. Flexible ultra-thin PCBs also offer improved durability, as they can better withstand the stresses of vibration and mechanical shock.
Enhanced Thermal Management
Ultra-thin PCBs can help improve thermal management in electronic devices. The reduced thickness of the board allows for better heat dissipation, as the heat generated by components can more easily transfer through the thin substrate to a heat sink or other cooling solution. This improved thermal management can help increase the reliability and longevity of electronic devices, particularly in high-performance applications.
Cost Reduction
In some cases, ultra-thin PCBs can help reduce the overall cost of electronic devices. By using fewer layers and less material, the raw material costs for ultra-thin PCBs can be lower than those for traditional PCBs. Additionally, the reduced weight and size of ultra-thin PCBs can lead to cost savings in shipping and packaging.
Challenges in Ultra-Thin PCB Design and Manufacturing
While ultra-thin PCBs offer many advantages, they also present several challenges in terms of design and manufacturing.
Material Selection
Choosing the right substrate material is critical for ultra-thin PCBs. The material must be thin enough to meet the desired thickness requirements while still providing adequate mechanical strength and electrical properties. Polyimide is a common choice for ultra-thin PCBs due to its excellent mechanical and thermal properties, but other materials such as liquid crystal polymer (LCP) and polyethylene naphthalate (PEN) may also be used.
Trace Width and Spacing
Ultra-thin PCBs often require smaller trace widths and spacing compared to traditional PCBs to accommodate the reduced thickness. This can make the design and layout process more challenging, as designers must ensure that the traces are properly spaced and sized to avoid signal integrity issues and manufacturing defects.
Handling and Assembly
The thin and flexible nature of ultra-thin PCBs can make them more difficult to handle and assemble compared to traditional PCBs. Special care must be taken during the manufacturing process to avoid damaging the delicate boards, and specialized equipment may be required for pick-and-place and soldering operations.
Reliability and Durability
Ensuring the reliability and durability of ultra-thin PCBs can be challenging, particularly in applications where the boards are subjected to mechanical stress or harsh environmental conditions. Proper material selection, design techniques, and manufacturing processes are essential for creating ultra-thin PCBs that can withstand the rigors of their intended application.
Manufacturing Process for Ultra-Thin PCBs
The manufacturing process for ultra-thin PCBs is similar to that of traditional PCBs, but with some key differences to accommodate the reduced thickness and special material requirements.
Material Preparation
The first step in the manufacturing process is to prepare the substrate material. For ultra-thin PCBs, this typically involves using a thin, flexible material such as polyimide. The material is cleaned and treated to ensure good adhesion of the copper layers.
Copper Deposition
Next, a thin layer of copper is deposited onto the substrate material. This can be done using various methods, such as electroless plating, electrolytic plating, or sputtering. The thickness of the copper layer is carefully controlled to ensure the desired electrical properties and mechanical strength.
Patterning and Etching
Once the copper layer is deposited, the desired circuit pattern is transferred onto the board using a photolithographic process. A photoresist material is applied to the copper layer, and the circuit pattern is exposed using UV light. The exposed areas of the photoresist are then removed, leaving the desired circuit pattern. The exposed copper is then etched away using a chemical solution, leaving only the copper traces that form the circuit.
Lamination and Drilling
If the ultra-thin PCB design requires multiple layers, the patterned layers are laminated together using heat and pressure. The laminated board is then drilled to create holes for component placement and interconnection between layers.
Surface Finishing
Finally, the ultra-thin PCB undergoes a surface finishing process to protect the copper traces and improve solderability. Common surface finishes for ultra-thin PCBs include organic solderability preservative (OSP), immersion silver, and electroless nickel/immersion gold (ENIG).
Testing and Quality Control for Ultra-Thin PCBs
Ensuring the quality and reliability of ultra-thin PCBs is critical, particularly given their use in demanding applications. Several testing and quality control methods are used to verify the performance and durability of ultra-thin PCBs.
Visual Inspection
Visual inspection is the first line of defense in detecting manufacturing defects and ensuring the overall quality of ultra-thin PCBs. Automated optical inspection (AOI) systems are commonly used to quickly and accurately identify issues such as incomplete etching, short circuits, and incorrect component placement.
Electrical Testing
Electrical testing is performed to verify the functionality and performance of ultra-thin PCBs. This can include continuity testing to ensure proper interconnection between components, insulation resistance testing to detect potential leakage paths, and high-potential (hipot) testing to verify the board’s ability to withstand high voltages.
Mechanical Testing
Given the flexible nature of many ultra-thin PCBs, mechanical testing is essential to ensure the board’s durability and reliability. This can include bend testing to verify the board’s ability to withstand repeated flexing, as well as vibration and shock testing to simulate the stresses the board may encounter in its intended application.
Environmental Testing
Environmental testing is used to verify the performance of ultra-thin PCBs under various environmental conditions. This can include thermal cycling to assess the board’s ability to withstand temperature fluctuations, humidity testing to evaluate moisture resistance, and salt spray testing to simulate corrosive environments.
Future Trends in Ultra-Thin PCB Technology
As the demand for smaller, lighter, and more advanced electronic devices continues to grow, ultra-thin PCB technology is expected to evolve to meet these challenges.
Advanced Materials
Researchers are continually developing new materials that can offer improved performance and reliability for ultra-thin PCBs. These include advanced polymer substrates with better mechanical and thermal properties, as well as novel conductive materials that can enable smaller trace widths and spacing.
3D Printing
3D printing technology is being explored as a potential method for fabricating ultra-thin PCBs. This could enable the creation of complex, three-dimensional circuit structures that are not possible with traditional manufacturing methods.
Embedded Components
The integration of passive components, such as resistors and capacitors, directly into the PCB substrate is another area of interest. This embedded component technology can help further reduce the size and weight of ultra-thin PCBs while improving performance and reliability.
High-Frequency Applications
As the demand for high-speed, high-frequency electronic devices grows, ultra-thin PCBs are being developed to meet the unique challenges of these applications. This includes the use of advanced materials and design techniques to minimize signal loss and maintain signal integrity at high frequencies.
FAQs
-
What is the typical thickness of an ultra-thin PCB?
Ultra-thin PCBs are typically less than 0.4 mm thick, with some advanced designs reaching thicknesses as low as 0.1 mm. -
What materials are commonly used for ultra-thin PCBs?
Polyimide is a common choice for ultra-thin PCBs due to its excellent mechanical and thermal properties. Other materials, such as liquid crystal polymer (LCP) and polyethylene naphthalate (PEN), may also be used. -
Can ultra-thin PCBs be flexible?
Yes, many ultra-thin PCBs are designed to be flexible, allowing them to conform to the shape of the device or enclosure in which they are installed. This flexibility can improve durability and enable more ergonomic and space-efficient designs. -
What are some common applications for ultra-thin PCBs?
Ultra-thin PCBs are used in a wide range of applications, including consumer electronics (smartphones, wearables), medical devices (implantables, wearable monitors), automotive electronics (infotainment systems, ADAS), aerospace and defense (UAVs, satellite communication), and industrial applications (portable test equipment, robotics). -
What are the main challenges in designing and manufacturing ultra-thin PCBs?
The main challenges in ultra-thin PCB design and manufacturing include material selection, achieving small trace widths and spacing, handling and assembly difficulties due to the thin and flexible nature of the boards, and ensuring reliability and durability in demanding applications.
Conclusion
Ultra-thin PCB technology has emerged as a key enabler for the development of smaller, lighter, and more advanced electronic devices. By offering reduced weight, improved flexibility, and enhanced thermal management, ultra-thin PCBs are finding applications in a wide range of industries, from consumer electronics to medical devices and aerospace systems.
As the demand for miniaturized and high-performance electronic devices continues to grow, ultra-thin PCB technology is expected to evolve, with advancements in materials, manufacturing processes, and design techniques. By staying at the forefront of these developments, PCB manufacturers and designers can create innovative solutions that meet the ever-increasing demands of the electronics industry.
Characteristic | Ultra-Thin PCB | Traditional PCB |
---|---|---|
Thickness | < 0.4 mm | > 0.4 mm |
Layers | 1-4 | 4+ |
Material | Polyimide, LCP, PEN | FR-4, CEM-3 |
Flexibility | Often flexible | Rigid |
Trace Width/Spacing | Smaller | Larger |