Introduction to SMT PCB
Surface Mount Technology (SMT) has revolutionized the production of Printed Circuit Boards (PCBs) since its introduction in the 1960s. SMT is a method of manufacturing electronic circuits in which the components are mounted directly onto the surface of a PCB. This technology has largely replaced the through-hole method, where components are inserted into holes drilled in the PCB and soldered on the opposite side.
SMT has become the dominant assembly process in the electronics industry due to its numerous advantages, including:
- Smaller component sizes
- Increased circuit density
- Improved performance
- Reduced manufacturing costs
- Faster assembly processes
In this article, we will explore the fundamentals of SMT PCB, its benefits, the assembly process, and its applications in various industries.
Understanding the Basics of SMT PCB
What is a Printed Circuit Board (PCB)?
A PCB is a flat board made of insulating materials, such as fiberglass or plastic, with conductive pathways etched on its surface. These pathways, also known as traces, connect various electronic components to form a complete circuit. PCBs serve as the foundation for most electronic devices, providing mechanical support and electrical connections for components.
Surface Mount Technology (SMT) vs. Through-Hole Technology (THT)
Before the widespread adoption of SMT, through-hole technology (THT) was the primary method for assembling electronic components on PCBs. In THT, components have long metal leads that are inserted into holes drilled in the PCB and soldered on the opposite side. While THT is still used for certain applications, it has several drawbacks compared to SMT:
- Larger component sizes
- Lower circuit density
- Slower assembly processes
- Higher manufacturing costs
In contrast, SMT components are smaller and have short leads or terminations that are soldered directly onto the surface of the PCB. This allows for higher component density, faster assembly, and reduced manufacturing costs.
Advantages of SMT PCB
SMT PCBs offer several benefits over their through-hole counterparts:
-
Miniaturization: SMT components are significantly smaller than through-hole components, allowing for more compact PCB designs and smaller electronic devices.
-
Increased circuit density: With smaller components and the absence of drilled holes, SMT PCBs can accommodate a higher number of components per unit area, enabling more complex and sophisticated electronic designs.
-
Improved performance: SMT components have shorter leads, which reduces parasitic inductance and capacitance, resulting in better high-frequency performance and reduced signal distortion.
-
Cost-effectiveness: The automated nature of the SMT assembly process, combined with the reduced material costs of smaller components, leads to lower overall manufacturing costs compared to THT.
-
Faster assembly: SMT allows for the use of automated pick-and-place machines, which can quickly and accurately place components on the PCB, reducing assembly time and increasing production throughput.
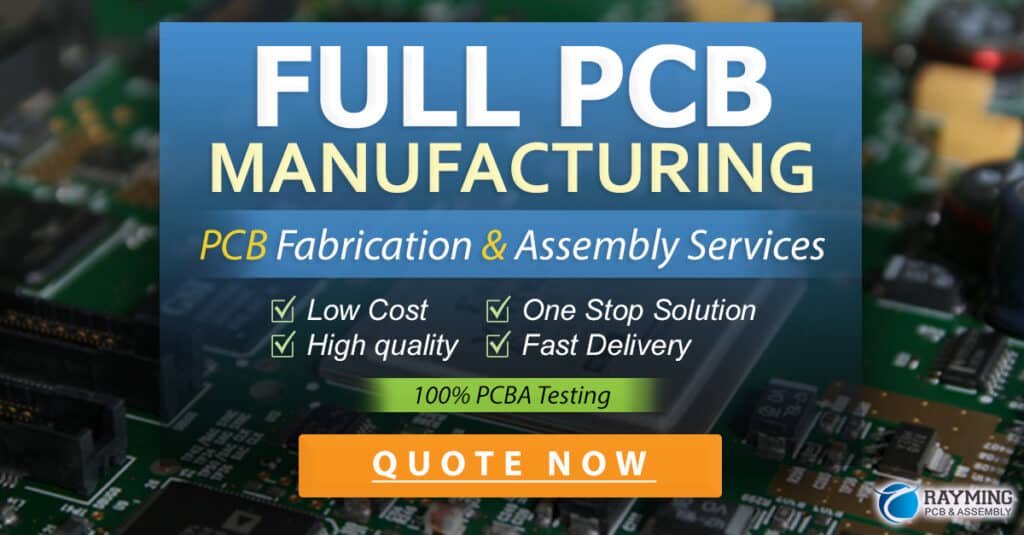
The smt pcb assembly Process
The SMT pcb assembly process consists of several key steps:
-
Solder paste application: A thin layer of solder paste, a mixture of tiny solder particles suspended in flux, is applied to the PCB’s surface using a stencil or solder paste printer. The solder paste is deposited on the pads where the SMT components will be placed.
-
Component placement: An automated pick-and-place machine uses a vacuum nozzle or gripper to pick up SMT components from reels or trays and place them onto the solder paste-coated pads on the PCB. The machine uses computer vision and precise positioning systems to ensure accurate placement.
-
Reflow soldering: The PCB with placed components is passed through a reflow oven, which heats the board in a controlled manner. The solder paste melts, forming a permanent electrical and mechanical connection between the components and the PCB pads. The board is then cooled, solidifying the solder joints.
-
Inspection and testing: After the reflow soldering process, the assembled PCB undergoes visual inspection and automated optical inspection (AOI) to detect any manufacturing defects, such as missing components, misaligned components, or solder bridges. Electrical testing, such as in-circuit testing (ICT) or functional testing, may also be performed to ensure the proper operation of the assembled PCB.
-
Rework and repair: If defects are found during the inspection and testing phase, the PCB may undergo rework and repair. This involves removing and replacing defective components, cleaning, and resoldering.
SMT Component Packaging
SMT components are packaged in various formats to facilitate automated assembly processes:
-
Reels: SMT components, such as resistors, capacitors, and integrated circuits (ICs), are often packaged on tape and reel. The components are placed in pockets on a carrier tape, which is wound onto a reel. The pick-and-place machine feeds the tape and extracts the components for placement on the PCB.
-
Trays: Some larger or more delicate SMT components, such as connectors or certain ICs, are packaged in trays. The components are placed in individual pockets within the tray, which is loaded into the pick-and-place machine.
-
Tubes: Cylindrical SMT components, such as electrolytic capacitors, may be packaged in tubes. The components are stacked end-to-end within the tube, which is fed into the pick-and-place machine.
Applications of SMT PCB
SMT PCBs are used in a wide range of industries and applications, including:
-
Consumer electronics: Smartphones, tablets, laptops, gaming consoles, and wearable devices all rely on SMT PCBs for their compact size and high performance.
-
Automotive: Modern vehicles incorporate numerous electronic systems, such as infotainment systems, engine control units, and advanced driver assistance systems (ADAS), which are built using SMT PCBs.
-
Medical devices: SMT PCBs are used in various medical devices, including patient monitors, diagnostic equipment, and implantable devices, where reliability and miniaturization are critical.
-
Industrial automation: SMT PCBs are used in industrial control systems, sensors, and communication devices that enable automation and the Internet of Things (IoT) in manufacturing and other industries.
-
Aerospace and defense: High-reliability SMT PCBs are used in avionics, satellites, and military equipment, where they must withstand harsh environments and meet stringent performance requirements.
Challenges and Advancements in SMT PCB
While SMT PCB technology has revolutionized the electronics industry, it also presents some challenges:
-
Miniaturization limits: As components continue to shrink in size, the limits of SMT technology are being tested. Extremely small components, such as 01005 (0.4 mm x 0.2 mm) passive components, require advanced assembly equipment and processes.
-
Thermal management: With increased component density, thermal management becomes a concern. Effective heat dissipation is essential to ensure the reliability and longevity of SMT PCBs.
-
Rework and repair: Due to the small size of SMT components and the high component density, rework and repair of SMT PCBs can be challenging and time-consuming.
Despite these challenges, ongoing advancements in SMT PCB technology are addressing these issues:
-
Advanced assembly equipment: Manufacturers are developing more sophisticated pick-and-place machines, reflow ovens, and inspection systems to handle the challenges of miniaturization and high-density assembly.
-
Improved materials: New PCB materials, such as high-temperature laminates and thermally conductive substrates, are being developed to enhance thermal management in SMT PCBs.
-
3D printing: Additive manufacturing techniques, such as 3D printing of PCBs and components, are being explored as potential solutions for rapid prototyping and low-volume production of SMT PCBs.
Frequently Asked Questions (FAQ)
-
What is the difference between SMT and SMD?
SMT (Surface Mount Technology) refers to the method of assembling electronic components directly onto the surface of a PCB. SMD (Surface Mount Device) refers to the components themselves that are designed for use in SMT assembly. -
Can through-hole components be used on SMT PCBs?
Yes, through-hole components can be used on SMT PCBs, but they require additional steps in the assembly process. The through-hole components are typically inserted and soldered after the SMT components have been assembled. -
What are the most common SMT component packages?
Some of the most common SMT component packages include: - Resistors and capacitors: 0402, 0603, 0805, 1206
- ICs: SOIC, TSSOP, QFP, BGA
- Diodes: SOD-123, SOD-323
-
Transistors: SOT-23, SOT-223
-
How do I choose the right solder paste for my SMT PCB assembly?
When selecting a solder paste, consider factors such as the alloy composition (e.g., Sn63/Pb37, SAC305), particle size, flux type (e.g., rosin-based, water-soluble), and viscosity. Consult with your PCB assembly provider or solder paste manufacturer for guidance based on your specific application and requirements. -
What is the typical reflow soldering temperature profile for SMT PCB assembly?
The reflow soldering temperature profile depends on the solder paste used and the components being assembled. A typical lead-free (SAC305) reflow profile may have the following stages: - Preheat: 150-180°C for 60-90 seconds
- Soak: 180-200°C for 60-120 seconds
- Reflow: 235-250°C for 30-60 seconds
- Cooling: Gradual cooling to room temperature
Conclusion
SMT PCB technology has transformed the electronics industry, enabling the production of smaller, faster, and more cost-effective electronic devices. By understanding the fundamentals of SMT PCB, its assembly process, and its applications, engineers and designers can leverage this technology to create innovative and reliable electronic products.
As the demand for more complex and compact electronic devices continues to grow, SMT PCB technology will continue to evolve, with advancements in materials, equipment, and processes driving the future of the electronics industry.
Characteristic | Through-Hole Technology (THT) | Surface Mount Technology (SMT) |
---|---|---|
Component size | Larger | Smaller |
Circuit density | Lower | Higher |
Performance | Lower | Higher |
Manufacturing cost | Higher | Lower |
Assembly speed | Slower | Faster |