Composition of Rogers PCB Material
Rogers PCB material is a composite substrate that consists of a ceramic-filled hydrocarbon polymer laminate. The most commonly used Rogers materials are:
- RO3000 Series:
- RO3003: A ceramic-filled PTFE composite with a dielectric constant of 3.0 and a dissipation factor of 0.0013 at 10 GHz.
- RO3006: A ceramic-filled PTFE composite with a dielectric constant of 6.15 and a dissipation factor of 0.0025 at 10 GHz.
-
RO3010: A ceramic-filled PTFE composite with a dielectric constant of 10.2 and a dissipation factor of 0.0023 at 10 GHz.
-
RO4000 Series:
- RO4003C: A ceramic-filled hydrocarbon polymer with a dielectric constant of 3.38 and a dissipation factor of 0.0027 at 10 GHz.
-
RO4350B: A ceramic-filled hydrocarbon polymer with a dielectric constant of 3.48 and a dissipation factor of 0.0037 at 10 GHz.
-
RT/duroid Series:
- RT/duroid 5870: A glass microfiber-reinforced PTFE composite with a dielectric constant of 2.33 and a dissipation factor of 0.0012 at 10 GHz.
- RT/duroid 5880: A glass microfiber-reinforced PTFE composite with a dielectric constant of 2.20 and a dissipation factor of 0.0009 at 10 GHz.
The following table summarizes the key properties of some popular Rogers PCB materials:
Material | Dielectric Constant | Dissipation Factor (at 10 GHz) | Thermal Conductivity (W/m·K) |
---|---|---|---|
RO3003 | 3.00 | 0.0013 | 0.50 |
RO3006 | 6.15 | 0.0025 | 0.61 |
RO4003C | 3.38 | 0.0027 | 0.71 |
RO4350B | 3.48 | 0.0037 | 0.69 |
RT/duroid 5870 | 2.33 | 0.0012 | 0.22 |
RT/duroid 5880 | 2.20 | 0.0009 | 0.20 |
Advantages of Rogers PCB Material
Rogers PCB materials offer several advantages over traditional FR-4 substrates, making them suitable for high-frequency and high-speed applications:
-
Low Dielectric Loss: Rogers materials have low dielectric loss tangents, which minimize signal attenuation and distortion at high frequencies.
-
Consistent Dielectric Constant: The dielectric constant of Rogers materials remains stable over a wide frequency range, ensuring predictable performance.
-
Excellent Thermal Stability: Rogers materials have a low coefficient of thermal expansion (CTE), which reduces the risk of thermal stress and warping during manufacturing and operation.
-
High Mechanical Strength: Rogers materials possess high mechanical strength and durability, making them resistant to damage during handling and assembly.
-
Improved Signal Integrity: The low dielectric loss and consistent dielectric constant of Rogers materials contribute to improved signal integrity and reduced signal distortion.
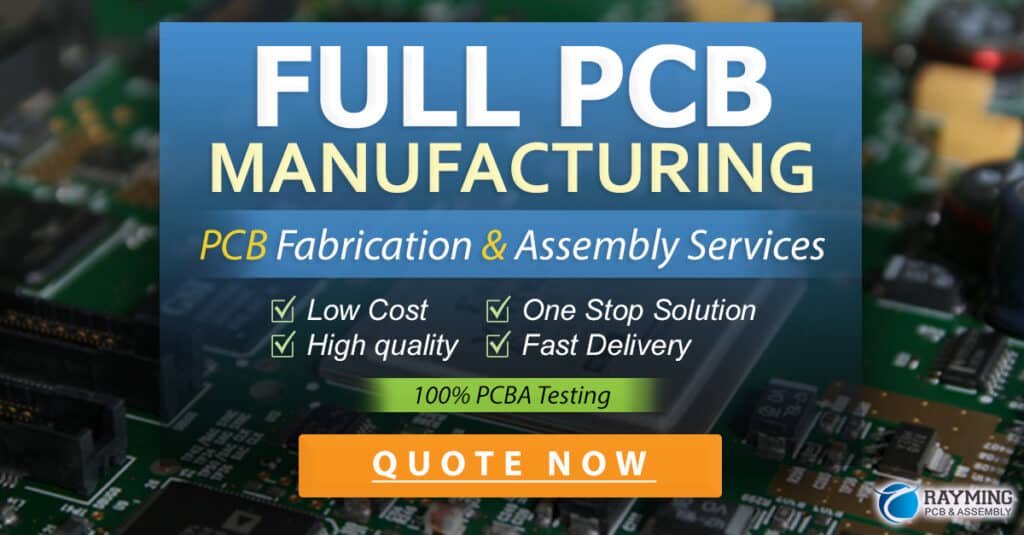
Applications of Rogers PCB Material
Rogers PCB materials find extensive use in various high-frequency and high-speed applications, such as:
- Wireless Communication Systems:
- 5G networks
- Cellular base stations
- Satellite communication
-
GPS receivers
-
Radar and Sensor Systems:
- Automotive radar
- Aerospace and defense radar
-
Medical imaging systems
-
High-Speed Digital Systems:
- High-speed data transmission
- High-performance computing
-
Data centers and servers
-
Microwave and Millimeter-Wave Devices:
- Microwave antennas
- Millimeter-wave transceivers
-
Microwave filters and couplers
-
Aerospace and Defense Electronics:
- Avionics systems
- Missile guidance systems
- Radar countermeasures
Frequently Asked Questions (FAQ)
-
Q: What is the main difference between Rogers PCB material and FR-4?
A: Rogers PCB materials have lower dielectric loss, more consistent dielectric constant, and better thermal stability compared to FR-4. These properties make Rogers materials suitable for high-frequency and high-speed applications where signal integrity is critical. -
Q: Can Rogers PCB material be used for multilayer PCBs?
A: Yes, Rogers PCB materials can be used for multilayer PCBs. The low dielectric loss and consistent dielectric constant of Rogers materials make them suitable for high-frequency signal routing in multilayer structures. -
Q: How does the cost of Rogers PCB material compare to traditional FR-4?
A: Rogers PCB materials are generally more expensive than FR-4 due to their specialized composition and superior electrical properties. However, the improved performance and reliability offered by Rogers materials can justify the higher cost in critical applications. -
Q: What are the challenges in manufacturing PCBs with Rogers material?
A: Manufacturing PCBs with Rogers material requires specialized equipment and processes due to the material’s unique properties. Challenges include the need for precise temperature control during lamination, careful handling to avoid damage, and the use of compatible adhesives and surface finishes. -
Q: Can Rogers PCB material be used for flexible PCBs?
A: While Rogers materials are primarily used for rigid PCBs, some specialized Rogers products, such as the RO3000 series, can be used for flexible PCBs. These materials offer the benefits of low dielectric loss and consistent dielectric constant in flexible form factors.
Conclusion
Rogers PCB material is a high-performance substrate that offers superior electrical properties, thermal stability, and mechanical strength compared to traditional PCB materials. Its composition, which includes ceramic-filled hydrocarbon polymers and PTFE composites, enables its use in demanding high-frequency and high-speed applications.
The low dielectric loss, consistent dielectric constant, and excellent thermal stability of Rogers materials make them ideal for applications such as wireless communication systems, radar and sensor systems, high-speed digital systems, and microwave and millimeter-wave devices.
While Rogers PCB materials may come at a higher cost and require specialized manufacturing processes, their enhanced performance and reliability justify their use in critical applications where signal integrity and reliability are paramount.
As technology continues to advance and the demand for high-frequency and high-speed electronics grows, Rogers PCB materials will likely play an increasingly important role in enabling the next generation of electronic devices and systems.