The Importance of PCBs in Modern Electronics
PCBs are the backbone of modern electronics. They provide a reliable and efficient means of connecting electronic components, allowing for the creation of complex circuits in a compact form factor. PCBs are used in a wide range of applications, including:
- Consumer electronics (smartphones, laptops, televisions)
- Automotive electronics (infotainment systems, engine control units)
- Medical devices (imaging equipment, patient monitors)
- Industrial equipment (process control systems, automation devices)
- Aerospace and defense systems (avionics, communication devices)
The demand for PCBs has grown significantly in recent years, driven by the increasing complexity and miniaturization of electronic devices. As a result, the role of PCB fabricators has become increasingly important in the electronics industry.
The PCB Fabrication Process
The PCB fabrication process involves several steps, each of which requires specialized equipment and expertise. The main stages of PCB fabrication are:
- PCB Design
- PCB Fabrication
- PCB Assembly
- Testing and Quality Control
PCB Design
The PCB fabrication process begins with the design of the PCB. This involves creating a schematic diagram of the circuit and a layout of the PCB. The schematic diagram shows the electrical connections between the components, while the layout shows the physical arrangement of the components on the PCB.
PCB design is typically done using specialized software, such as Altium Designer, Eagle, or KiCad. These software tools allow designers to create complex circuits and layouts quickly and accurately. The design process involves several key considerations, including:
- Component selection and placement
- Signal integrity and electromagnetic compatibility
- Thermal management
- Manufacturing constraints (minimum trace width, hole size, etc.)
Once the design is complete, it is sent to the PCB fabricator for manufacturing.
PCB Fabrication
The PCB fabrication process involves several steps, each of which is critical to the quality and reliability of the final product. The main steps in PCB fabrication are:
- Substrate preparation
- Copper deposition
- Photolithography
- Etching
- Drilling
- Plating
- Solder mask application
- Silkscreen printing
Substrate Preparation
The substrate is the base material of the PCB, typically made of a flame-retardant material such as FR-4. The substrate is cut to the required size and shape, and any necessary holes are drilled.
Copper Deposition
A thin layer of copper is deposited onto the substrate using a process called electroless plating. This layer of copper will form the conductive traces on the PCB.
Photolithography
A photosensitive resist is applied to the copper layer, and a photomask is used to expose the resist to UV light. The exposed areas of the resist are then removed, leaving a pattern of copper traces on the substrate.
Etching
The exposed copper is etched away using a chemical solution, leaving only the desired copper traces on the substrate.
Drilling
Holes are drilled through the PCB to allow for the mounting of components and the creation of vias (connections between layers).
Plating
The holes are plated with copper to create electrical connections between layers. Additional layers of copper may be added to increase the current-carrying capacity of the traces.
Solder Mask Application
A solder mask is applied to the PCB to protect the copper traces and prevent short circuits. The solder mask is typically green, but other colors are available.
Silkscreen Printing
Text and symbols are printed onto the PCB using a silkscreen process. This allows for easy identification of components and provides a professional appearance to the final product.
PCB Assembly
Once the PCB has been fabricated, it is ready for assembly. This involves mounting the electronic components onto the PCB and soldering them in place. There are two main methods of PCB assembly:
- Through-hole assembly
- Surface-mount assembly
Through-Hole Assembly
Through-hole assembly involves inserting the leads of the components through holes in the PCB and soldering them in place on the opposite side. This method is typically used for larger components and is more labor-intensive than surface-mount assembly.
Surface-Mount Assembly
Surface-mount assembly involves placing the components directly onto pads on the surface of the PCB and soldering them in place. This method allows for smaller components and higher component density than through-hole assembly.
PCB assembly can be done manually or using automated equipment. Automated assembly is typically used for high-volume production, while manual assembly is used for prototypes and low-volume production.
Testing and Quality Control
After the PCB has been assembled, it must be tested to ensure that it functions correctly and meets the required specifications. Testing typically involves several steps, including:
- Visual inspection
- Electrical testing
- Functional testing
- Environmental testing
Visual Inspection
The PCB is inspected visually for any defects, such as incorrect component placement, solder bridges, or damaged components.
Electrical Testing
The PCB is tested electrically to ensure that all connections are correct and that there are no short circuits or open circuits. This is typically done using automated test equipment (ATE).
Functional Testing
The PCB is tested to ensure that it performs the intended function correctly. This may involve testing the PCB in the final product or using specialized test equipment.
Environmental Testing
The PCB may be subjected to environmental testing to ensure that it can withstand the expected operating conditions. This may include testing for temperature, humidity, vibration, and shock.
Quality control is an essential part of the PCB fabrication process. PCB fabricators use a variety of techniques to ensure the quality of their products, including:
- Statistical process control (SPC)
- Failure mode and effects analysis (FMEA)
- Six Sigma methodologies
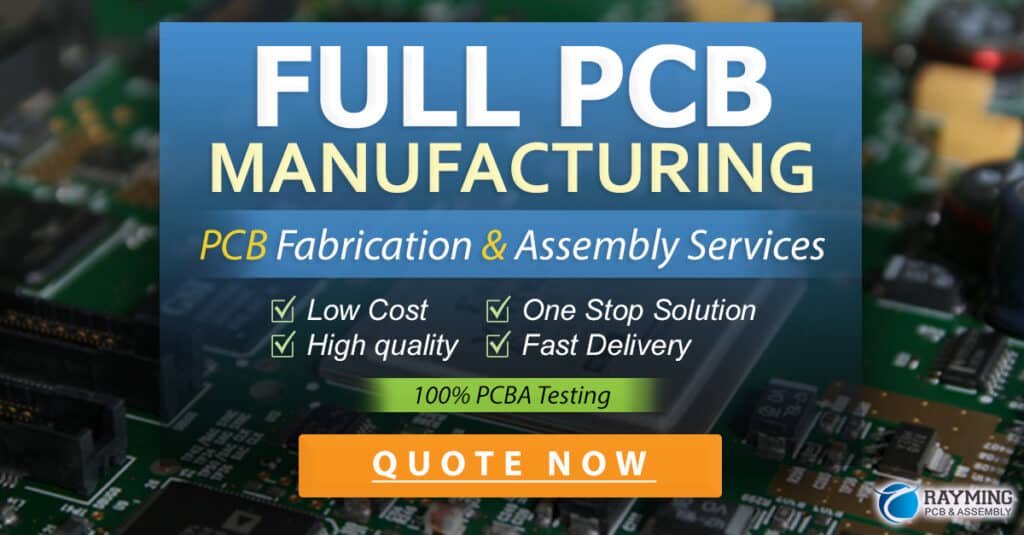
Technologies Used in PCB Fabrication
PCB fabricators use a variety of technologies to create high-quality PCBs efficiently and cost-effectively. Some of the key technologies used in PCB fabrication include:
Computer-Aided Design (CAD) Software
CAD software is used to create the schematic diagrams and layouts for PCBs. This software allows designers to create complex circuits quickly and accurately, and to simulate the performance of the PCB before it is manufactured.
Computer-Aided Manufacturing (CAM) Software
CAM software is used to generate the machine code needed to control the manufacturing equipment used in PCB fabrication. This software takes the PCB design files and converts them into instructions for the manufacturing equipment, such as drill files and Gerber files.
Computer Numerical Control (CNC) Equipment
CNC equipment is used to automate many of the manufacturing processes involved in PCB fabrication, such as drilling, routing, and milling. This equipment allows for high precision and repeatability, reducing the risk of errors and improving the overall quality of the PCB.
Automated Optical Inspection (AOI) Equipment
AOI equipment is used to inspect PCBs for defects automatically. This equipment uses cameras and image processing software to detect defects such as missing components, incorrect component placement, and solder defects.
Flying Probe Testing (FPT) Equipment
FPT equipment is used to test PCBs for electrical defects automatically. This equipment uses probes to contact the test points on the PCB and measure the electrical characteristics of the circuit. This allows for rapid testing of PCBs without the need for custom test fixtures.
Benefits of Working with a Professional PCB Fabricator
Working with a professional PCB fabricator offers several benefits, including:
- Expertise and experience
- Access to advanced technologies
- Faster time-to-market
- Cost-effectiveness
- Quality assurance
A professional PCB fabricator has the expertise and experience needed to create high-quality PCBs efficiently and cost-effectively. They have access to advanced technologies and equipment that may not be available to individual designers or small businesses. This allows them to create PCBs faster and with higher quality than would be possible in-house.
Working with a professional PCB fabricator also allows for faster time-to-market. The fabricator can handle all aspects of the manufacturing process, from design to assembly, allowing the customer to focus on their core business. This can be particularly important for companies that need to bring new products to market quickly to stay competitive.
Finally, a professional PCB fabricator can provide quality assurance through rigorous testing and quality control processes. This ensures that the PCBs meet the required specifications and are free from defects, reducing the risk of product failures and returns.
Choosing the Right PCB Fabricator
Choosing the right PCB fabricator is essential to ensure the success of your project. When selecting a PCB fabricator, consider the following factors:
- Experience and expertise
- Quality control processes
- Capabilities and technologies
- Turnaround time
- Cost
Look for a PCB fabricator with experience and expertise in your specific industry or application. Check their quality control processes to ensure that they meet your requirements for reliability and performance. Consider their capabilities and technologies to ensure that they can handle your specific PCB design and manufacturing needs.
Turnaround time is also an important factor, particularly if you have tight deadlines. Look for a PCB fabricator that can meet your schedule without compromising on quality. Finally, consider the cost of the PCB fabrication services. While cost is important, it should not be the only factor in your decision. Look for a PCB fabricator that offers a good balance of quality, turnaround time, and cost.
Frequently Asked Questions (FAQ)
- What is the typical turnaround time for PCB fabrication?
-
The typical turnaround time for PCB fabrication varies depending on the complexity of the design and the fabricator’s workload. Simple PCBs can be fabricated in as little as 24 hours, while more complex designs may take several weeks.
-
What is the minimum order quantity for PCB fabrication?
-
The minimum order quantity for PCB fabrication varies depending on the fabricator and the complexity of the design. Some fabricators may have a minimum order quantity of 1 or 2 PCBs, while others may require a minimum order of 100 or more.
-
What file formats are typically required for PCB fabrication?
-
The file formats typically required for PCB fabrication include Gerber files (for the PCB layout), drill files (for the hole locations), and BOM files (for the bill of materials). Some fabricators may also require additional files, such as pick-and-place files or 3D models.
-
What materials are used in PCB fabrication?
-
The most common materials used in PCB fabrication are FR-4 (a flame-retardant glass-reinforced epoxy laminate), polyimide (a high-temperature plastic), and PTFE (polytetrafluoroethylene, also known as Teflon). Other materials, such as aluminum or copper-clad laminates, may be used for specific applications.
-
How can I ensure the quality of my PCB fabrication?
- To ensure the quality of your PCB fabrication, work with a reputable PCB fabricator that has experience in your industry or application. Provide clear and accurate design files, and communicate your requirements for quality and reliability. Consider using a fabricator that offers automated inspection and testing to detect defects and ensure that the PCBs meet your specifications.
Step | Description |
---|---|
PCB Design | Create schematic diagram and layout using CAD software |
Substrate Preparation | Cut substrate to size and drill holes |
Copper Deposition | Deposit thin layer of copper onto substrate using electroless plating |
Photolithography | Apply photosensitive resist, expose to UV light through photomask, and remove exposed resist |
Etching | Etch away exposed copper using chemical solution |
Drilling | Drill holes through PCB for component mounting and vias |
Plating | Plate holes with copper to create electrical connections, add additional copper layers if needed |
Solder Mask Application | Apply solder mask to protect copper traces and prevent short circuits |
Silkscreen Printing | Print text and symbols onto PCB using silkscreen process |
PCB Assembly | Mount electronic components onto PCB and solder in place (through-hole or surface-mount) |
Testing and Quality Control | Perform visual inspection, electrical testing, functional testing, and environmental testing |
Conclusion
PCB fabrication is a complex process that requires specialized equipment, expertise, and attention to detail. By understanding the steps involved in PCB fabrication and the technologies used by PCB fabricators, designers can create PCBs that meet their specific requirements for performance, reliability, and cost.
Working with a professional PCB fabricator offers several benefits, including access to advanced technologies, faster time-to-market, and quality assurance. When selecting a PCB fabricator, consider their experience, capabilities, turnaround time, and cost to ensure that they can meet your specific needs.
As the demand for PCBs continues to grow, driven by the increasing complexity and miniaturization of electronic devices, the role of PCB fabricators will become increasingly important. By staying up-to-date with the latest technologies and best practices in PCB fabrication, designers and manufacturers can create innovative and reliable electronic products that meet the needs of today’s market.