What is Flux?
Flux is a chemical agent used in the soldering process to remove oxides and other contaminants from the surfaces of the metal parts being soldered. It promotes the wetting of the solder to the metal surfaces, allowing for a strong and reliable bond between the components and the PCB.
Types of Flux
There are three main types of flux used in PCB assembly:
-
Rosin Flux: This is the most common type of flux used in PCB soldering. It is made from the sap of pine trees and is available in various activity levels, such as mild, activated, and highly activated. Rosin flux is known for its excellent wetting properties and provides a strong, reliable bond between components and the PCB.
-
Water-Soluble Flux: As the name suggests, this type of flux is soluble in water and can be easily cleaned after the soldering process. It is typically used in applications where cleanliness is a top priority, such as in the manufacturing of medical devices or aerospace components.
-
No-Clean Flux: This type of flux is designed to leave minimal residue after the soldering process, eliminating the need for post-soldering cleaning. No-clean flux is popular in high-volume PCB assembly as it reduces the time and cost associated with cleaning.
Flux Type | Characteristics | Applications |
---|---|---|
Rosin Flux | Excellent wetting properties, strong bond | General PCB assembly |
Water-Soluble Flux | Easily cleaned with water | Medical devices, aerospace components |
No-Clean Flux | Minimal residue, no post-soldering cleaning required | High-volume PCB assembly |
The Role of Flux in PCB Assembly
Flux plays a vital role in the PCB assembly process by:
-
Removing Oxides: When exposed to air, the metal surfaces of components and PCB pads develop a layer of oxide. This oxide layer hinders the proper wetting of the solder, resulting in poor solder joints. Flux removes these oxides, allowing for better solder wetting and a stronger bond.
-
Promoting Solder Wetting: Flux improves the wetting properties of the solder, enabling it to flow easily and evenly over the metal surfaces. This ensures a strong and reliable connection between the components and the PCB.
-
Preventing Reoxidation: During the soldering process, flux creates a protective barrier that prevents the metal surfaces from reoxidizing. This is particularly important when soldering temperature-sensitive components, as it allows for lower soldering temperatures and reduces the risk of component damage.
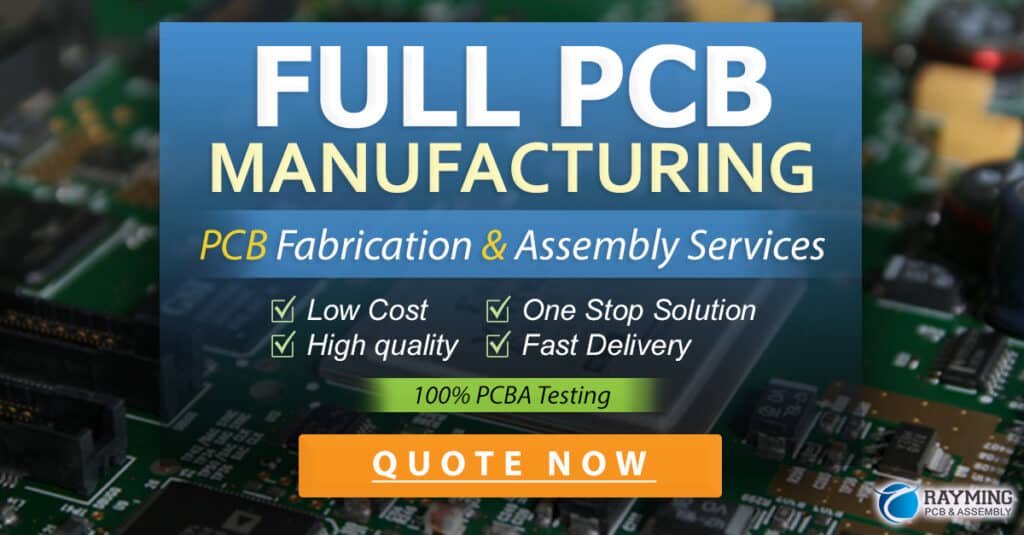
Choosing the Right Flux for Your PCB Assembly
When selecting a flux for your PCB assembly process, consider the following factors:
-
PCB Application: The type of flux used depends on the specific requirements of your PCB application. For example, medical devices and aerospace components may require the use of water-soluble flux for enhanced cleanliness, while high-volume consumer electronics may benefit from the use of no-clean flux to reduce production time and costs.
-
Soldering Method: The choice of flux also depends on the soldering method employed. Wave soldering, selective soldering, and hand soldering each have different flux requirements. For instance, wave soldering typically uses a more active flux to ensure proper solder wetting, while hand soldering may use a milder flux to reduce the risk of component damage.
-
Environmental Considerations: The environmental impact of the flux should also be taken into account. Some fluxes contain volatile organic compounds (VOCs) that can be harmful to the environment and human health. In recent years, there has been a trend towards the use of more environmentally friendly fluxes, such as water-based and low-VOC formulations.
Proper Flux Application Techniques
To ensure optimal results, it is essential to apply flux correctly during the PCB assembly process. Here are some best practices for flux application:
-
Use the Right Amount: Applying too little flux can result in poor solder wetting and weak solder joints, while applying too much flux can lead to excessive residue and potential reliability issues. Follow the manufacturer’s recommendations for the appropriate amount of flux to use.
-
Apply Evenly: Flux should be applied evenly across the PCB surface to ensure consistent solder wetting. Uneven flux application can result in inconsistent solder joint quality and potential reliability issues.
-
Use the Right Application Method: There are various methods for applying flux, including spray, foam, and brush application. Choose the method that best suits your PCB assembly process and ensures even coverage.
-
Monitor Flux Activity: Flux activity can degrade over time due to exposure to air and heat. Monitor the activity level of your flux regularly and replace it as needed to ensure optimal performance.
Flux Residue and Cleaning
After the soldering process, flux residue may remain on the PCB surface. Depending on the type of flux used and the application requirements, this residue may need to be cleaned. Here are some considerations for flux residue and cleaning:
-
Rosin Flux: Rosin flux residue is non-conductive and can be left on the PCB surface in most applications. However, in some cases, such as when conformal coating is required, the residue must be removed using solvents or other cleaning methods.
-
Water-Soluble Flux: Water-soluble flux residue is conductive and must be removed after soldering. This is typically done using deionized water in a batch or inline cleaning process.
-
No-Clean Flux: As the name suggests, no-clean flux is designed to leave minimal residue that does not require cleaning. However, in some applications, such as those with strict cleanliness requirements, even no-clean flux residue may need to be removed.
FAQ
-
Q: What is the difference between active and passive flux?
A: Active flux contains activators that aggressively remove oxides from metal surfaces, while passive flux relies on the heat of the soldering process to remove oxides. Active flux is typically used in applications where the metal surfaces are heavily oxidized, while passive flux is used in applications where the metal surfaces are relatively clean. -
Q: Can I use the same flux for all soldering applications?
A: No, different soldering applications may require different types of flux. For example, wave soldering typically requires a more active flux than hand soldering. It is essential to choose the right flux for your specific application to ensure optimal results. -
Q: How do I know when to replace my flux?
A: Flux activity can degrade over time due to exposure to air and heat. If you notice a decrease in solder wetting or an increase in solder defects, it may be time to replace your flux. Regularly monitoring flux activity and following the manufacturer’s recommendations for storage and handling can help extend the life of your flux. -
Q: Can I mix different types of flux?
A: Mixing different types of flux is not recommended, as it can lead to unpredictable results and potential reliability issues. Always use the flux type specified for your application and follow the manufacturer’s recommendations for usage and storage. -
Q: What are some common flux-related defects in PCB assembly?
A: Common flux-related defects include poor solder wetting, solder bridges, and flux residue contamination. These defects can be caused by using the wrong type of flux, applying too much or too little flux, or failing to clean flux residue when required. Proper flux selection, application, and cleaning can help prevent these defects and ensure reliable PCB assembly.
Conclusion
Flux PCB is a critical component in the PCB assembly process, ensuring proper solder wetting and strong, reliable solder joints. Understanding the different types of flux, their applications, and proper usage techniques is essential for achieving optimal results in your PCB assembly process. By choosing the right flux for your application, applying it correctly, and properly managing flux residue and cleaning, you can ensure the production of high-quality, reliable PCBs.
As the electronics industry continues to evolve, so too do the fluxes used in PCB assembly. Advances in flux technology, such as the development of low-VOC and halogen-free formulations, are helping to address environmental and health concerns while still providing the performance required for reliable PCB assembly.
By staying up-to-date with the latest developments in flux technology and best practices for usage and handling, PCB manufacturers can ensure that they are producing high-quality, reliable products that meet the evolving needs of their customers.