Overview of the PCB Assembly Process
The typical PCB assembly process flow includes:
- PCB Fabrication: Manufacturing the bare printed circuit board substrate
- Solder Paste Application: Applying solder paste to component pads via stencil printing
- Component Placement: Mounting components onto the PCB
- Reflow Soldering: Melting the solder paste to form permanent solder joints
- Inspection and Testing: Verifying proper assembly and functionality of the PCB
- Cleaning: Removing any solder flux residue from the board
- Final Inspection and Packaging: Final quality checks and packaging for shipment
Let’s explore each of these steps in more detail.
PCB Fabrication
Before components can be assembled, the bare PCB must first be fabricated. This starts with the PCB design, which defines the copper traces, pads, vias, and overall board shape.
The fabrication process typically involves the following sub-steps:
-
Inner layer printing: Copper foil is laminated onto the core PCB substrate material. The copper is then etched away to form inner circuit traces as defined by the design data.
-
Layer alignment and bonding: Multiple inner layers are stacked and laminated together under heat and pressure. Holes are drilled through the stack where vias and through-holes will be located.
-
Outer layer printing: Copper foil is laminated onto the outer layers of the bonded stack. Again, unwanted copper is etched away to form circuit traces, pads, and planes.
-
PCB finish application: A surface finish, such as ENIG (Electroless Nickel Immersion Gold), is applied to the exposed copper to prevent oxidation and enhance solderability.
-
Silkscreen and solder mask: A solder mask is applied over the outer layers, leaving only the pads and SMT lands exposed. A silkscreen layer is printed to add component identifiers and polarity marks.
-
Routing and scoring: The fabricated panel is routed or v-scored to singulate individual PCBs.
The output of this process is the bare PCB, ready for assembly.
Solder Paste Application
In surface mount assembly, the first step is to apply solder paste to the component pads. Solder paste is a mixture of tiny solder spheres (typically a tin-silver-copper alloy), flux, and other additives. It is the “glue” that will physically and electrically bond the components to the PCB.
The most common method for solder paste application is stencil printing:
-
A laser-cut stainless steel stencil is aligned over the PCB. The stencil has openings that match the component pads.
-
Solder paste is dispensed onto the stencil and a squeegee blade is used to spread the paste across the stencil surface. This forces paste through the openings and onto the pads.
-
The stencil is lifted away, leaving precise deposits of solder paste on each pad.
Proper control of the stencil design, paste rheology, and printing parameters is critical to achieve the right solder paste volume and avoid defects like bridging or insufficient deposits.
Component Placement
With solder paste applied, the PCB is ready for component placement. This is typically done with automated pick-and-place (P&P) machines, although smaller volumes may be placed by hand.
P&P machines use vacuum nozzles to pick up individual components from feeders or trays and place them onto their respective pads on the PCB. They are programmed with the PCB design data to know the exact XY coordinates of each component.
Some key aspects of the placement process include:
-
Feeder setup: Reels, trays, and sticks of components are loaded into the P&P machine. Each feeder slot is programmed with the component part number to ensure the right part is placed in the right location.
-
Fiducial recognition: The P&P machine uses fiducial marks on the PCB to align its coordinate system and compensate for any slight board warp or skew. This ensures components are placed accurately.
-
Placement inspection: Modern P&P machines have 2D and/or 3D cameras to inspect components after placement. This allows them to identify missing or misaligned parts before soldering.
After placement, the PCB is transferred to a reflow oven for soldering.
Reflow Soldering
Reflow soldering is the process of heating the PCB assembly to melt the solder paste and form permanent solder joints. This is done in a controlled conveyor oven with multiple temperature zones.
A typical reflow oven temperature profile looks like this:
Zone | Temperature (°C) | Time (seconds) |
---|---|---|
Preheat | 150-180 | 60-120 |
Soak | 180-200 | 60-120 |
Reflow | 230-250 | 30-60 |
Cooling | < 100 | 30-60 |
The key steps in the reflow process are:
-
Preheat: The board is gradually heated to activate the flux and begin evaporating solvents from the solder paste.
-
Soak: The board temperature is held steady to allow any remaining volatiles to escape and ensure even heating across the board.
-
Reflow: The temperature is ramped up above the melting point of the solder alloy, typically to 20-40°C above liquidus. This allows the molten solder to wet to the pads and component leads.
-
Cooling: The board is cooled, allowing the molten solder to solidify into permanent intermetallic bonds.
Precise control of conveyor speed, zone temperatures, and airflow is essential for a reliable soldering process. The reflow profile must be tailored to the thermal mass of the board, component types, and solder paste specifications.
Inspection and Testing
After reflow, the assembled PCBs go through an inspection and testing process to verify proper assembly and functionality. Common inspection methods include:
-
Visual Inspection: Inspectors use magnifying optics to visually check for solder joint defects, component placement, and general workmanship.
-
Automated Optical Inspection (AOI): An AOI machine scans the PCB and uses computer vision algorithms to compare it to the expected design. It can rapidly identify missing components, solder bridges, insufficient solder, and other defects.
-
X-Ray Inspection: X-ray imaging allows inspection of solder joints hidden underneath components, such as BGA and QFN packages.
Functional circuit testing is also critical to verify that the assembled PCB performs as intended. This can include:
-
In-Circuit Testing (ICT): An ICT fixture makes contact with test points on the board and performs a series of analog and digital measurements to verify component values, connectivity, and basic functionality.
-
Functional Testing: The PCB is powered on and put through its paces to ensure it functions as specified across various operating modes and conditions. This may involve the use of automated test equipment (ATE) or manual testing procedures.
Boards that fail inspection or testing may be reworked or scrapped, depending on the nature and severity of the defect.
Cleaning
After soldering, solder flux residues may be left on the PCB surface. While some modern no-clean fluxes may not require removal, many assemblies still undergo a cleaning process to remove any contaminants.
The most common PCB cleaning methods are:
-
Aqueous cleaning: The PCB is washed with a mixture of deionized water and saponifying agents in a spray or immersion system.
-
Semi-aqueous cleaning: Similar to aqueous cleaning but uses a water-soluble organic solvent in place of the saponifier.
-
Solvent cleaning: The PCB is washed in a pure organic solvent, such as isopropyl alcohol, to dissolve and remove flux residues.
After cleaning, the boards are dried and ready for final inspection.
Final Inspection and Packaging
A final visual inspection is typically performed on the cleaned assemblies to check for any handling damage or leftover contaminants. Boards are then packaged for shipment, which may involve:
-
ESD bagging: Each board is sealed in an antistatic bag to protect it from electrostatic discharge (ESD) damage.
-
Vacuum sealing: Boards may be vacuum sealed in moisture barrier bags with desiccant packs for added protection against moisture and contaminants.
-
Bulk packaging: Individual bags are packed in boxes or crates for shipment. Proper cushioning and labeling are used to protect boards in transit.
The packaged PCBs are then ready for shipment to the end customer or next higher level of product assembly.
Benefits of Automated PCB Assembly
Automated PCB assembly offers numerous benefits over manual assembly methods:
-
Speed: Automated P&P machines and reflow ovens can assemble boards much faster than human operators, enabling higher throughput.
-
Precision: Machines can place components with extremely high accuracy and repeatability, down to a few microns in some cases. This allows reliable assembly of high-density designs.
-
Consistency: Automated processes are highly repeatable, ensuring consistent quality from board to board and lot to lot.
-
Flexibility: Modern assembly equipment can handle a wide range of component types and sizes, from tiny 0201 passives to large BGA packages. Changeovers between different board types are also relatively quick.
-
Traceability: Automated systems can generate detailed logs of every placement, reflow, and inspection step for each unique board. This enables traceability in case of quality issues.
While automated assembly requires higher upfront investment in equipment and programming, it is essential for most medium- to high-volume PCB production.
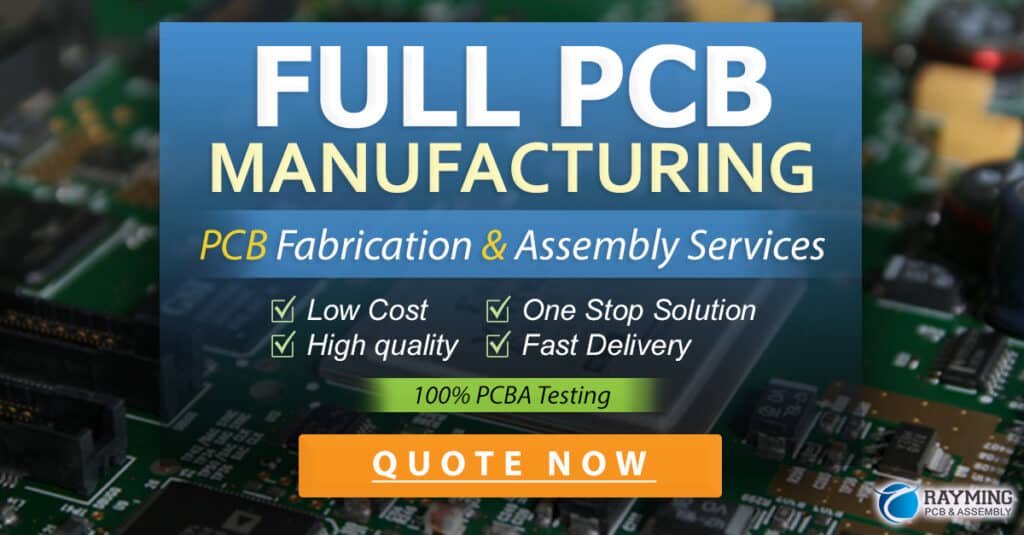
Design for Manufacturing (DFM) Considerations
To ensure a smooth and reliable PCB assembly process, it’s important to consider Design for Manufacturing (DFM) principles during the PCB design phase. Some key DFM considerations include:
-
Component selection: Choose components that are compatible with your assembly processes and equipment. Avoid obsolete or hard-to-source parts.
-
Footprint design: Ensure component footprints have the correct pad sizes and shapes for reliable soldering. Provide adequate spacing between components for placement and inspection.
-
Panelization: Design boards that can be efficiently panelized for fabrication and assembly. Use mouse bites or v-score breakaway tabs for easy depanelization.
-
Solder mask and silkscreen: Ensure solder mask openings are sized correctly for the pads and SMT lands. Provide clear and accurate silkscreen markings for polarity and reference designators.
-
Testability: Include test points and probe access on the board for in-circuit and functional testing. Provide clear labeling for test points and connector pinouts.
By collaborating closely with your pcb fabrication and assembly partners and following DFM best practices, you can minimize assembly issues and improve overall manufacturing yields.
Conclusion
Electronic PCB assembly is a complex multi-step process that turns a bare circuit board into a functional electronic product. From solder paste application to component placement to reflow soldering and inspection, each step must be carefully controlled to ensure reliable and high-quality results.
Automated assembly processes offer significant advantages in speed, precision, consistency, and flexibility compared to manual methods. However, proper DFM and close collaboration between design and manufacturing teams are essential for success.
As electronic products continue to evolve in complexity and miniaturization, innovations in PCB assembly technologies and processes will be key to enabling the next generation of devices. From 5G smartphones to self-driving cars to industrial IoT, the humble PCB remains the backbone of our increasingly connected world.
FAQ
- Q: What is the difference between through-hole and surface mount assembly?
A: Through-hole assembly involves inserting component leads through drilled holes in the PCB and soldering them to pads on the opposite side. Surface mount assembly places components directly onto pads on the PCB surface and solder them in place using a reflow oven. Surface mount is generally faster, more space-efficient, and allows higher component density compared to through-hole.
- Q: What is a stencil and why is it used in PCB assembly?
A: A stencil is a thin metal sheet with laser-cut openings that match the component pads on the PCB. It is used to apply solder paste to the pads prior to component placement. The stencil ensures a precise and consistent amount of solder paste is deposited on each pad, which is critical for reliable soldering.
- Q: How are PCBs tested after assembly?
A: PCBs typically undergo several types of testing after assembly to verify proper functionality and workmanship. These can include automated optical inspection (AOI) to check for component placement and solder defects, X-ray inspection for hidden solder joints, in-circuit testing (ICT) to verify component values and connectivity, and functional testing to ensure the board performs as intended under various operating conditions.
- Q: What is a reflow oven and how does it work?
A: A reflow oven is a controlled heating chamber used to melt and solidify solder paste to form permanent solder joints between components and PCB pads. The oven has multiple temperature zones that the PCB passes through on a conveyor belt. The temperature profile is carefully controlled to preheat the board, activate the solder flux, melt the solder, and then cool the board back down to room temperature.
- Q: What are some common PCB assembly defects to watch out for?
A: Some common PCB assembly defects include:
- Solder bridges: Unintended solder connections between adjacent pads or traces
- Cold solder joints: Weak, grainy solder joints that result from insufficient heat or poor wetting
- Tombstoning: One end of a component lifts off the pad due to uneven heating or pad design
- Component skew: Components rotated or misaligned from their intended orientation
- Insufficient or excessive solder: Too little or too much solder paste applied to the pads
Proper DFM, process control, and post-assembly inspection can help identify and correct these issues.