What is Castellation?
Castellation refers to the process of creating small, semicircular or rectangular cuts along the edges of a PCB. These cuts, known as castellations, serve as electrical contacts and mechanical support points for the board. They allow the PCB to be easily connected to other boards or components through soldering or other means of attachment.
Types of Castellation
There are two main types of castellation used in PCB design:
-
Half-hole Castellation: In this type, the castellations are created by drilling half-holes along the edges of the PCB. The holes are typically plated with a conductive material, such as copper, to enable electrical connectivity. Half-hole castellation is commonly used for through-hole mounting of components.
-
Surface-mount Castellation: Surface-mount castellation involves creating rectangular or semicircular cuts along the edges of the PCB without drilling through the board. The castellation pads are exposed on both sides of the PCB, allowing for surface-mount soldering. This type of castellation is often used for connecting modules or boards in a stackable configuration.
Benefits of Castellation in PCB Design
Castellation offers several advantages in PCB design and manufacturing:
-
Improved Connectivity: Castellations provide a reliable and efficient means of connecting PCBs to other boards or components. They allow for easy soldering and ensure a strong mechanical and electrical connection.
-
Space Savings: By using castellation, PCBs can be designed with smaller footprints. The castellated edges eliminate the need for additional connectors or mounting hardware, reducing the overall size of the board and saving valuable space in electronic devices.
-
Enhanced Mechanical Strength: Castellation adds mechanical strength to the PCB, particularly at the edges. The castellated cuts distribute stress evenly along the board’s perimeter, reducing the risk of damage during handling or operation.
-
Simplified Assembly: Castellated PCBs are easier to assemble compared to boards with traditional connectors. The castellations allow for direct soldering of components or other boards, streamlining the assembly process and reducing manufacturing time and costs.
-
Versatility: Castellation enables various interconnection options, such as board-to-board stacking, edge-to-edge connection, or module integration. This versatility makes castellated PCBs suitable for a wide range of applications, from consumer electronics to industrial systems.
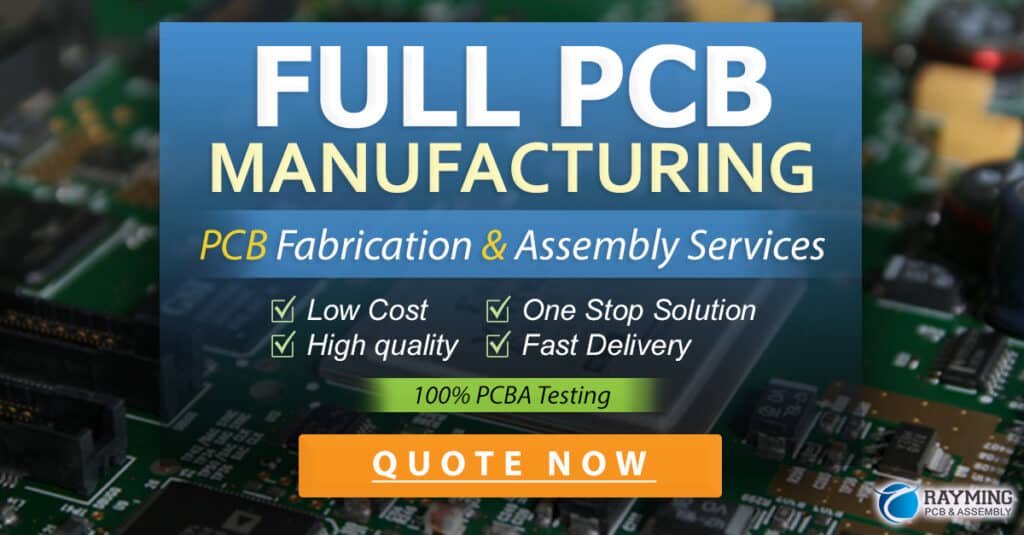
Implementing Castellation in PCB Manufacturing
To incorporate castellation in PCB manufacturing, several steps are involved:
-
PCB Design: The PCB design must include the castellation features along the edges of the board. The designer specifies the size, shape, and spacing of the castellations based on the requirements of the project.
-
Drilling: If half-hole castellation is used, the PCB undergoes a drilling process to create the holes along the edges. The drilling is precisely controlled to ensure accurate hole placement and size.
-
Plating: After drilling, the castellations are plated with a conductive material, typically copper. The plating process ensures electrical conductivity and provides a surface for soldering.
-
Routing: For surface-mount castellation, the PCB undergoes a routing process to create the rectangular or semicircular cuts along the edges. The routing is performed using specialized equipment to ensure precise and consistent castellation profiles.
-
Solder Mask Application: A solder mask is applied to the PCB, covering the areas that should not be exposed to solder. The solder mask is selectively removed from the castellation pads to allow for soldering.
-
Surface Finish: The PCB receives a surface finish, such as HASL (Hot Air Solder Leveling), ENIG (Electroless Nickel Immersion Gold), or OSP (Organic Solderability Preservative). The surface finish protects the copper and enhances the solderability of the castellation pads.
Castellation Design Considerations
When designing a PCB with castellation, several factors should be considered:
-
Castellation Size and Spacing: The size and spacing of the castellations depend on the specific requirements of the project. The designer must ensure that the castellations are large enough to provide sufficient mechanical strength and electrical contact, while also maintaining proper spacing to prevent shorts or interference.
-
PCB Thickness: The thickness of the PCB affects the depth of the castellations. Thicker boards may require deeper castellations to ensure adequate mechanical support and electrical connectivity.
-
Component Placement: The placement of components on the PCB should be considered in relation to the castellation. Adequate clearance must be provided between the components and the castellated edges to avoid interference and ensure proper assembly.
-
Solder Mask and Pad Design: The solder mask and pad design around the castellations should be carefully planned. The solder mask should be properly aligned with the castellation pads to prevent solder bridging or insufficient coverage. The pad size and shape should be optimized for reliable soldering and mechanical strength.
-
Manufacturing Capabilities: The PCB manufacturer’s capabilities and limitations should be taken into account when designing castellation. Different manufacturers may have specific requirements or restrictions regarding castellation size, spacing, and tolerances. It is important to communicate with the manufacturer early in the design process to ensure feasibility and manufacturability.
Applications of Castellated PCBs
Castellated PCBs find applications in various industries and product categories:
-
Consumer Electronics: Castellated PCBs are commonly used in consumer electronic devices, such as smartphones, tablets, and wearables. They enable compact and modular designs, allowing for easy assembly and customization.
-
Industrial Systems: In industrial settings, castellated PCBs are used for connecting modules, sensors, and control boards. The robust mechanical and electrical connections provided by castellation ensure reliable operation in demanding environments.
-
Automotive Electronics: Castellated PCBs are employed in automotive electronics, such as infotainment systems, driver assistance modules, and powertrain control units. The space-saving and high-reliability features of castellation make it suitable for automotive applications.
-
Medical Devices: Castellation is utilized in medical devices, including implantable electronics and diagnostic equipment. The compact size and reliable connectivity offered by castellated PCBs are crucial for medical applications where space is limited and performance is critical.
-
IoT and Wireless Modules: Castellated PCBs are extensively used in IoT (Internet of Things) and wireless modules. They enable the creation of compact and stackable designs, facilitating the integration of multiple functionalities in a single device.
FAQ
-
What is the difference between half-hole and surface-mount castellation?
Half-hole castellation involves drilling half-holes along the edges of the PCB, while surface-mount castellation creates rectangular or semicircular cuts without drilling through the board. Half-hole castellation is used for through-hole mounting, while surface-mount castellation is used for surface-mount soldering. -
Can castellated PCBs be used for high-density interconnects?
Yes, castellated PCBs can be used for high-density interconnects. The small size and precise spacing of the castellations allow for a large number of connections in a compact area. However, proper design considerations, such as castellation size, spacing, and pad design, must be taken into account to ensure reliable and error-free connections. -
Are there any limitations to the number of castellations on a PCB?
The number of castellations on a PCB is limited by factors such as the board size, castellation size, and spacing requirements. The designer must balance the number of castellations with the mechanical and electrical integrity of the board. Additionally, manufacturing capabilities and costs may also impose limitations on the number of castellations that can be practically implemented. -
How does castellation affect the cost of PCB manufacturing?
Incorporating castellation in PCB manufacturing can slightly increase the cost compared to standard PCBs without castellation. The additional processes involved, such as drilling, plating, and routing, contribute to the increased cost. However, the cost impact is often outweighed by the benefits of castellation, such as improved connectivity, space savings, and simplified assembly. -
Can castellated PCBs be used for high-frequency applications?
Yes, castellated PCBs can be used for high-frequency applications. However, special considerations must be taken into account to ensure signal integrity and minimize electromagnetic interference (EMI). Proper impedance matching, ground plane design, and shielding techniques should be employed to mitigate high-frequency effects. Additionally, the choice of materials, such as low-loss substrates and high-quality plating, is crucial for optimal high-frequency performance.
Conclusion
Castellation is a valuable feature in PCB design that offers numerous benefits, including improved connectivity, space savings, mechanical strength, and simplified assembly. By creating small cuts or holes along the edges of the PCB, castellation enables reliable and efficient interconnection between boards or components. The two main types of castellation, half-hole and surface-mount, cater to different mounting and soldering requirements.
When implementing castellation in PCB manufacturing, careful consideration must be given to factors such as castellation size, spacing, PCB thickness, component placement, solder mask and pad design, and manufacturing capabilities. By optimizing these aspects, designers can ensure the successful integration of castellation in their pcb projects.
Castellated PCBs find applications in various industries, including consumer electronics, industrial systems, automotive electronics, medical devices, and IoT and wireless modules. The compact size, reliable connectivity, and versatility offered by castellation make it a preferred choice for a wide range of electronic products.
As technology continues to advance and electronic devices become more complex and miniaturized, the importance of castellation in PCB design is likely to grow. By leveraging the benefits of castellation, designers can create innovative and efficient electronic solutions that meet the evolving demands of the market.