How are Flexible PCBs Made?
Flexible PCBs are made using a similar process to traditional rigid PCBs, but with a few key differences. Instead of using a rigid substrate material like FR-4, flexible PCBs use a flexible substrate material such as polyimide or polyester. The circuit is then printed onto the flexible substrate using a conductive ink or a thin layer of copper.
Materials Used in Flexible PCBs
Material | Description |
---|---|
Polyimide | A high-temperature resistant polymer that is commonly used as the base material for flexible PCBs. |
Polyester | A lower-cost alternative to polyimide that is suitable for less demanding applications. |
Copper | A thin layer of copper is often used as the conductive material in flexible PCBs. |
Adhesives | Various adhesives are used to bond the layers of a flexible PCB together. |
Manufacturing Process
-
Design: The first step in manufacturing a flexible PCB is to design the circuit using computer-aided design (CAD) software.
-
Printing: The circuit design is then printed onto the flexible substrate material using a screen printing process or a photolithography process.
-
Etching: If a copper layer is used, the unwanted copper is etched away using a chemical etching process.
-
Lamination: The layers of the flexible PCB are then laminated together using heat and pressure.
-
Cutting: The finished flexible PCB is then cut to the desired shape and size using a die-cutting process or a laser-cutting process.
Advantages of Flexible PCBs
Flexible PCBs offer several advantages over traditional rigid PCBs, including:
Space Savings
One of the main advantages of flexible PCBs is that they can be designed to fit into tight spaces where a rigid PCB would not be able to fit. This is especially important in applications where space is at a premium, such as in mobile devices or wearable technology.
Increased Reliability
Flexible PCBs are more resistant to vibration and shock than rigid PCBs, which can help to increase the reliability of the circuit. This is because the flexible substrate material is able to absorb some of the energy from impacts or vibrations, reducing the stress on the components.
Improved Thermal Management
Flexible PCBs can also help to improve thermal management in electronic devices. Because the flexible substrate material is thinner than a rigid substrate, it allows for better heat dissipation. This can help to prevent overheating and prolong the life of the components.
Cost Savings
In some cases, using a flexible PCB can help to reduce the overall cost of an electronic device. This is because flexible PCBs can often be designed to replace multiple rigid PCBs, reducing the number of components and the overall complexity of the device.
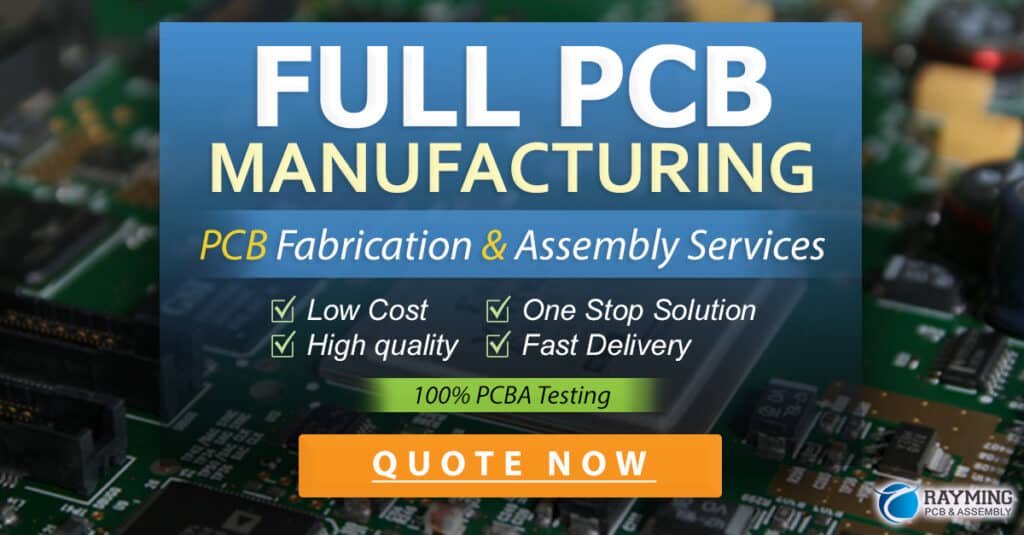
Applications of Flexible PCBs
Flexible PCBs are used in a wide range of applications, including:
Consumer Electronics
Flexible PCBs are commonly used in consumer electronics devices such as smartphones, tablets, and wearable technology. They allow for smaller, more compact designs and can help to improve the overall reliability of the device.
Medical Devices
Flexible PCBs are also used in medical devices such as hearing aids, pacemakers, and insulin pumps. They allow for smaller, more comfortable designs and can help to improve the reliability and longevity of the device.
Automotive Electronics
Flexible PCBs are increasingly being used in automotive electronics, such as in dashboard displays, sensors, and control modules. They offer improved reliability and can help to reduce the overall weight of the vehicle.
Aerospace and Defense
Flexible PCBs are also used in aerospace and defense applications, such as in satellites, aircraft, and military equipment. They offer improved reliability and can help to reduce the overall weight and size of the equipment.
Types of Flexible PCBs
There are several different types of flexible PCBs, each with its own unique characteristics and applications.
Single-Sided Flexible PCBs
Single-sided flexible PCBs have conductive traces on only one side of the substrate material. They are the simplest and most cost-effective type of flexible PCB, but they are limited in terms of the complexity of the circuit that can be designed.
Double-Sided Flexible PCBs
Double-sided flexible PCBs have conductive traces on both sides of the substrate material. They offer more design flexibility than single-sided flexible PCBs, but they are also more complex and expensive to manufacture.
Multi-Layer Flexible PCBs
Multi-layer flexible PCBs have multiple layers of conductive traces separated by insulating layers. They offer the most design flexibility and can be used to create complex circuits with a high density of components. However, they are also the most complex and expensive type of flexible PCB to manufacture.
Rigid-Flex PCBs
Rigid-flex PCBs are a hybrid of rigid and flexible PCBs. They consist of one or more rigid PCBs that are connected by flexible PCBs. This allows for the benefits of both rigid and flexible PCBs to be combined in a single design.
Challenges of Flexible PCBs
While flexible PCBs offer many advantages over traditional rigid PCBs, they also come with their own set of challenges.
Designing for Flexibility
Designing a flexible PCB requires careful consideration of the mechanical stresses that the circuit will be subjected to. The designer must ensure that the circuit can withstand repeated bending and flexing without breaking or failing.
Material Selection
Selecting the right materials for a flexible PCB is critical to its performance and reliability. The substrate material must be able to withstand the mechanical stresses of flexing, while the conductive material must be able to maintain its conductivity over time.
Manufacturing Challenges
Manufacturing flexible PCBs can be more challenging than manufacturing rigid PCBs. The flexible substrate material can be more difficult to handle and process, and the circuit must be designed to accommodate the flexing of the substrate.
FAQ
What is the difference between a flexible PCB and a rigid PCB?
A flexible PCB is designed to be bendable and can conform to various shapes and sizes, while a rigid PCB is designed to be stiff and inflexible. Flexible PCBs are often used in applications where space is limited or where the circuit needs to be able to move or flex, while rigid PCBs are used in applications where a stable, rigid platform is required.
What are the advantages of using a flexible PCB?
The advantages of using a flexible PCB include space savings, increased reliability, improved thermal management, and potential cost savings. Flexible PCBs can be designed to fit into tight spaces, are more resistant to vibration and shock, and can help to improve heat dissipation in electronic devices.
What are some common applications of flexible PCBs?
Flexible PCBs are commonly used in consumer electronics, medical devices, automotive electronics, and aerospace and defense applications. They are often used in applications where space is limited or where the circuit needs to be able to move or flex.
What are the different types of flexible PCBs?
The different types of flexible PCBs include single-sided flexible PCBs, double-sided flexible PCBs, multi-layer flexible PCBs, and rigid-flex PCBs. Each type of flexible PCB has its own unique characteristics and applications.
What are some of the challenges of designing and manufacturing flexible PCBs?
Some of the challenges of designing and manufacturing flexible PCBs include designing for flexibility, selecting the right materials, and manufacturing challenges. Designing a flexible PCB requires careful consideration of the mechanical stresses that the circuit will be subjected to, and manufacturing flexible PCBs can be more challenging than manufacturing rigid PCBs due to the need to handle and process the flexible substrate material.
Conclusion
Flexible PCBs are an increasingly important technology in the world of electronics. They offer numerous advantages over traditional rigid PCBs, including space savings, increased reliability, improved thermal management, and potential cost savings. While they come with their own set of challenges, the benefits of flexible PCBs make them an attractive option for a wide range of applications.
As technology continues to advance and electronic devices become smaller and more complex, the demand for flexible PCBs is only likely to increase. By understanding the basics of flexible PCBs, including how they are made, their advantages and applications, and the challenges of designing and manufacturing them, engineers and designers can make informed decisions about when and where to use this versatile technology.