The Role of Battery PCBs in Electronic Devices
Battery PCBs play a crucial role in the functioning of electronic devices that rely on portable power sources. These PCBs serve as the interface between the battery and the device’s components, regulating the flow of electricity and ensuring that each component receives the appropriate voltage and current.
Some of the key functions of a battery PCB include:
-
Power distribution: The battery PCB distributes power from the battery to the various components of the device, such as the processor, display, sensors, and communication modules.
-
Voltage regulation: The PCB includes voltage regulation circuitry to ensure that the components receive a stable and appropriate voltage level, preventing damage from voltage fluctuations.
-
Battery management: Battery PCBs often incorporate battery management systems (BMS) that monitor the battery’s charge level, temperature, and health, ensuring safe and efficient operation.
-
Protection circuits: To prevent damage to the battery and the device, battery PCBs include protection circuits that guard against overcharging, over-discharging, short-circuiting, and other potential hazards.
Types of Battery PCBs
There are several types of battery PCBs, each designed to cater to specific device requirements and battery technologies. Some common types include:
Li-ion Battery PCBs
Lithium-ion (Li-ion) batteries are widely used in portable electronic devices due to their high energy density, low self-discharge, and long lifespan. Li-ion battery PCBs are designed to manage the charging and discharging of these batteries, ensuring safe and efficient operation.
Li-Polymer Battery PCBs
Lithium-polymer (Li-Po) batteries are a variant of Li-ion batteries that offer higher energy density and a slimmer profile. Li-Po battery PCBs are similar to Li-ion PCBs but may include additional features to accommodate the unique characteristics of Li-Po batteries.
NiMH and NiCd Battery PCBs
Nickel-metal hydride (NiMH) and nickel-cadmium (NiCd) batteries are older battery technologies that are still used in some applications. PCBs designed for these batteries include specific charging and protection circuits to ensure optimal performance and safety.
Alkaline Battery PCBs
Alkaline batteries are primary (non-rechargeable) cells commonly used in low-power devices such as remote controls and wireless keyboards. Alkaline battery PCBs are relatively simple, focusing on power distribution and protection against reverse polarity and short-circuiting.
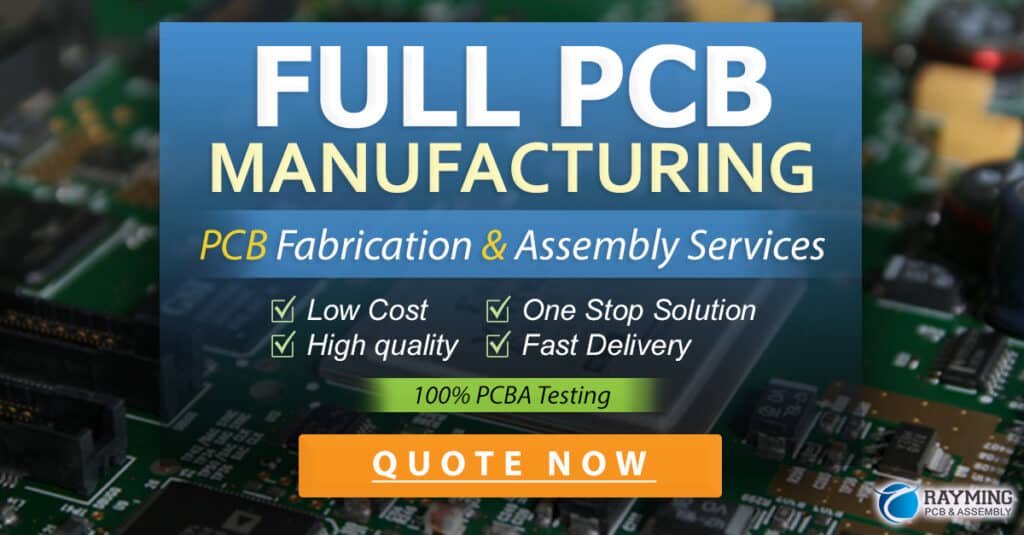
Battery PCB Design Considerations
Designing a battery PCB requires careful consideration of several factors to ensure optimal performance, safety, and reliability. Some key design considerations include:
-
Battery specifications: The PCB design must account for the battery’s voltage, capacity, and discharge characteristics to ensure compatibility and optimal performance.
-
Device requirements: The PCB must be designed to meet the power requirements of the device’s components, including voltage levels, current draw, and power sequencing.
-
Protection features: The PCB should incorporate appropriate protection circuits to safeguard against overcharging, over-discharging, short-circuiting, and other potential hazards.
-
Size and form factor: Battery PCBs must be designed to fit within the device’s enclosure while accommodating the battery and other components.
-
Thermal management: As batteries and electronic components generate heat during operation, the PCB design should consider thermal management techniques, such as heat sinks and ventilation, to prevent overheating.
-
Regulatory compliance: Battery PCBs must comply with relevant safety and environmental regulations, such as UL, CE, and RoHS standards.
Battery PCB Manufacturing Process
The manufacturing process for battery PCBs involves several steps to ensure high quality and reliability. These steps include:
-
PCB design and layout: The PCB design is created using electronic design automation (EDA) software, taking into account the various design considerations mentioned earlier.
-
Prototyping: A prototype of the PCB is manufactured and tested to validate the design and ensure proper functionality.
-
PCB fabrication: The PCB is manufactured using a multi-step process that includes printing the circuit pattern, etching, drilling, plating, and applying a protective coating.
-
Component assembly: The electronic components, including the battery management system, protection circuits, and connectors, are soldered onto the PCB using surface mount technology (SMT) or through-hole mounting.
-
Testing and quality control: The assembled PCB undergoes rigorous testing to ensure proper functionality, safety, and reliability. This may include electrical testing, environmental testing, and burn-in testing.
-
Packaging and shipping: The completed battery PCBs are packaged and shipped to the device manufacturer for integration into the final product.
Frequently Asked Questions (FAQ)
-
What is the difference between a battery PCB and a regular PCB?
A battery PCB is specifically designed to manage and control the flow of electricity from a battery to a device’s components. It includes additional features such as battery management systems, protection circuits, and voltage regulation, which are not typically found on regular PCBs. -
Can a battery PCB be replaced if it fails?
In most cases, a faulty battery PCB can be replaced by a skilled technician. However, the replacement process may vary depending on the device and the level of integration between the PCB and the battery. -
What safety features are included in battery PCBs?
Battery PCBs typically include protection circuits that guard against overcharging, over-discharging, short-circuiting, and other potential hazards. These features ensure the safe operation of the battery and prevent damage to the device and the user. -
How do battery PCBs handle different voltage requirements?
Battery PCBs include voltage regulation circuitry that ensures each component receives the appropriate voltage level. This may involve step-up or step-down converters, depending on the battery voltage and the requirements of the device’s components. -
Are battery PCBs designed differently for different battery technologies?
Yes, battery PCBs are designed to cater to the specific characteristics and requirements of different battery technologies, such as Li-ion, Li-Po, NiMH, and NiCd. The PCB design must account for factors such as voltage, capacity, and charging/discharging behavior of the specific battery type.
Conclusion
Battery PCBs are critical components in modern electronic devices, enabling the safe and efficient use of portable power sources. By understanding the functions, types, design considerations, and manufacturing processes of battery PCBs, engineers and manufacturers can create more reliable and high-performing devices that meet the ever-growing demands of consumers.
As battery technologies continue to evolve and new applications emerge, the role of battery PCBs will only become more important. By staying up-to-date with the latest advancements in battery PCB design and manufacturing, the electronics industry can continue to push the boundaries of what is possible with portable power sources.