Overview of the PCB Assembly Process
The PCB assembly process can be broadly divided into three main phases:
- PCB fabrication
- PCB assembly
- Testing and inspection
Each of these phases consists of several sub-steps that contribute to the overall success of the assembly process. Let’s take a closer look at each phase and its associated steps.
Phase 1: PCB Fabrication
Before the actual assembly process can begin, the PCB must be fabricated. This phase involves creating the bare PCB board that will serve as the foundation for the electronic components. The PCB fabrication process typically involves the following steps:
Step 1: PCB Design and Layout
The first step in PCB fabrication is designing the circuit and creating the PCB layout. This is typically done using specialized PCB design software, such as Altium Designer, Eagle, or KiCad. The design process involves:
- Schematic capture: Creating a digital representation of the electronic circuit
- Component placement: Arranging the electronic components on the PCB layout
- Routing: Connecting the components using copper traces
- Design rule checks (DRC): Verifying that the PCB layout adheres to manufacturing constraints and design guidelines
Step 2: PCB Manufacturing
Once the PCB design is finalized, the bare PCB board is manufactured. This process involves several sub-steps:
- Film generation: The PCB layout is used to create photographic films or digital files for each layer of the PCB.
- Copper lamination: Thin layers of copper foil are laminated onto the insulating substrate material, such as FR-4.
- Photoresist application: A light-sensitive polymer, called photoresist, is applied to the copper layers.
- Exposure and development: The photoresist is exposed to UV light through the photographic films or digital masks, and then developed to remove the unexposed areas.
- Etching: The exposed copper is etched away using a chemical solution, leaving behind the desired copper traces and pads.
- Drill holes: Holes are drilled through the PCB to accommodate through-hole components and vias.
- Solder mask application: A protective layer, called solder mask, is applied to the PCB to insulate the copper traces and prevent solder bridging.
- Silkscreen printing: Text, logos, and component identifiers are printed onto the PCB using a silkscreen process.
- Surface finish application: A surface finish, such as HASL, ENIG, or OSP, is applied to the exposed copper to prevent oxidation and enhance solderability.
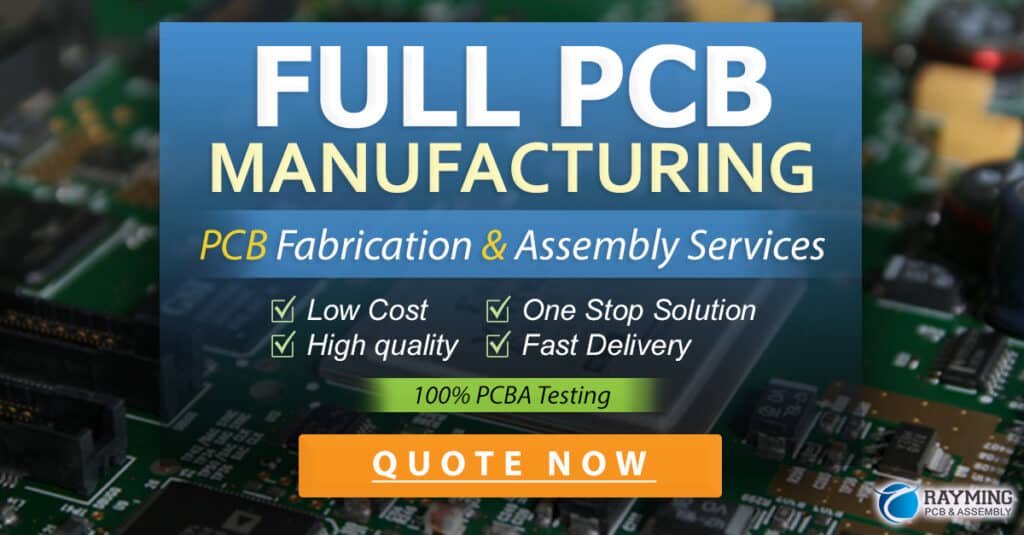
Phase 2: PCB Assembly
With the bare PCB board fabricated, the assembly process can begin. This phase involves populating the PCB with electronic components and soldering them in place. The PCB assembly process can be divided into two main categories: through-hole assembly (THA) and surface mount assembly (SMA).
Through-Hole Assembly (THA)
Through-hole assembly involves inserting component leads through holes drilled in the PCB and soldering them to pads on the opposite side. The process typically includes the following steps:
- Component placement: Through-hole components are inserted into the corresponding holes on the PCB, either manually or using automated insertion machines.
- Wave soldering: The populated PCB is passed over a molten solder wave, which solders the component leads to the PCB pads on the bottom side.
Surface Mount Assembly (SMA)
Surface mount assembly involves placing components directly onto pads on the surface of the PCB and soldering them in place. This process is more common in modern PCB assembly due to the smaller size of surface mount components and the increased density of PCB designs. SMA typically involves the following steps:
- Solder paste application: A thin layer of solder paste, consisting of tiny solder balls suspended in a flux matrix, is applied to the PCB pads using a stencil or screen printing process.
- Component placement: Surface mount components are placed onto the solder paste-coated pads using high-speed pick-and-place machines.
- Reflow soldering: The populated PCB is passed through a reflow oven, which heats the board in a controlled manner, melting the solder paste and creating a permanent bond between the components and the PCB pads.
Mixed Assembly
In some cases, a PCB may require both through-hole and surface mount components. In this mixed assembly process, the surface mount components are typically placed and soldered first, followed by the through-hole components.
Phase 3: Testing and Inspection
After the PCB assembly process is complete, the board undergoes various tests and inspections to ensure its quality, reliability, and functionality. This phase may include the following steps:
Step 1: Visual Inspection
A visual inspection is performed to check for any obvious defects, such as misaligned components, solder bridges, or missing components. This can be done manually by trained operators or using automated optical inspection (AOI) systems.
Step 2: Automated Optical Inspection (AOI)
AOI systems use high-resolution cameras and advanced image processing algorithms to detect assembly defects, such as component misalignment, incorrect polarity, or solder issues. AOI is a fast and efficient way to identify potential problems early in the assembly process.
Step 3: X-Ray Inspection
For PCBs with hidden solder joints, such as those found in ball grid array (BGA) components, X-ray inspection may be necessary. X-ray systems allow operators to view the internal structure of the solder joints and identify any voids, cracks, or other defects.
Step 4: In-Circuit Testing (ICT)
In-circuit testing involves using a bed-of-nails fixture to make electrical contact with specific points on the PCB. This allows the system to test the functionality of individual components and verify that they are correctly connected to the circuit.
Step 5: Functional Testing
Functional testing involves powering up the assembled PCB and verifying that it performs as intended. This may include running specific test routines, measuring key parameters, and ensuring that the board meets the required specifications.
Best Practices for PCB Assembly
To ensure a successful PCB assembly process, consider the following best practices:
- Design for manufacturability (DFM): Collaborate with your PCB fabrication and assembly partners early in the design process to ensure that your PCB layout is optimized for manufacturing.
- Use standard components: Whenever possible, use standard, readily available components to minimize lead times and reduce the risk of obsolescence.
- Maintain proper documentation: Keep accurate and up-to-date documentation, including bill of materials (BOM), assembly drawings, and test specifications, to avoid confusion and ensure smooth communication between all parties involved.
- Implement quality control measures: Establish a robust quality control system that includes regular inspections, testing, and continuous improvement initiatives to identify and address any issues in the assembly process.
- Partner with experienced suppliers: Work with reputable PCB fabrication and assembly partners who have a proven track record of delivering high-quality results and can provide valuable guidance throughout the process.
Frequently Asked Questions (FAQ)
1. What is the difference between through-hole and surface mount assembly?
Through-hole assembly involves inserting component leads through holes drilled in the PCB and soldering them to pads on the opposite side. Surface mount assembly, on the other hand, involves placing components directly onto pads on the surface of the PCB and soldering them in place. Surface mount assembly is more common in modern PCB designs due to the smaller size of components and increased board density.
2. What is solder paste, and how is it applied during PCB assembly?
Solder paste is a mixture of tiny solder balls suspended in a flux matrix. It is applied to the PCB pads during surface mount assembly using a stencil or screen printing process. The solder paste holds the components in place during the reflow soldering process, which melts the solder and creates a permanent bond between the components and the PCB pads.
3. Why is testing and inspection important in the PCB assembly process?
Testing and inspection are critical steps in the PCB assembly process, as they help ensure the quality, reliability, and functionality of the final product. Various methods, such as visual inspection, automated optical inspection, X-ray inspection, in-circuit testing, and functional testing, are used to identify any defects or issues that may affect the performance of the assembled PCB.
4. What is design for manufacturability (DFM), and why is it important?
Design for manufacturability (DFM) is the practice of designing a PCB layout that is optimized for the manufacturing process. This involves collaborating with PCB fabrication and assembly partners early in the design process to ensure that the PCB can be efficiently and reliably manufactured. DFM helps minimize the risk of production delays, quality issues, and cost overruns.
5. How can I ensure a successful PCB assembly process?
To ensure a successful PCB assembly process, consider the following best practices:
- Implement design for manufacturability (DFM) principles
- Use standard, readily available components
- Maintain accurate and up-to-date documentation
- Implement robust quality control measures
- Partner with experienced PCB fabrication and assembly suppliers
By following these best practices and working closely with your PCB assembly partners, you can minimize the risk of issues and ensure a smooth, efficient, and successful PCB assembly process.
Conclusion
The PCB assembly process is a complex and multi-faceted endeavor that requires careful planning, attention to detail, and close collaboration between all parties involved. By understanding the various steps involved in PCB fabrication, assembly, and testing, you can make informed decisions and implement best practices to ensure the success of your PCB projects.
Remember to prioritize design for manufacturability, use standard components, maintain proper documentation, implement quality control measures, and partner with experienced suppliers. By doing so, you can streamline your PCB assembly process, minimize the risk of issues, and deliver high-quality, reliable electronic products to your customers.
Phase | Steps |
---|---|
PCB Fabrication | 1. PCB Design and Layout 2. PCB Manufacturing |
PCB Assembly | 1. Through-Hole Assembly (THA) 2. Surface Mount Assembly (SMA) 3. Mixed Assembly |
Testing and Inspection | 1. Visual Inspection 2. Automated Optical Inspection (AOI) 3. X-Ray Inspection 4. In-Circuit Testing (ICT) 5. Functional Testing |
By mastering the PCB assembly process and staying up-to-date with the latest technologies and best practices, you can position yourself as a leader in the electronics manufacturing industry and deliver innovative, high-quality products that meet the evolving needs of your customers.