Introduction
In the rapidly evolving world of electronics, Printed Circuit Boards (PCBs) are the backbone of nearly every device, from smartphones and laptops to industrial machinery and automotive systems. As electronic devices become more compact, powerful, and complex, managing heat dissipation within PCBs has become a critical challenge. Effective thermal management in PCB design is essential to ensure the reliability, performance, and longevity of electronic systems.
This article delves into the importance of thermal management in PCBs, explores the key factors influencing heat generation and dissipation, and provides a detailed overview of the strategies, techniques, and materials used to address thermal challenges in modern PCB design.
The Importance of Thermal Management in PCBs
1. Why Thermal Management Matters
Heat is an inevitable byproduct of electronic components operating at high speeds and power levels. Excessive heat can lead to a range of issues, including:
- Component Failure: High temperatures can degrade the performance of semiconductors, capacitors, and other components, leading to premature failure.
- Signal Integrity Issues: Thermal expansion and contraction can cause mechanical stress, leading to solder joint cracks and signal integrity problems.
- Reduced Lifespan: Prolonged exposure to high temperatures can shorten the lifespan of electronic devices.
- Safety Risks: In extreme cases, overheating can pose safety risks, such as fire hazards or thermal runaway in batteries.
Effective thermal management ensures that heat is efficiently dissipated, maintaining optimal operating temperatures and preventing these issues.
2. Trends Driving the Need for Better Thermal Management
- Miniaturization: As devices shrink in size, the power density on PCBs increases, making heat dissipation more challenging.
- High-Power Applications: Modern electronics, such as 5G devices, electric vehicles, and IoT sensors, demand higher power levels, generating more heat.
- Advanced Technologies: The integration of advanced technologies like AI, machine learning, and high-performance computing requires PCBs to handle higher thermal loads.
Key Factors Influencing Thermal Management in PCBs
1. Heat Generation in PCBs
Heat in PCBs is primarily generated by:
- Active Components: Processors, microcontrollers, and power transistors are major heat sources.
- Passive Components: Resistors and inductors can also generate heat, especially in high-current applications.
- Trace Resistance: The resistance of copper traces can lead to Joule heating, particularly in high-current circuits.
2. Thermal Conductivity of PCB Materials
The ability of a PCB to conduct heat depends on the thermal conductivity of its materials:
- Substrate Materials: FR-4, the most common PCB substrate, has relatively low thermal conductivity. High-performance materials like ceramic or metal-core PCBs offer better thermal management.
- Copper Layers: Copper is an excellent conductor of heat, and its thickness and distribution play a crucial role in heat dissipation.
3. PCB Layout and Design
The layout of components and traces significantly impacts thermal performance:
- Component Placement: High-power components should be strategically placed to minimize heat concentration.
- Thermal Vias: These are small holes filled with conductive material that transfer heat from one layer to another.
- Heat Sinks and Pads: These are used to dissipate heat from high-power components.
4. Environmental Factors
External conditions, such as ambient temperature and airflow, also affect thermal management:
- Enclosure Design: The design of the device enclosure can either aid or hinder heat dissipation.
- Cooling Systems: Fans, heat pipes, and liquid cooling systems are often used to enhance thermal performance.
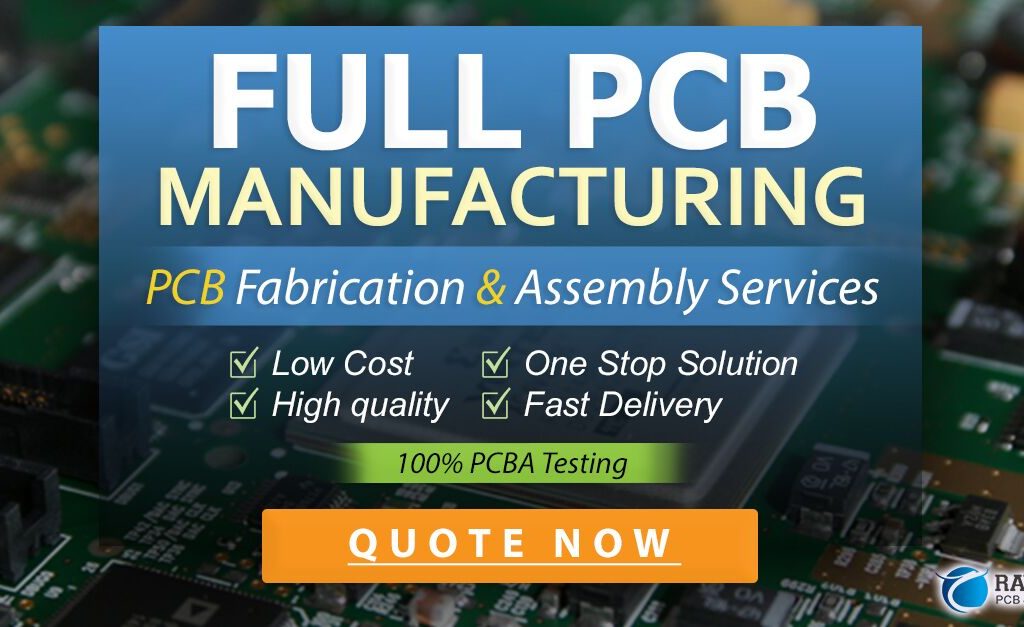
Strategies for Effective Thermal Management in PCBs
1. Material Selection
Choosing the right materials is the first step in effective thermal management:
- High-Thermal-Conductivity Substrates: Materials like aluminum, copper, and ceramic offer superior thermal performance compared to traditional FR-4.
- Thermal Interface Materials (TIMs): These materials, such as thermal pastes and pads, improve heat transfer between components and heat sinks.
2. Optimized PCB Layout
A well-designed PCB layout can significantly improve thermal performance:
- Component Placement: Place high-power components away from heat-sensitive parts and ensure adequate spacing for airflow.
- Thermal Relief Pads: These pads reduce thermal resistance between components and the PCB, improving heat dissipation.
- Copper Pouring: Adding copper pours to unused areas of the PCB can act as a heat spreader.
3. Thermal Vias
Thermal vias are essential for transferring heat between layers:
- Design Considerations: The size, number, and placement of thermal vias should be optimized based on the thermal load.
- Filled vs. Unfilled Vias: Filled vias offer better thermal conductivity but are more expensive.
4. Heat Sinks and Cooling Systems
Heat sinks and cooling systems are commonly used to manage high thermal loads:
- Heat Sinks: These are attached to high-power components to dissipate heat into the surrounding air.
- Fans and Blowers: Forced air cooling can significantly enhance heat dissipation.
- Liquid Cooling: In high-power applications, liquid cooling systems offer superior thermal performance.
5. Simulation and Analysis
Thermal simulation tools are invaluable for predicting and optimizing thermal performance:
- Finite Element Analysis (FEA): This technique models heat transfer within the PCB and identifies hotspots.
- Computational Fluid Dynamics (CFD): CFD simulations analyze airflow and cooling efficiency.
6. Advanced Techniques
Emerging technologies are pushing the boundaries of thermal management:
- Embedded Components: Integrating components within the PCB substrate can reduce thermal resistance.
- 3D Printing: Additive manufacturing enables the creation of complex, custom heat sinks and cooling structures.
- Phase Change Materials (PCMs): These materials absorb and release heat during phase transitions, providing passive thermal management.
Case Studies: Thermal Management in Real-World Applications
1. Consumer Electronics
In smartphones and laptops, thermal management is critical due to the high power density and compact form factor. Techniques like heat pipes, graphite sheets, and advanced TIMs are commonly used.
2. Automotive Electronics
Electric vehicles (EVs) require robust thermal management to handle the high power levels of batteries, motors, and power electronics. Liquid cooling and metal-core PCBs are often employed.
3. Industrial Electronics
Industrial machinery and robotics generate significant heat, necessitating the use of heat sinks, fans, and high-thermal-conductivity substrates.
4. Aerospace and Defense
In aerospace applications, thermal management is crucial due to extreme operating conditions. Ceramic PCBs and advanced cooling systems are commonly used.
Future Trends in PCB Thermal Management
1. Integration of AI and Machine Learning
AI-driven thermal simulation tools can optimize PCB designs in real-time, predicting thermal performance with unprecedented accuracy.
2. Development of New Materials
Researchers are exploring materials with even higher thermal conductivity, such as graphene and carbon nanotubes, for next-generation PCBs.
3. Enhanced Cooling Technologies
Innovations in cooling technologies, such as microchannel cooling and thermoelectric coolers, promise to revolutionize thermal management.
4. Sustainability
As the electronics industry moves toward sustainability, eco-friendly thermal management solutions, such as biodegradable TIMs, are gaining traction.
Conclusion
Thermal management in PCB design is a multifaceted challenge that requires a holistic approach, combining material science, design optimization, and advanced cooling technologies. As electronic devices continue to evolve, the importance of effective thermal management will only grow, driving innovation and shaping the future of PCB design.
By understanding the principles and strategies outlined in this article, engineers and designers can create PCBs that not only meet the demands of modern electronics but also ensure reliability, performance, and longevity in even the most demanding applications.
This article provides a comprehensive overview of thermal management in PCBs, covering key concepts, strategies, and future trends. If you need further details or specific examples, feel free to ask!