In the rapidly advancing field of electronics, multilayer printed circuit boards (PCBs) have become indispensable for designing complex and high-performance devices. Multilayer PCBs, which consist of three or more conductive layers separated by insulating material, offer significant advantages over single- or double-layer boards, including higher component density, improved signal integrity, and better thermal management. However, designing multilayer PCBs presents unique challenges that require careful planning, attention to detail, and adherence to best practices.
This article provides a comprehensive guide to the best multilayer PCB design guidelines and tips for circuit board layout. From layer stackup planning and signal integrity considerations to thermal management and manufacturability, these guidelines will help you create robust, reliable, and high-performance multilayer PCB designs.
Introduction to Multilayer PCBs
Multilayer PCBs are widely used in applications such as telecommunications, automotive electronics, medical devices, and consumer electronics. They enable designers to integrate more functionality into smaller form factors while maintaining high performance and reliability. However, the complexity of multilayer PCBs demands a systematic approach to design, ensuring that electrical, thermal, and mechanical requirements are met.
Key Advantages of Multilayer PCBs
- Higher Component Density: Multilayer PCBs allow for more components to be placed in a smaller area, making them ideal for compact devices.
- Improved Signal Integrity: Dedicated signal and ground layers reduce electromagnetic interference (EMI) and crosstalk.
- Better Thermal Management: Multiple layers provide additional pathways for heat dissipation.
- Enhanced Design Flexibility: Multilayer PCBs support complex routing and high-speed signal transmission.
- Reduced Weight and Size: By consolidating multiple functions into a single board, multilayer PCBs reduce the overall weight and size of electronic devices.
Best Multilayer PCB Design Guidelines
Designing a multilayer PCB requires a holistic approach that considers electrical performance, thermal management, manufacturability, and cost. Below are the best guidelines and tips for multilayer PCB design.
1. Layer Stackup Planning
The layer stackup is the foundation of a multilayer PCB design. It defines the arrangement of conductive and insulating layers and plays a critical role in determining the board’s electrical and mechanical performance.
a. Determine the Number of Layers
- Choose the number of layers based on the complexity of the circuit, signal integrity requirements, and thermal considerations.
- Common configurations include 4-layer, 6-layer, and 8-layer boards, but more layers may be required for high-density designs.
b. Assign Layer Functions
- Signal Layers: Dedicate specific layers for signal routing. High-speed signals should be routed on inner layers to minimize EMI.
- Ground and Power Planes: Use dedicated ground and power planes to provide low-impedance return paths and reduce noise.
- Split Planes: For multiple power domains, use split planes to isolate different voltage levels.
c. Symmetrical Stackup
- Arrange layers symmetrically to prevent warping and ensure mechanical stability. For example, a 6-layer stackup could be: Signal-Ground-Signal-Signal-Ground-Signal.
2. Signal Integrity Considerations
Signal integrity is critical for high-speed and high-frequency designs. Follow these guidelines to minimize signal degradation:
a. Controlled Impedance Routing
- Use controlled impedance routing for high-speed signals (e.g., USB, HDMI, DDR). Calculate trace width and spacing based on the dielectric constant and layer stackup.
- Maintain consistent trace widths and avoid abrupt changes in direction.
b. Minimize Crosstalk
- Separate high-speed signal traces from each other and from sensitive analog signals.
- Use ground planes between signal layers to reduce crosstalk.
c. Avoid Stubs
- Eliminate stubs in high-speed signal paths, as they can cause signal reflections and degrade performance.
d. Differential Pair Routing
- Route differential pairs (e.g., USB, Ethernet) with equal length and spacing to maintain signal integrity.
3. Power Integrity and Decoupling
Proper power distribution is essential for reliable operation. Follow these tips:
a. Power Plane Design
- Use solid power planes to provide low-impedance power distribution.
- Avoid splitting power planes unless necessary for multiple voltage domains.
b. Decoupling Capacitors
- Place decoupling capacitors close to power pins of ICs to suppress noise and stabilize voltage.
- Use a mix of bulk and ceramic capacitors for effective decoupling.
c. Via Placement
- Use multiple vias to connect power and ground planes, reducing inductance and improving current flow.
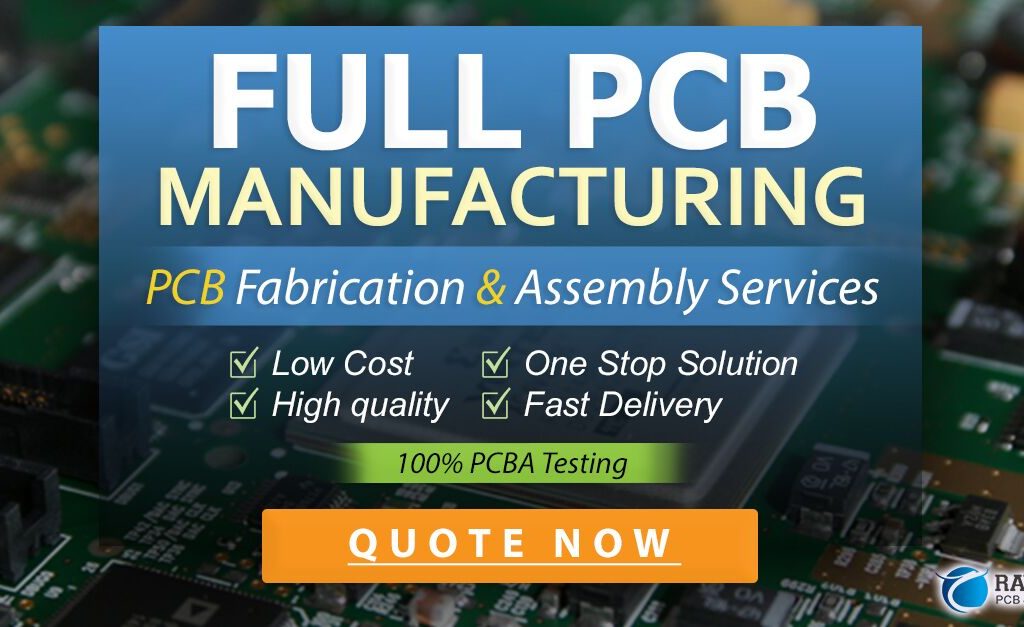
4. Thermal Management
Effective thermal management prevents overheating and ensures long-term reliability.
a. Thermal Vias
- Use thermal vias to transfer heat from components to inner or outer layers.
- Place thermal vias under high-power components, such as processors and power regulators.
b. Copper Pour
- Add copper pour on unused areas of signal layers to improve heat dissipation.
c. Component Placement
- Place heat-generating components away from sensitive devices and near the board edges for better airflow.
5. Component Placement and Routing
Proper component placement and routing are critical for manufacturability and performance.
a. Group Components by Function
- Place related components (e.g., analog, digital, power) in separate areas to minimize interference.
b. Minimize Trace Lengths
- Keep trace lengths as short as possible to reduce signal delay and losses.
c. Avoid Sharp Angles
- Use 45-degree angles or curves for trace routing to prevent signal reflections and manufacturing issues.
6. Design for Manufacturability (DFM)
Designing for manufacturability ensures that your PCB can be produced efficiently and reliably.
a. Follow Manufacturer Guidelines
- Adhere to the manufacturer’s design rules, including minimum trace width, spacing, and hole size.
b. Panelization
- Design the PCB in panels to facilitate handling during assembly. Include breakaway tabs or mouse bites for easy separation.
c. Test Points
- Add test points for in-circuit testing (ICT) and functional testing.
7. EMI/EMC Considerations
Electromagnetic interference (EMI) and electromagnetic compatibility (EMC) are critical for compliance and performance.
a. Shielding
- Use shielding cans or grounded copper pour to isolate sensitive circuits.
b. Grounding
- Ensure a solid ground connection for all components and layers.
c. Filtering
- Add filters to suppress noise on power and signal lines.
Common Mistakes to Avoid
When designing multilayer PCBs, avoid these common mistakes:
- Inadequate Layer Stackup Planning: Poor layer arrangement can lead to signal integrity issues and manufacturing challenges.
- Ignoring Thermal Management: Overheating can cause component failure and reduce the board’s lifespan.
- Neglecting DFM Guidelines: Failing to follow manufacturer guidelines can result in costly rework and delays.
- Overlooking EMI/EMC: Inadequate EMI/EMC measures can lead to compliance failures and performance issues.
Conclusion
Multilayer PCB design is a complex but rewarding process that enables the creation of high-performance, compact, and reliable electronic devices. By following the best guidelines and tips outlined in this article, you can overcome the challenges of multilayer PCB design and achieve optimal results.
Key considerations include proper layer stackup planning, signal and power integrity, thermal management, component placement, and design for manufacturability. Additionally, addressing EMI/EMC concerns and avoiding common mistakes will ensure that your multilayer PCB meets performance, reliability, and compliance requirements.
As technology continues to evolve, mastering the art of multilayer PCB design will remain an essential skill for engineers and designers. By adhering to these best practices, you can create innovative and high-quality multilayer PCB designs that push the boundaries of modern electronics.