The Printed Circuit Board (PCB) industry is a cornerstone of modern electronics, serving as the foundation for virtually every electronic device we use today. From smartphones and laptops to medical devices and automotive systems, PCBs are integral to the functionality and performance of these technologies. However, as the demand for more advanced, compact, and efficient electronic devices grows, the PCB industry faces a myriad of technological challenges. These challenges range from the need for higher density interconnects and improved thermal management to the adoption of new materials and the integration of advanced manufacturing techniques. This article delves into the key technological challenges in the PCB industry and explores the strategies and innovations that are helping to overcome them.
1. Miniaturization and Higher Density Interconnects
One of the most significant challenges in the PCB industry is the relentless push for miniaturization. As electronic devices become smaller and more powerful, the demand for PCBs with higher density interconnects (HDI) has surged. HDI PCBs are characterized by finer lines and spaces, smaller vias, and higher connection pad density. These features enable the placement of more components in a smaller area, which is essential for the development of compact and lightweight devices.
Challenges:
- Manufacturing Precision: Achieving the required precision for HDI PCBs is a significant challenge. The fabrication of fine lines and spaces, microvias, and high-density pads demands advanced manufacturing equipment and processes. Any deviation from the required specifications can lead to defects, such as short circuits, open circuits, or misaligned vias, which can compromise the performance and reliability of the PCB.
- Material Limitations: Traditional PCB materials may not be suitable for HDI applications due to their limitations in terms of thermal stability, dielectric properties, and mechanical strength. As a result, there is a need for new materials that can meet the stringent requirements of HDI PCBs.
- Cost Considerations: The production of HDI PCBs is more complex and time-consuming than traditional PCBs, leading to higher manufacturing costs. Balancing the need for high-density interconnects with cost-effectiveness is a significant challenge for PCB manufacturers.
Solutions:
- Advanced Manufacturing Techniques: The adoption of advanced manufacturing techniques, such as laser drilling, direct imaging, and automated optical inspection (AOI), has enabled the production of HDI PCBs with greater precision and accuracy. These technologies allow for the creation of finer features and the detection of defects at an early stage, reducing the risk of costly rework.
- New Materials: The development of new materials, such as high-performance laminates and low-loss dielectrics, has addressed some of the limitations of traditional PCB materials. These materials offer improved thermal stability, lower dielectric loss, and enhanced mechanical strength, making them suitable for HDI applications.
- Design Optimization: Optimizing the design of HDI PCBs can help reduce manufacturing complexity and costs. This includes the use of design for manufacturability (DFM) principles, which ensure that the PCB design is optimized for the manufacturing process, minimizing the risk of defects and reducing production time.
2. Thermal Management
As electronic devices become more powerful and compact, the issue of thermal management becomes increasingly critical. High-power components, such as processors and power amplifiers, generate significant amounts of heat, which can lead to thermal stress, component failure, and reduced reliability if not properly managed.
Challenges:
- Heat Dissipation: The compact nature of modern electronic devices limits the available space for heat dissipation. Traditional cooling methods, such as heat sinks and fans, may not be feasible in small form-factor devices, making it challenging to dissipate heat effectively.
- Thermal Expansion: Different materials in the PCB have different coefficients of thermal expansion (CTE). When exposed to temperature variations, these materials expand and contract at different rates, leading to thermal stress and potential failure of the PCB.
- High-Temperature Operation: Some applications, such as automotive and aerospace electronics, require PCBs to operate at high temperatures. Ensuring the reliability and performance of PCBs under these conditions is a significant challenge.
Solutions:
- Thermal Vias and Planes: The use of thermal vias and planes in the PCB design can help dissipate heat more effectively. Thermal vias are small holes filled with conductive material that transfer heat from the surface of the PCB to the inner layers or the opposite side of the board. Thermal planes, on the other hand, are large copper areas that spread heat across the PCB, reducing hot spots.
- Advanced Materials: The use of advanced materials with high thermal conductivity, such as metal-core PCBs and ceramic substrates, can improve heat dissipation. These materials provide a direct path for heat to escape from high-power components, reducing the risk of thermal stress and failure.
- Thermal Interface Materials (TIMs): TIMs are used to improve the thermal contact between components and heat sinks or other cooling solutions. These materials fill the microscopic gaps between surfaces, reducing thermal resistance and improving heat transfer.
- Simulation and Testing: Thermal simulation and testing are essential for identifying potential thermal issues early in the design process. By simulating the thermal behavior of the PCB under different operating conditions, designers can optimize the layout and materials to ensure effective heat dissipation.
3. Signal Integrity and High-Speed Design
With the increasing demand for high-speed data transmission in applications such as 5G, IoT, and high-performance computing, maintaining signal integrity has become a critical challenge in PCB design. Signal integrity refers to the quality of the electrical signals as they travel through the PCB, and it is affected by factors such as impedance matching, crosstalk, and signal attenuation.
Challenges:
- Impedance Matching: Ensuring proper impedance matching between the PCB traces and the connected components is essential for minimizing signal reflections and maintaining signal integrity. However, achieving the required impedance control can be challenging, especially in high-density designs with tight spacing.
- Crosstalk: Crosstalk occurs when signals from one trace interfere with adjacent traces, leading to signal distortion and data errors. As the density of PCB traces increases, the risk of crosstalk also increases, making it more difficult to maintain signal integrity.
- Signal Attenuation: High-frequency signals are more susceptible to attenuation, which is the loss of signal strength as it travels through the PCB. This can lead to reduced signal quality and data errors, particularly in long traces or high-speed designs.
Solutions:
- Controlled Impedance Design: Controlled impedance design involves carefully designing the PCB traces to achieve the required impedance for high-speed signals. This includes selecting the appropriate trace width, spacing, and dielectric material, as well as using impedance calculation tools to ensure accurate design.
- Differential Pair Routing: Differential pair routing is a technique used to minimize crosstalk and improve signal integrity in high-speed designs. By routing two traces carrying complementary signals in close proximity, the electromagnetic fields generated by each trace cancel each other out, reducing crosstalk and improving signal quality.
- Signal Integrity Simulation: Signal integrity simulation tools allow designers to analyze the behavior of high-speed signals in the PCB before fabrication. By simulating the effects of impedance, crosstalk, and attenuation, designers can identify potential issues and optimize the design to ensure reliable signal transmission.
- Advanced Materials: The use of advanced materials with low dielectric loss and consistent dielectric properties can help reduce signal attenuation and improve signal integrity. These materials are particularly important for high-frequency applications, where signal loss can be a significant issue.
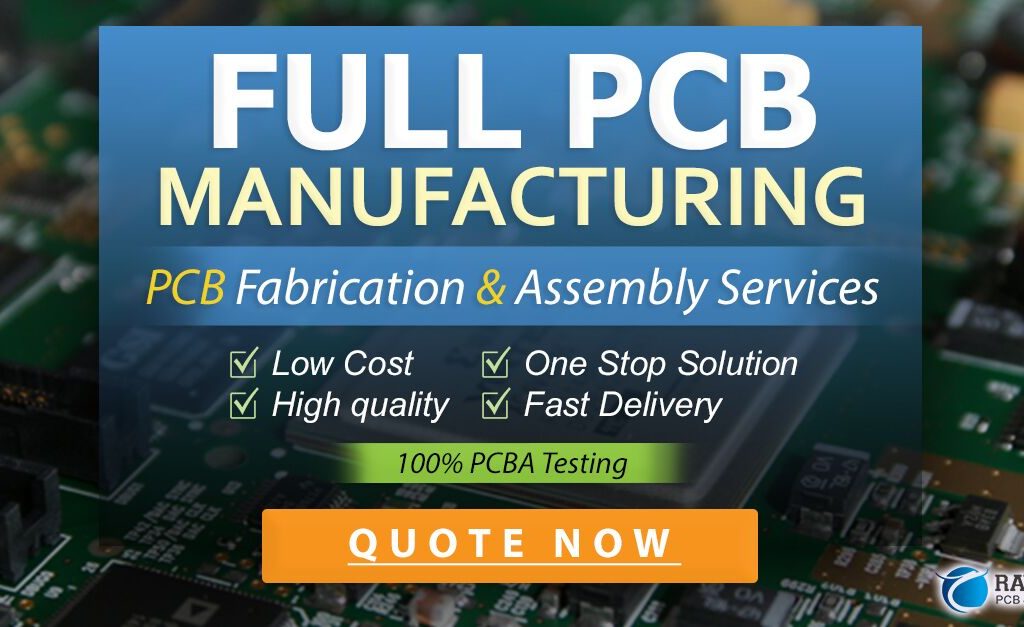
4. Environmental and Regulatory Compliance
The PCB industry is subject to a wide range of environmental regulations and standards, which aim to reduce the environmental impact of electronic products and ensure their safety and reliability. Compliance with these regulations is a significant challenge for PCB manufacturers, as it requires the adoption of new materials, processes, and technologies.
Challenges:
- Restriction of Hazardous Substances (RoHS): The RoHS directive restricts the use of certain hazardous substances, such as lead, mercury, and cadmium, in electronic products. Compliance with RoHS requires PCB manufacturers to use lead-free solders and other environmentally friendly materials, which can be more challenging to work with and may require changes to the manufacturing process.
- Waste Electrical and Electronic Equipment (WEEE): The WEEE directive requires the recycling and proper disposal of electronic waste. PCB manufacturers must design their products with end-of-life considerations in mind, such as using recyclable materials and minimizing the use of hazardous substances.
- Conflict Minerals: The use of conflict minerals, such as tin, tantalum, tungsten, and gold, in electronic products is a growing concern. PCB manufacturers must ensure that their supply chains are free from conflict minerals, which can be a complex and time-consuming process.
404: 02-10 13:55:26
Solutions:
- Lead-Free Soldering: The adoption of lead-free soldering processes has become standard in the PCB industry to comply with RoHS regulations. While lead-free solders have different properties than traditional lead-based solders, advancements in soldering technology and materials have made it possible to achieve reliable solder joints with lead-free alloys.
- Green Manufacturing: Green manufacturing practices, such as reducing waste, recycling materials, and using energy-efficient processes, can help PCB manufacturers comply with environmental regulations and reduce their environmental impact. This includes the use of water-based cleaning agents, the recycling of copper and other materials, and the adoption of energy-efficient equipment.
- Supply Chain Transparency: Ensuring transparency in the supply chain is essential for compliance with conflict mineral regulations. PCB manufacturers can work with suppliers to trace the origin of materials and ensure that they are sourced from conflict-free regions. This may involve the use of certification programs and third-party audits to verify the integrity of the supply chain.
5. Adoption of Advanced Manufacturing Technologies
The PCB industry is increasingly adopting advanced manufacturing technologies, such as additive manufacturing (3D printing), automation, and artificial intelligence (AI), to improve efficiency, reduce costs, and enhance product quality. However, the adoption of these technologies also presents challenges, particularly in terms of integration, scalability, and workforce training.
Challenges:
- Integration with Existing Processes: Integrating advanced manufacturing technologies with existing PCB manufacturing processes can be complex and costly. This may require significant changes to the production line, as well as the development of new workflows and quality control procedures.
- Scalability: While advanced manufacturing technologies offer significant benefits, scaling these technologies for high-volume production can be challenging. This is particularly true for additive manufacturing, which is currently more suited to prototyping and low-volume production.
- Workforce Training: The adoption of advanced manufacturing technologies requires a skilled workforce that is familiar with these technologies. However, there is a shortage of trained professionals in the PCB industry, making it difficult for manufacturers to fully leverage the potential of these technologies.
Solutions:
- Pilot Programs: Implementing pilot programs is a practical approach to integrating advanced manufacturing technologies into existing processes. By starting with small-scale projects, manufacturers can evaluate the feasibility and benefits of these technologies before scaling up.
- Collaboration with Technology Providers: Collaborating with technology providers can help PCB manufacturers overcome the challenges of integrating and scaling advanced manufacturing technologies. Technology providers can offer expertise, support, and customized solutions to meet the specific needs of PCB manufacturers.
- Workforce Development: Investing in workforce development is essential for the successful adoption of advanced manufacturing technologies. This includes providing training programs, certifications, and continuous learning opportunities to ensure that employees have the skills and knowledge needed to operate and maintain these technologies.
6. Cybersecurity and Intellectual Property Protection
As the PCB industry becomes more connected and reliant on digital technologies, cybersecurity and intellectual property (IP) protection have become critical concerns. The increasing use of IoT devices, cloud computing, and digital design tools has made PCBs more vulnerable to cyberattacks and IP theft.
Challenges:
- Cybersecurity Threats: The interconnected nature of modern manufacturing systems makes them vulnerable to cyberattacks, such as ransomware, data breaches, and intellectual property theft. A successful cyberattack can disrupt production, compromise sensitive data, and result in significant financial losses.
- IP Protection: Protecting intellectual property is a major concern for PCB manufacturers, particularly in a highly competitive market. Unauthorized access to design files, manufacturing processes, and proprietary technologies can lead to IP theft and loss of competitive advantage.
Solutions:
- Cybersecurity Measures: Implementing robust cybersecurity measures is essential for protecting manufacturing systems and sensitive data. This includes the use of firewalls, encryption, multi-factor authentication, and regular security audits to detect and prevent cyber threats.
- Secure Design and Manufacturing Processes: Ensuring the security of design and manufacturing processes is critical for protecting intellectual property. This includes the use of secure design tools, access controls, and digital rights management (DRM) to prevent unauthorized access to design files and manufacturing data.
- Employee Training: Educating employees about cybersecurity best practices is essential for preventing cyberattacks and protecting intellectual property. This includes training on recognizing phishing attempts, using secure passwords, and following company security policies.
Conclusion
The PCB industry is at the forefront of technological innovation, driving the development of advanced electronic devices that are transforming our world. However, this rapid pace of innovation also brings with it a host of technological challenges, from miniaturization and thermal management to signal integrity and environmental compliance. Overcoming these challenges requires a combination of advanced manufacturing techniques, new materials, design optimization, and a commitment to continuous improvement.
By embracing these solutions and staying ahead of emerging trends, the PCB industry can continue to push the boundaries of what is possible, delivering high-quality, reliable, and innovative products that meet the demands of today’s fast-paced technological landscape. As the industry evolves, collaboration between manufacturers, technology providers, and regulatory bodies will be essential for addressing these challenges and ensuring the continued growth and success of the PCB industry.