Introduction
In the ever-evolving world of electronics, the complexity of devices continues to grow, driven by the demand for more functionality, higher performance, and compact form factors. Multi-board PCB design has emerged as a critical solution to meet these demands, enabling the development of sophisticated systems that integrate multiple printed circuit boards (PCBs) into a single cohesive unit. This approach is widely used in applications ranging from consumer electronics and automotive systems to industrial machinery and aerospace technologies.
This article provides a comprehensive guide to multi-board PCB design, covering the fundamentals, benefits, design considerations, and best practices for creating high-performance multi-board systems.
What is Multi-Board PCB Design?
Definition
Multi-board PCB design involves the integration of multiple PCBs into a single system, where each board performs specific functions and communicates with other boards through connectors, cables, or wireless interfaces. This approach allows designers to modularize complex systems, making them easier to design, test, and maintain.
Key Components of Multi-Board Systems
- Main Board: Often referred to as the motherboard, this board serves as the central hub, connecting all other boards and managing communication between them.
- Daughter Boards: These are secondary boards that connect to the main board and perform specific functions, such as signal processing, power management, or sensor interfacing.
- Interconnects: These include connectors, cables, and backplanes that facilitate communication and power distribution between the boards.
- Enclosure: The physical housing that contains and protects the multi-board system, ensuring proper alignment, thermal management, and mechanical stability.
Benefits of Multi-Board PCB Design
1. Modularity
One of the primary benefits of multi-board PCB design is modularity. By breaking down a complex system into smaller, functional modules, designers can develop, test, and debug each module independently. This modular approach simplifies the design process and allows for easier upgrades and repairs.
2. Scalability
Multi-board systems are inherently scalable. Designers can add or remove daughter boards to adapt the system to different requirements or applications. This flexibility is particularly valuable in industries where customization and scalability are critical, such as automotive and industrial automation.
3. Improved Signal Integrity
By separating high-speed, high-power, and sensitive circuits onto different boards, multi-board design can improve signal integrity. This separation reduces electromagnetic interference (EMI) and crosstalk, leading to better overall performance.
4. Enhanced Thermal Management
Multi-board systems allow for more effective thermal management. Heat-generating components can be placed on separate boards, enabling better heat dissipation and reducing the risk of thermal-related failures. Additionally, the use of dedicated cooling solutions, such as heat sinks and fans, can be optimized for each board.
5. Cost Efficiency
While multi-board systems may have higher initial design and manufacturing costs, they can lead to cost savings in the long run. The modular nature of these systems allows for easier repairs and upgrades, reducing downtime and maintenance costs. Additionally, the ability to reuse daughter boards across different projects can lower development costs.
6. Design Flexibility
Multi-board design offers greater flexibility in terms of form factor and layout. Designers can arrange boards in various configurations to fit specific enclosures or mechanical constraints. This flexibility is particularly important in applications with limited space, such as portable devices and automotive systems.
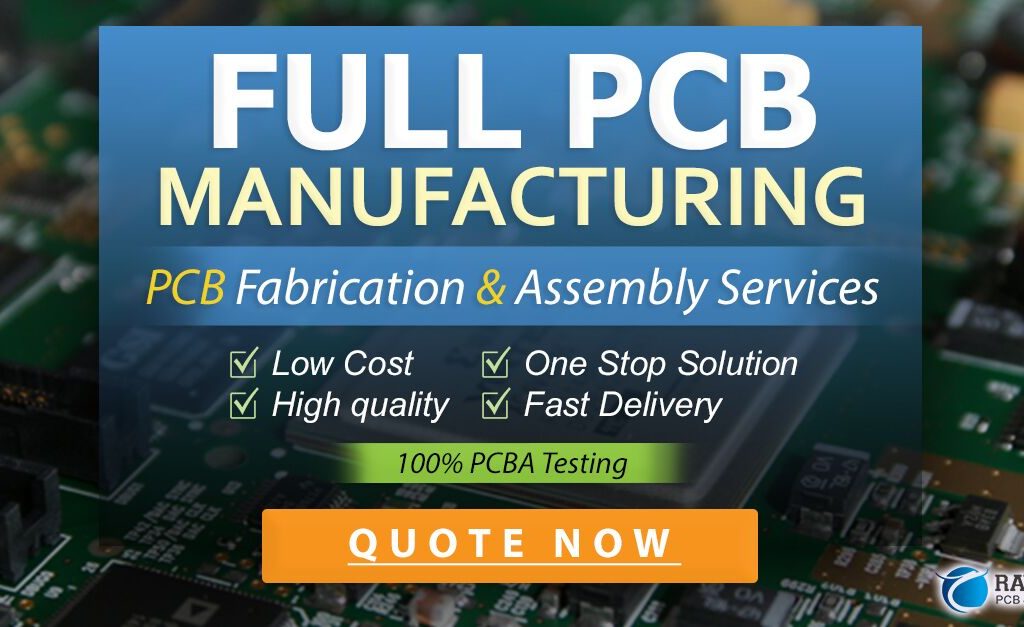
Multi-Board PCB Design Considerations
1. System Architecture
The first step in multi-board PCB design is defining the system architecture. This involves identifying the functional blocks, determining the number of boards required, and specifying the interconnections between them. Key considerations include:
- Functional Partitioning: Divide the system into logical modules based on functionality, such as power supply, signal processing, and communication.
- Communication Protocols: Choose appropriate communication protocols (e.g., SPI, I2C, UART, Ethernet) for inter-board communication.
- Power Distribution: Plan the power distribution network to ensure stable and efficient power delivery to all boards.
2. Interconnect Design
Interconnects are critical for the performance and reliability of multi-board systems. Key considerations for interconnect design include:
- Connector Selection: Choose connectors that meet the electrical, mechanical, and environmental requirements of the system. Consider factors such as pin count, pitch, current rating, and mating cycles.
- Cable Management: Design cables and harnesses to minimize signal loss, EMI, and mechanical stress. Use shielded cables for high-speed signals and ensure proper strain relief.
- Backplane Design: In systems with a backplane, ensure that the backplane provides reliable connections and supports the required signal integrity and power distribution.
3. Signal Integrity
Signal integrity is a critical consideration in multi-board PCB design, especially for high-speed and high-frequency signals. Key considerations include:
- Impedance Matching: Ensure that trace impedances are matched to prevent signal reflections and ensure clean signal transitions.
- Crosstalk: Minimize crosstalk by properly spacing signal traces and using ground planes as shields.
- EMI: Implement shielding and filtering techniques to reduce electromagnetic interference and ensure compliance with EMC standards.
4. Power Integrity
Power integrity is essential for ensuring stable and reliable power delivery to all boards in the system. Key considerations include:
- Power Distribution Network (PDN): Design a robust PDN with low impedance to ensure stable voltage levels and minimize noise.
- Decoupling Capacitors: Place decoupling capacitors near power pins to filter high-frequency noise and provide local energy storage.
- Voltage Drop: Ensure that trace widths and lengths are sufficient to minimize voltage drop and ensure adequate power delivery.
5. Thermal Management
Thermal management is critical for ensuring the reliability and performance of multi-board systems. Key considerations include:
- Heat Dissipation: Use thermal vias, heat sinks, and thermal pads to dissipate heat from high-power components.
- Material Selection: Choose materials with good thermal conductivity to improve heat dissipation.
- Component Placement: Place heat-generating components away from sensitive components and ensure adequate airflow.
6. Mechanical Design
The mechanical design of multi-board systems is crucial for ensuring proper alignment, stability, and durability. Key considerations include:
- Enclosure Design: Design the enclosure to provide proper alignment and secure mounting for all boards. Consider factors such as vibration, shock, and thermal expansion.
- Board Stacking: In systems with stacked boards, ensure that the stacking configuration provides adequate clearance and support. Use spacers and standoffs to maintain proper alignment.
- Mechanical Stress: Minimize mechanical stress on interconnects and components by ensuring proper strain relief and avoiding excessive bending or twisting.
7. Manufacturability
Designing for manufacturability is essential for ensuring that multi-board systems can be produced reliably and cost-effectively. Key considerations include:
- Design Rules: Follow the design rules and guidelines provided by the PCB manufacturer to ensure that the design can be manufactured.
- Tolerances: Account for manufacturing tolerances in the design, including trace widths, spacing, and connector alignment.
- Testing: Include test points and design for testability (DFT) to facilitate testing and debugging during manufacturing.
Best Practices for Multi-Board PCB Design
1. Collaborate with Manufacturers
Collaborate closely with PCB manufacturers and assembly partners early in the design process to ensure that the design meets their capabilities and requirements. This includes discussing layer stackup, connector selection, material selection, and design rules.
2. Use Advanced Design Tools
Use advanced PCB design tools that support multi-board design features, such as 3D modeling, signal integrity analysis, and thermal simulation. These tools can help optimize the design for performance, reliability, and manufacturability.
3. Optimize Interconnect Design
Optimize the design of interconnects to ensure reliable connections and minimize signal loss. Use simulation tools to analyze the impact of different interconnect configurations on signal integrity and power integrity.
4. Implement Proper Grounding
Implement proper grounding techniques, including the use of ground planes, ground vias, and star grounding, to minimize noise and ensure stable reference voltages.
5. Use Simulation and Analysis Tools
Use simulation and analysis tools to evaluate the design for signal integrity, power integrity, and thermal performance. This can help identify and address potential issues before manufacturing.
6. Follow Design for Manufacturability (DFM) Guidelines
Follow DFM guidelines to ensure that the design can be manufactured reliably and cost-effectively. This includes adhering to design rules, tolerances, and testing requirements.
7. Conduct Prototype Testing
Conduct prototype testing to validate the design and identify any issues that may not have been apparent during simulation and analysis. This includes electrical testing, thermal testing, and environmental testing.
8. Document the Design
Thoroughly document the design, including schematics, layout files, bill of materials (BOM), and assembly instructions. This documentation is essential for manufacturing, testing, and future revisions.
Conclusion
Multi-board PCB design is a complex and challenging process that requires a deep understanding of system architecture, interconnect design, signal integrity, power integrity, thermal management, and mechanical design. By following the principles and best practices outlined in this guide, designers can create high-performance multi-board systems that meet the demands of modern electronic devices. Whether you’re designing for consumer electronics, automotive systems, industrial machinery, or aerospace applications, the key to successful multi-board PCB design lies in careful planning, collaboration with manufacturers, and the use of advanced design tools and simulation techniques.
As technology continues to evolve, the importance of multi-board PCB design will only grow. By staying informed about the latest trends, materials, and design techniques, you can stay ahead of the curve and create innovative, reliable, and high-performance multi-board systems that push the boundaries of what’s possible in electronics design.