Introduction
Flex circuits, also known as flexible printed circuits (FPCs), are an essential component of modern electronics and enable compact, lightweight designs. As demand for smaller, more powerful devices continues to grow, the market for flex circuits is expanding rapidly. Major flex circuit manufacturers are investing heavily in R&D and advanced manufacturing capabilities to meet the needs of customers across industries. This article provides an overview of the key players among flex circuit manufacturers and their capabilities.
Top Flex Circuits Manufacturers
Nippon Mektron
- One of the largest flex circuit manufacturers globally
- Based in Japan and serves clients worldwide
- Wide range of FPC capabilities including rigid-flex
- Key end markets include automotive, industrial, and consumer electronics
Zhen Ding Technology
- Leading Chinese flex circuit manufacturer
- High-volume production of 2+ layer flex circuits
- Significant presence in consumer electronics and mobile devices
- Expanded production capacity over past decade
Flexium Interconnect
- Major flex circuit supplier headquartered in Taiwan
- Specializes in high-density interconnects (HDI)
- Supplies Apple and other mobile device makers
- Ramping up capacity for flex-rigid boards
Fujikura Ltd.
- Japanese firm, a big player in automotive flex circuits
- Produces ultra-thin polyimide FPCs
- Expertise in high-frequency and high-speed signaling applications
- Operates manufacturing facilities globally
MFS Technology
- Singapore-based manufacturer serving various industries
- Offers quick-turn prototyping and ramp-to-volume production
- Investing in Industry 4.0 automation and smart factory systems
- Acquired German flex circuit maker Heligear in 2021
Multek Technologies
- Owned by Chinese automotive giant BYD
- High-volume supplier to mobile device OEMs
- Capabilities in rigid-flex PCBs and flexible metal circuits
- Global footprint with sites in China and Americas
Manufacturing Capabilities of Leading Companies
The table below summarizes the key manufacturing capabilities of major flex circuit producers:
Company | Lines/Layers | Minimum Trace Width | Thickness Range | Rigid-Flex | Key Processes |
---|---|---|---|---|---|
Nippon Mektron | 12+ layers | 15 μm | 25-500 μm | Yes | Laser via forming, embedded components |
Zhen Ding Tech | 6+ layers | 10 μm | 25-250 μm | Limited | Flex-SMT assembly, inkjet printing |
Flexium | 10+ layers | 20 μm | 25-400 μm | Yes | Laser drilling, stacked vias |
Fujikura | 8+ layers | 15 μm | 25-125 μm | Yes | Ultra-thin polyimide flex |
MFS Technology | 8 layers | 25 μm | 25-250 μm | Yes | Quick-turn prototyping |
Multek | 6+ layers | 30 μm | 50-250 μm | Yes | Flex-on-flex bonding, EMI shielding |
As shown above, leading flex circuit manufacturers offer advanced capabilities in high layer count designs, fine line widths and spacing, and specialized processes like laser drilling and embedded passives. The ability to combine rigid and flexible materials in one PCB (rigid-flex) is also becoming ubiquitous.
Trends Driving Flex Circuit Demand and Innovation
Several trends are fueling growth and developments in the flex circuit market:
- Miniaturization – Flex circuits enable smaller, thinner devices as an alternative to rigid PCBs. The demand for compact, portable electronics continues to rise.
- Wearable technology – Flex circuits can withstand bending and flexing cycles, making them ideal for wearables like smart watches and fitness trackers.
- Automotive electronics – Vehicles are incorporating ever-greater electronics content, and flex circuits withstand vibration and temperature changes.
- Internet of Things (IoT) – Interconnected smart devices require small, lightweight flex circuits for sensors and communication.
- High speed signals – Flex circuits excel at high frequency applications needed for 5G networks and routers/servers.
- Rigid-flex – Combining rigid and flexible materials in one circuit opens new design possibilities and is a fast-growing segment.
These trends are pushing flex circuit manufacturers to advance their technologies. Key innovations include higher layer counts, thinner circuits, new base materials, laser processing, and embedding active and passive components.
Comparing Leading Flex Circuit Manufacturers
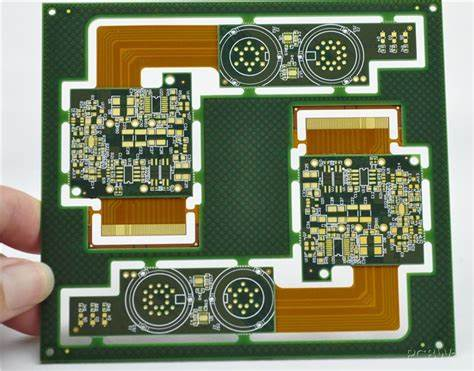
When selecting a flex circuit partner, there are several factors OEMs consider:
Volume Capabilities – The largest flex circuit makers like Nippon Mektron and Zhen Ding cater to high-volume customers, while smaller producers focus on prototyping and medium batches.
Quality & Reliability – Manufacturers must demonstrate consistent quality and reliability. Many have ISO 9001 certifications and conduct rigorous testing.
Design Capabilities – The ability to design and model complex flex circuits and provide engineering support is important.
Materials & Processes – Manufacturers differentiate based on materials (polyimide, LCP, etc.) and specialized processes like multilayer HDI flex.
Cost Structure – Pricing can vary greatly depending on order volumes, materials, tolerances, and other factors.
Logistics & Lead Times – Manufacturers able to deliver quick turns for prototypes and maintain short lead times have an advantage.
By examining these aspects, OEMs can find the ideal flex circuit partner to meet their specific requirements.
Frequently Asked Questions
Here are answers to some common questions about flex circuit manufacturers:
Q: What are some leading applications for flex circuits?
A: Key applications include consumer electronics, automotive, medical, industrial, and aerospace/defense. Flex circuits are used extensively in smartphones, tablets, wearables, vehicle electronics, medical devices, factory automation, avionics and more.
Q: Are flex circuits only made from polyimide materials?
A: No, other common base materials include polyester (PET), polyethylene naphthalate (PEN), and liquid crystal polymer (LCP). Manufacturers select the material based on requirements like flexibility, heat resistance, and dielectric properties.
Q: What are some differences between rigid PCBs and flex circuits?
A: Rigid PCBs provide superior mechanical support but are limited in terms of bending and shape. Flex circuits can bend dynamically and conform to space constraints. Flex circuits generally use thinner dielectric layers and finer traces than rigid boards.
Q: How are flex circuits and flexible printed electronics (FPE) different?
A: FPE refers to printing conductive inks/materials to create flexible circuits. This is an emerging technology but not yet widely used in commercial flex circuit fabrication which relies on copper etching.
Q: Are there environmental concerns around flex circuits?
A: Yes, some base materials like polyimide are difficult to recycle. Manufacturers are improving their environmental practices, for example, by reducing waste and using recyclable materials. Sustainability is an increasing priority for the industry.
Conclusion
As electronics OEMs continue innovating with smaller, smarter devices, they will rely on trusted flex circuit manufacturing partners. The leading manufacturers profiled here represent billions in capital investment and advanced R&D to expand the possibilities of flexible circuits. With trends like wearables and IoT just beginning to unfold, flex circuit makers are poised for strong growth by enabling the electronics of the future.