In-Circuit Testing and 6 Other PCB Testing Methods
As printed circuit boards (PCBs) become increasingly complex, with more intricate designs, higher component densities, and stricter performance requirements, effective testing is key to ensuring the quality and reliability of these critical systems. There are a variety of testing methods and techniques that can be utilized at the PCB level to validate proper design, fabrication, and assembly.
Types of PCB Testing
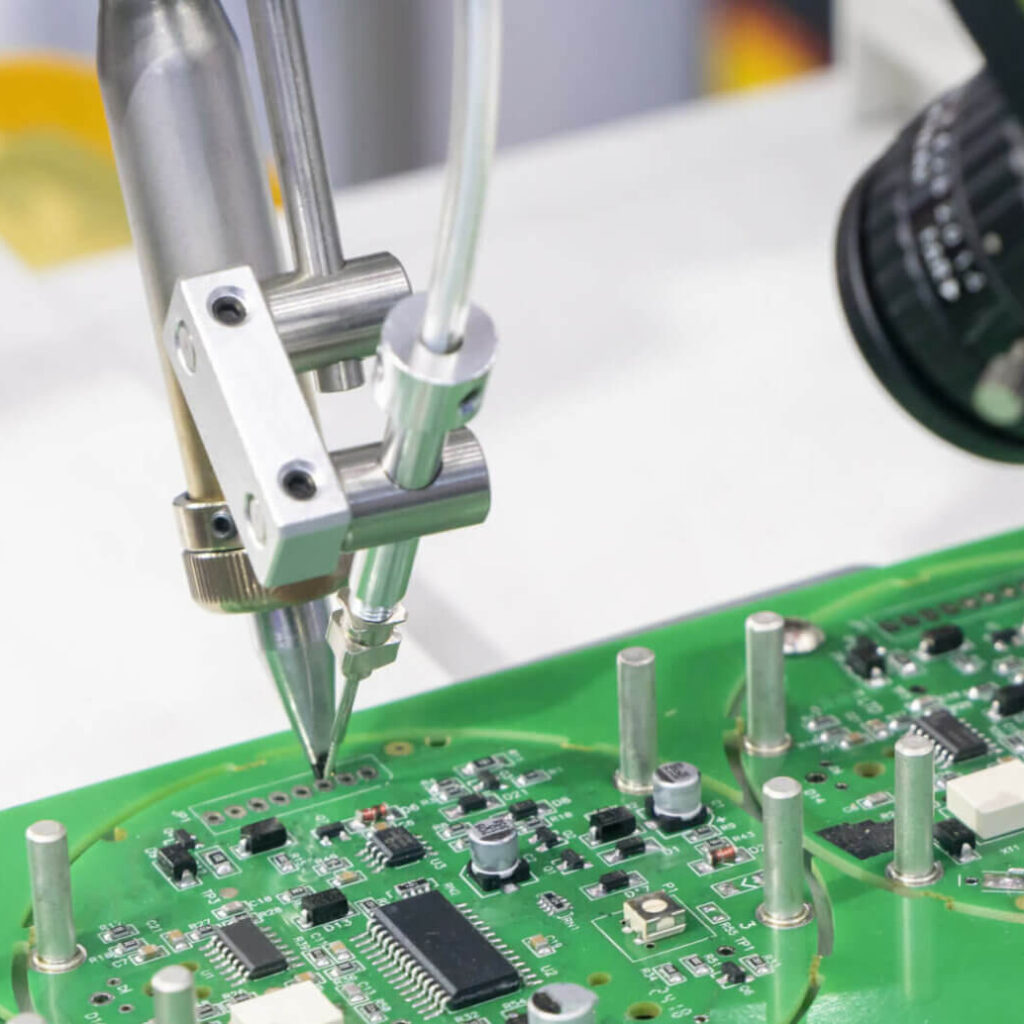
There are a number of testing methods that focus directly on verifying the PCB hardware itself. Some of the key types of PCB testing include:
Flying Probe Testing
Flying probe testing utilizes moveable test probes that can make contact at various test points across a PCB without requiring the use of a traditional fixture or bed-of-nails. It provides a fast, flexible testing approach well-suited for simple continuity checks and testing digital circuits.
In-Circuit Testing
In-circuit testing (ICT) verifies assembled boards by testing components in-situ as part of an active circuit. By incorporating system connections and components into the test, it can provide more complete testing coverage and detect certain types of assembly defects.
Boundary Scan Testing
Boundary scan testing leverages on-chip infrastructure to control and observe signal nodes when a device is mounted on assembled PCBs. It provides efficient testing access without physical test probes.
Automated Optical Inspection
Automated optical inspection (AOI) utilizes camera systems to visually inspect PCB assemblies and components. It serves as an efficient quality control check for material and workmanship issues.
X-Ray Inspection
X-ray imaging allows views inside a PCB or component, facilitating inspection of internal sub-assemblies as well as hidden solder and wire bonds that cannot be checked visually. It aids in detecting assembly-related flaws.
ICT Fixture Based Testing
Fixture based testing fixes a PCB in place electronically to facilitate efficient, repeated testing. Custom fixtures are designed to make contact with test points on a specific board. It enables thorough production testing.
Power Cycling
Power cycling applies repetitive power on-off stresses to boards in order to precipitate and detect latent defects. Such environmental stress screening provides accelerated life test data and can reveal reliability issues.
This article provides an in-depth examination of in-circuit testing along with brief overviews of these other common PCB test methods.
In-Circuit Testing
In-circuit test systems apply stimuli and take measurements at component terminals and test nodes across an assembled board while components remain electrically connected. This facilitates detailed testing of components in their operating state as part of active circuitry.
How In-Circuit Testing Works
In-circuit testing utilizes fixtures consisting of test probes, usually arranged in a bed-of-nails configuration, that make electrical contact at various test points across a PCB. Some key mechanisms enable reliable testing:
- Test fixtures provide secure physical clamping to gain stable electrical access
- Guarding techniques isolate measurements for accurate data capture
- Test programs apply vectors and capture measurement data
- Fixture simulation models ensure test coverage of circuits
To execute a test, boards are mounted into fixtures to engage test probes at target test points. The in-circuit test system then runs a pre-programmed test routine, applying signals in sponsored sequences while capturing measurements for comparison against expected values. Test results and diagnostics pinpoint faults.
Types of In-Circuit Test Systems
There are a few common architectures and implementations to deliver in-circuit testing:
Traditional In-Circuit Testers
Traditional ICT solutions utilize a centralized computer workstation controlling a switching matrix and instrumentation like digital sources and meters. The system cables out to separate fixtures housing probes and interfacing electronics.
Flying Probe Testers
Flying probe test systems incorporate test probes mounted on movable arms to contact points of interest across a board and perform connectivity checks or other simple functional tests without a fixture.
Fixtureless In-Circuit Testers
Emerging fixtureless ICT leverages multiple independently operated test pins arranged over a board to emulate fixture performance and deliver sophisticated in-circuit tests without separate fixtures.
Integrated Flying Probe Testers
Some systems combine traditional fixtures for access to hidden nodes with flying probes to extend access across the PCB, integrating in-circuit and flying probe technologies.
In-Circuit Testing Advantages
In-circuit test delivers some unique advantages, including:
- Tests components in operating state under actual loads
- Detects faults like improper connections or insertion errors
- Provides detailed fault isolation and diagnostics
- Covers hidden component pins and internal circuits
-Suits complex, high performance designs
By incorporating more complete functional paths and operating contexts – interactions from surrounding components, loads, noise sources, power supplies, etc. – ICT can stimulate and verify circuits to find defects that simpler methods may miss.
In-Circuit Test System Hardware
In-circuit test solutions require specialized hardware to enable reliable PCB access and accurate measurements while components operate in-circuit.
Test Fixtures
Test fixtures provide mechanical clamping paired with an array of test probes to establish electrical connections. They are custom designed for target PCB configurations to access designated test points across assemblies under test. Popular options include:
Bed-of-Nails Fixtures
Bed-of-nails fixtures incorporates an array of spring-loaded test pins that make contact and provide test access across the PCB surface. They facilitate cost-efficient testing for low to moderate complexity boards.
Loaded Board Fixtures
Loaded board fixtures integrate interfacing electronics right into the fixture to increase channel counts and enable guards for sensitive measurements. They suit more complex boards.
Vacuum Fixtures
Vacuum test fixtures combined mechanical clamping with a vacuum seal onto board surfaces to provide very secure, stable connections for in-circuit testing. They minimize intermittencies.
Custom Fixtures
For advanced packages and demanding test requirements, custom fixture designs can incorporate features like thermal controls, precise alignments, and built-in stimulation/response electronics to enable specialized ICT capabilities.
Test Probes
A variety of spring-loaded test probe designs allow fixtures to establish and maintain electrical contacts. Key probe styles include:
- Pogo Pins – Vertical travel pins for general purpose use
- Cobra Probes – Providing applied contact force during actuation
- Torsion probes – Allowing applied downforce without bending
- Litho probes – Offering ultra-fine pitch connection capabilities
Careful probe selection enhances connection integrity and helps minimize intermittencies during critical in-circuit testing.
Switching Matrix
The switching matrix routes signals from test instrumentation to target probe pins in the fixture under program control. Coaxial reed relays maintain signal fidelity up to microwave frequencies for high performance boards. Large matrices easily scale to fixtures with thousands of test probes.
Instrumentation
Programmable power supplies, digital sources and meters, function generators, electronic loads, and other instruments actually apply stimuli and capture response data during circuit measurements and function tests executed over the fixture??s access probes. Wide ranging sets of instruments support diverse PCB test needs.
In-Circuit Test Coverage
Effective in-circuit testing requires:
- Test point access for power, ground, and I/O signals
- Sufficient points to isolate faults
- Careful test program design to exercise circuits
Test coverage modeling helps assess these factors upfront and determine where additional test points may need to be designed into the product to facilitate required fault isolation levels. Virtual or actual test executions with failure injection can verify the test??s diagnostic resolution.
In-Circuit Test Program Development
Strategic test programming tailors in-circuit test vectors to reliably detect and diagnose faults without causing damage. Approaches include:
Sequential Testing
Applies input stimuli in series to monitor responses
Parallel Testing
Simultaneously applies multiple test vectors as allowed by configurations
Functional Testing
Exercises critical operating modes, applications, and sub-assemblies on the board
Analog Signature Testing
Uses specialized measurements to characterize sensitive analog circuit nodes
Self-Test Routine Testing
Runs on-board self-tests to fully exercise BIST circuitry
In-Circuit Testing Challenges
While delivering valuable testing coverage, in-circuit test does face some inherent challenges including:
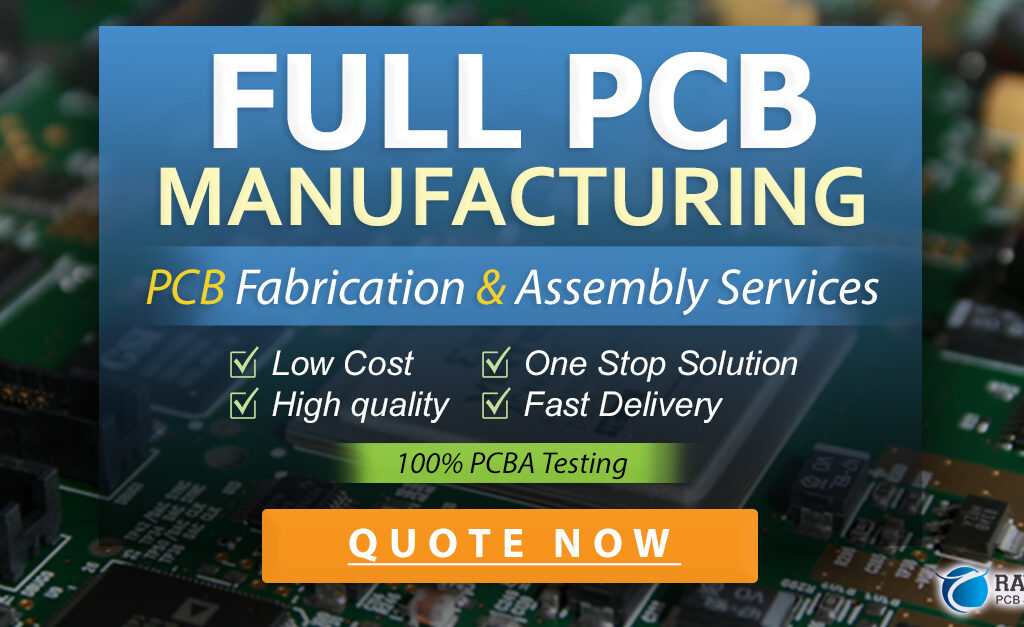
Access Limitations: Fixtures can only access exposed test points, preventing stimulation of purely internal nodes.
Measurement Interference: Surrounding components can induce noise or loading effects that undermine measurement integrity.
Timing Difficulties: Race conditions and propagation delays make testing timing-critical paths difficult.
Alignment Requirements: Tight alignments between small test points on boards and fixture probes demands careful fixturing.
Shorting Risks: In-circuit measurement risks accidentally shorting nodes, requiring very controlled probe placements.
Despite these issues, purposeful test designs can successfully overcome these challenges to implement high coverage, high quality in-circuit testing.
When to Apply In-Circuit Test
Here are common situations where in-circuit testing delivers particular value:
New Product Introduction Testing
During initial design verification, ICT provides comprehensive stimulus coverage and fault diagnostics supporting accelerated debug and root cause analysis.
Manufacturing Defect Screening
For volume production testing, ICT screens out a wide range of assembly-related and workmanship defects other methods may miss.
Field Service Depot Repair
When diagnosing complex faults from returns, ICT provides component-level stimulation and response capture better pinpointing failure origins.
Design Characterization
In-circuit measurement capabilities support in-depth performance characterization and margin testing to proven design robustness.
Qualification Testing
ICT supplements environmental stress screening with intermediate power-on tests monitoring operation throughout life test exposures.
For each application, appropriate test fixtures, instrumentation, and program suites must be developed to deliver efficient and effective in-circuit testing.
Key Specifications
These parameters help define essential performance capabilities when evaluating in-circuit testing solutions:
| Key Parameter | Description |
|-|-|
| Number of Test Channels | The number of actively driven test probes supported, defining total pins accessible |
| Maximum Probes per Fixture | The test point capacity accommodated for individual fixtures, governing design scale |
| Switching Technology | Matrix architecture (relay, multiplexer) supporting test point routing flexibility |
| Signal Frequency Range | The stimulus spectral content delivered and measurement BW provided |
| Digital Channels | Quantity of independent power-protected digital instruments |
| Analog Channels | Quantity of isolated sensitive measurement instruments |
| Vector Depth | Number of test node states controlled for a given instrument set to enable complex sequences/patterns |
| Vector Rate | The speed at which test vectors can be applied, establishing test cycle times |
| Guarding Infrastructure | Guarding techniques available to enhance measurement integrity and avoid interference |
| Safety Protection | Over-voltage and over-current protections preventing board or instrument damage |
| Diagnostic Feedback | Information from tests about precise failure locations and probable root causes |
Table data covers typical ranges for key parameters differentiating in-circuit test system capabilities. The necessary technical performance, channel counts, and test features depend on particular products under test and program objectives.
Cost Considerations
In-circuit testing requires significant upfront and ongoing investments. The table below outlines representative cost factors associated with acquiring and operating in-circuit test solutions.
| Cost Factor | Typical Range |
|-|-|
| Test Equipment Capital | $50K to $500K+ |
| Fixture Design and Fabrication | $5K to $50K per design |
| Test Program Development | $20K to $100K+ per program |
| Maintenance Contracts | ~10% capital cost per year |
| Floor Space | 50 to 500+ sqft |
| Technician Labor | 0.5 to 2+ technicians per system |
Test equipment capital covers hardware ranging from benchtop ICT testers to automated solutions with handlers. Fixtures, probes, cabling and other accessories add more. Custom fixturing and sophisticated test program authoring add substantial costs. Significant technician labor enables programming updates, maintenance, and operation. These costs can multiply with product variety.
Overall equipment efficiency, test coverage, and fault diagnostics prove critical to justifying investments and containing overall test costs through defect screening, repair acceleration, and avoidance of rework.
In-Circuit Testing FAQs
Q: Can in-circuit testing be applied during board fabrication?
A: No. In-circuit testing requires powered assembled boards so that components can operate in their mounted configurations within energized surrounding circuitry. It analyzes interactions unavailable on bare boards.
Q: Does in-circuit testing catch manufacturing defects?
A: Yes. By stimulating circuits across component terminals, bad connections, missing parts, or incorrect placements readily manifest as operation faults detected during test. Its component-level visibility aids diagnosing assembly issues.
Q: Can standalone self-tests provide similar testing to in-circuit approaches?
A: No. While valuable, onboard self-tests exercise limited internal monitor points with narrow controllability. Only external in-circuit test systems can access thousands of nodes across assemblies. Complete stimulus and diagnostics requires direct access.
Q: What is a guard on in-circuit test measurements?
A: Guarding refers to a shield driven at the same potential as a weak node being measured to prevent external noise or loading from distorting readings. Guards improve measurement integrity to meet accuracy requirements.
Q: Does in-circuit testing require writing vectors and code?
A: Yes. Tailored vectors and test execution software are required to properly sequence stimuli, route nodes, coordinate instruments, and evaluate captured data. Test programs are as critical as test hardware.