Introduction
Printed Circuit Boards (PCBs) are the backbone of modern electronics, and their design plays a critical role in the performance, reliability, and manufacturability of electronic devices. As circuits become more complex and operate at higher frequencies, the need for multi-layer PCBs has grown significantly. A 4-layer PCB is one of the most popular choices for balancing cost, complexity, and performance. This article provides a comprehensive guide on how to design and fabricate the best 4-layer PCB stackup using Altium Designer, one of the leading PCB design tools in the industry. We will cover stackup configuration, material selection, design rules, signal integrity considerations, and fabrication tips.
Why Choose a 4-Layer PCB?
Advantages of 4-Layer PCBs
- Improved Signal Integrity:
- Dedicated power and ground planes reduce noise and crosstalk.
- Better impedance control for high-speed signals.
- Enhanced Power Distribution:
- Low-impedance power delivery reduces voltage drops and improves stability.
- Compact Design:
- Multiple layers allow for denser component placement and routing.
- Cost-Effective:
- More affordable than higher-layer count PCBs while offering significant performance benefits.
Applications of 4-Layer PCBs
- Consumer electronics (smartphones, tablets, IoT devices).
- Industrial control systems.
- Automotive electronics.
- Medical devices.
- Communication systems.
Understanding PCB Stackup
What is a PCB Stackup?
A PCB stackup refers to the arrangement of copper and insulating layers in a multi-layer PCB. A well-designed stackup ensures proper signal integrity, power distribution, and thermal management.
Typical 4-Layer PCB Stackup
A standard 4-layer PCB stackup consists of the following layers:
- Top Layer (Signal Layer):
- Used for component placement and signal routing.
- Contains high-speed signals and critical traces.
- Inner Layer 1 (Ground Plane):
- Provides a low-impedance return path for signals.
- Reduces electromagnetic interference (EMI).
- Inner Layer 2 (Power Plane):
- Distributes power to components.
- Minimizes voltage drops and noise.
- Bottom Layer (Signal Layer):
- Used for additional signal routing and component placement.
Designing the Best 4-Layer PCB Stackup with Altium Designer
Step 1: Define Design Requirements
Before starting the design, gather the following information:
- Board Size and Shape:
- Determine the dimensions and form factor of the PCB.
- Component Placement:
- Identify critical components and their placement requirements.
- Signal Types:
- Classify signals as high-speed, low-speed, analog, or digital.
- Power Requirements:
- Specify voltage levels and current requirements.
- Impedance Control:
- Define impedance requirements for high-speed signals (e.g., 50Ω for single-ended, 100Ω for differential pairs).
Step 2: Configure the Stackup in Altium Designer
- Open the Layer Stack Manager:
- In Altium Designer, go to Design > Layer Stack Manager.
- Add Layers:
- Add four layers: Top, Inner 1, Inner 2, and Bottom.
- Assign Layer Types:
- Set Inner 1 as a ground plane and Inner 2 as a power plane.
- Define Dielectric Materials:
- Choose appropriate dielectric materials (e.g., FR-4) and specify their thickness.
- Set Copper Weights:
- Define copper thickness for each layer (e.g., 1 oz/ft² for signal layers, 2 oz/ft² for power planes).
- Impedance Calculation:
- Use the built-in impedance calculator to ensure trace widths meet impedance requirements.
Step 3: Plan Signal Routing
- High-Speed Signals:
- Route high-speed signals on the top and bottom layers.
- Use microstrip or stripline configurations for controlled impedance.
- Power and Ground Connections:
- Use vias to connect components to the power and ground planes.
- Place decoupling capacitors close to power pins.
- Signal Integrity:
- Avoid crossing split planes to prevent signal return path discontinuities.
- Minimize trace lengths and use 45-degree angles for bends.
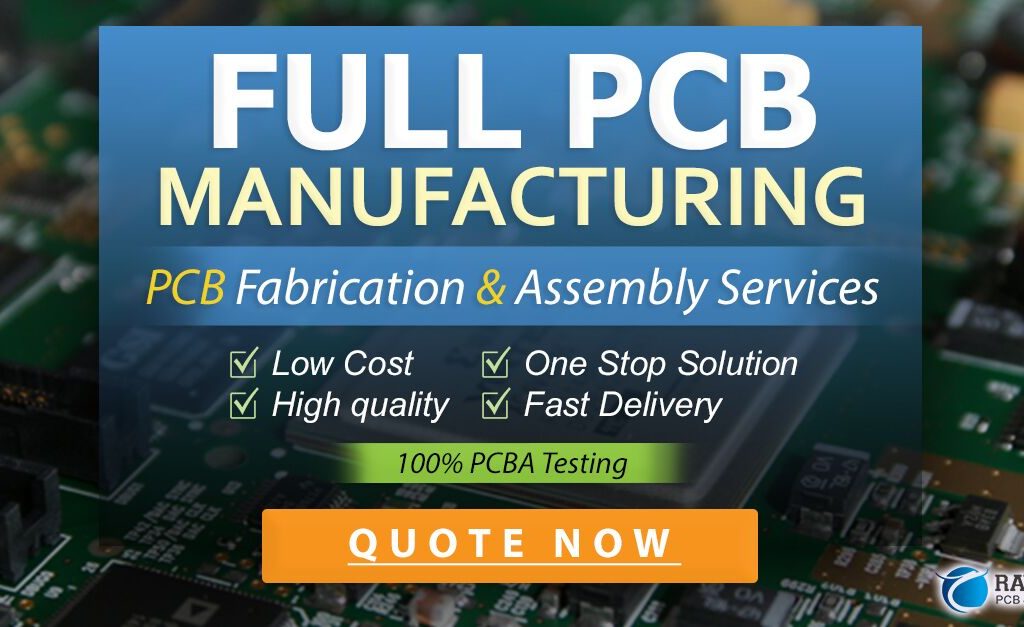
Step 4: Power Distribution Network (PDN) Design
- Power Plane Layout:
- Ensure the power plane covers all areas requiring power.
- Use multiple vias to reduce inductance and improve current flow.
- Decoupling Capacitors:
- Place decoupling capacitors near ICs to suppress noise.
- Use a mix of bulk and ceramic capacitors for different frequency ranges.
- Voltage Regulation:
- Include voltage regulators or DC-DC converters if multiple voltage levels are required.
Step 5: Thermal Management
- Thermal Vias:
- Use thermal vias under high-power components to dissipate heat to the ground plane.
- Copper Pour:
- Add copper pours on signal layers to improve heat dissipation.
- Component Placement:
- Space out heat-generating components to avoid hot spots.
Step 6: Design Rule Check (DRC)
- Set Design Rules:
- Define rules for trace width, clearance, via size, and more in Design > Rules.
- Run DRC:
- Perform a Design Rule Check to identify and resolve errors.
Step 7: Generate Manufacturing Files
- Gerber Files:
- Export Gerber files for each layer, including solder mask and silkscreen.
- Drill Files:
- Generate drill files for through-hole and via drilling.
- Bill of Materials (BOM):
- Create a BOM listing all components and their specifications.
- Assembly Drawings:
- Provide assembly drawings for component placement and orientation.
Fabrication Tips for 4-Layer PCBs
Material Selection
- Core Material:
- Use high-quality FR-4 for most applications.
- Consider high-frequency materials (e.g., Rogers) for RF circuits.
- Copper Thickness:
- Standard thickness is 1 oz/ft², but increase to 2 oz/ft² for high-current applications.
- Surface Finish:
- Choose HASL, ENIG, or OSP based on cost and performance requirements.
Impedance Control
- Work with the Fabricator:
- Provide impedance requirements and collaborate with the fabricator to achieve them.
- Test Coupons:
- Include test coupons on the PCB to verify impedance during fabrication.
Panelization
- Panel Design:
- Panelize the PCB to optimize manufacturing efficiency.
- Include breakaway tabs or V-grooves for easy separation.
- Fiducial Marks:
- Add fiducial marks for accurate assembly and alignment.
Testing and Validation
Electrical Testing
- Continuity Testing:
- Verify electrical connections and check for shorts or opens.
- Impedance Testing:
- Measure impedance of critical traces to ensure compliance with design requirements.
Functional Testing
- Power-Up Test:
- Apply power and verify voltage levels at key points.
- Signal Integrity Testing:
- Use oscilloscopes or network analyzers to test high-speed signals.
- Thermal Testing:
- Monitor temperature under load to ensure proper thermal management.
Conclusion
Designing and fabricating a high-quality 4-layer PCB stackup requires careful planning, attention to detail, and collaboration with fabrication partners. By leveraging the powerful tools in Altium Designer, you can create a stackup that meets your design requirements while ensuring signal integrity, power distribution, and thermal performance. Whether you’re working on consumer electronics, industrial systems, or automotive applications, the principles outlined in this guide will help you achieve the best possible results.
A well-designed 4-layer PCB not only enhances the performance and reliability of your electronic device but also reduces manufacturing costs and time-to-market. As technology continues to evolve, mastering the art of PCB stackup design will remain a critical skill for engineers and designers alike. With the knowledge and tools provided in this guide, you are well-equipped to tackle your next 4-layer PCB project with confidence.