Introduction
In the world of manufacturing and product development, the Bill of Materials (BOM) is a critical document that serves as the foundation for production, procurement, and assembly processes. Effective BOM management is essential for ensuring that products are built correctly, on time, and within budget. This article provides a comprehensive guide to BOM management, covering best practices, challenges, tools, and strategies to optimize the process. Whether you’re managing a simple product or a complex assembly, understanding and implementing robust BOM management practices can significantly enhance your operational efficiency and product quality.
Understanding the Bill of Materials (BOM)
What is a BOM?
A Bill of Materials (BOM) is a detailed list of all the components, materials, and subassemblies required to manufacture a product. It serves as a blueprint for production, guiding procurement, manufacturing, and assembly processes. The BOM includes information such as part numbers, descriptions, quantities, and sometimes even costs and suppliers.
Types of BOMs
- Engineering BOM (EBOM)
- Description: Created during the design phase, the EBOM includes all components and materials required to build the product as designed.
- Usage: Used by engineers and designers to ensure that the product can be manufactured as intended.
- Manufacturing BOM (MBOM)
- Description: Used during production, the MBOM includes additional details like assembly instructions, packaging, and process steps.
- Usage: Used by manufacturing teams to guide the production process.
- Service BOM (SBOM)
- Description: Used for maintenance and repair, the SBOM lists parts and assemblies needed for servicing the product.
- Usage: Used by service and maintenance teams to ensure that the product can be repaired and maintained effectively.
Key Components of a BOM
Part Number
A unique identifier for each component, ensuring that each part can be easily identified and tracked.
Description
A brief description of the component, including its function and specifications.
Quantity
The number of each component required to build the product.
Unit of Measure
The unit in which the quantity is measured (e.g., pieces, meters, kilograms).
Reference Designators
Identifiers that indicate where each component is located on the assembly (e.g., R1 for resistor 1, C1 for capacitor 1).
Supplier Information
Details about the suppliers of each component, including part numbers and contact information.
Cost
The cost of each component, which can be used to calculate the total cost of the product.
Best Practices for BOM Management
1. Standardize Part Numbering
A standardized part numbering system is crucial for ensuring that each component is uniquely identified and easily tracked.
- Consistency: Use a consistent format for all part numbers.
- Uniqueness: Ensure each part number is unique to avoid confusion.
- Scalability: Design the system to accommodate future growth and new components.
2. Maintain a Single Source of Truth
Ensuring that all stakeholders are working from the same BOM is critical to avoid discrepancies and errors.
- Centralized Repository: Use a centralized repository to store the BOM and ensure that all updates are reflected in real-time.
- Access Control: Implement strict access controls to prevent unauthorized changes and ensure that only approved versions are used.
3. Implement Version Control
Version control is essential for tracking changes and ensuring that the correct version of the BOM is used.
- Change Logs: Maintain a detailed change log that records all modifications, including the rationale behind each change.
- Approval Process: Implement an approval process for changes to the BOM to ensure that all modifications are reviewed and approved by relevant stakeholders.
4. Use BOM Management Software
BOM management software can automate and streamline the process, reducing the risk of errors and improving efficiency.
- Automation: Automates repetitive tasks, such as updating part numbers and quantities.
- Integration: Integrates with other tools like CAD, ERP, and PLM systems.
- Visibility: Provides real-time visibility into the BOM, making it easier to track changes and manage components.
5. Collaborate with Stakeholders
Effective BOM management requires collaboration between various stakeholders, including designers, procurement, and manufacturing teams.
- Communication: Establish clear communication channels to ensure that all stakeholders are informed of changes and updates.
- Collaboration Tools: Use collaborative tools and platforms that allow real-time updates and communication.
6. Regularly Review and Update the BOM
Regular reviews and updates of the BOM help maintain accuracy and relevance throughout the design and manufacturing process.
- Design Reviews: Include the BOM in regular design reviews to ensure that it is still accurate and up-to-date.
- Change Management: Implement a robust change management process to track updates to the BOM and communicate changes to all stakeholders.
7. Plan for Component Obsolescence
Component obsolescence can disrupt production and lead to costly redesigns.
- Lifecycle Management: Monitor the lifecycle of components and plan for replacements before they become obsolete.
- Alternative Sources: Identify alternative sources for components to mitigate the impact of obsolescence.
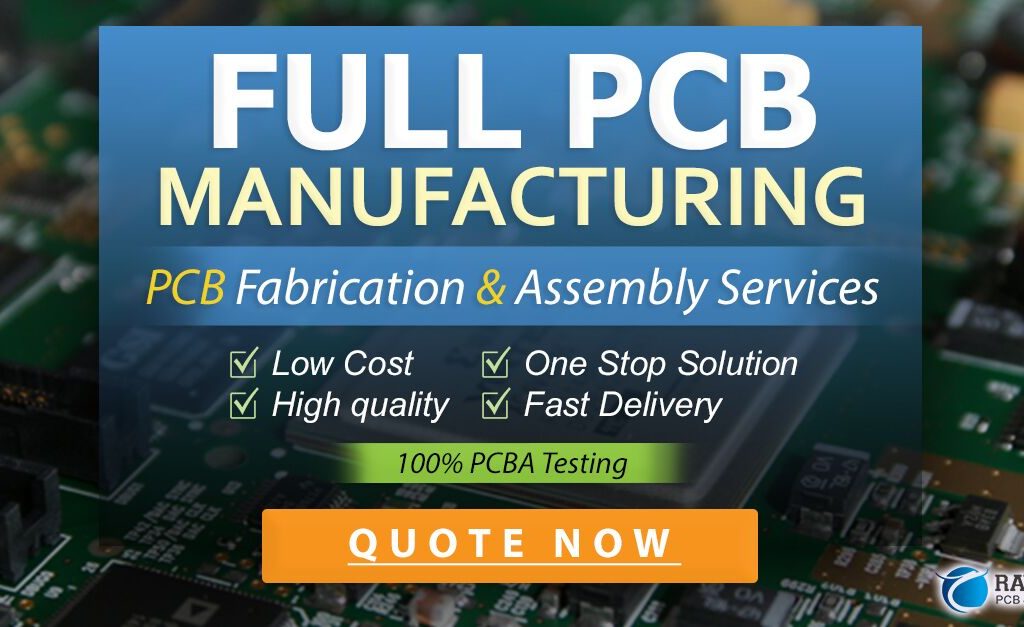
Challenges in BOM Management
1. Complexity and Volume
As products become more complex, the number of components in the BOM can grow exponentially, making management increasingly challenging.
- Solution: Use BOM management software to automate and streamline the process.
2. Component Availability
Component availability can fluctuate due to supply chain issues, obsolescence, or changes in demand.
- Solution: Maintain a flexible BOM and establish relationships with multiple suppliers.
3. Version Control
Keeping track of changes and ensuring that the correct version of the BOM is used is critical.
- Solution: Implement robust version control practices and use BOM management tools that support versioning.
4. Collaboration
BOM management often involves multiple stakeholders, including designers, procurement, and manufacturing teams.
- Solution: Use collaborative tools and platforms that allow real-time updates and communication.
BOM Management Tools and Software
Benefits of BOM Management Software
- Automation: Automates repetitive tasks, reducing the risk of errors.
- Integration: Integrates with other tools like CAD, ERP, and PLM systems.
- Visibility: Provides real-time visibility into the BOM, making it easier to track changes and manage components.
Popular BOM Management Tools
- Altium Designer
- Features: Integrated BOM management, real-time updates, and collaboration tools.
- Advantages: Seamless integration with PCB design tools, comprehensive features.
- Arena PLM
- Features: Cloud-based BOM management, version control, and collaboration.
- Advantages: Scalable, easy to use, and accessible from anywhere.
- Siemens Teamcenter
- Features: Comprehensive PLM and BOM management, integration with CAD and ERP systems.
- Advantages: Robust features, suitable for large enterprises.
Case Studies
Case Study 1: Streamlining BOM Management in a Consumer Electronics Company
A consumer electronics company faced challenges with managing the BOM for their complex PCB designs. By implementing Altium Designer and adopting a hierarchical BOM structure, they were able to streamline their BOM management process, reduce errors, and improve collaboration between design and manufacturing teams.
Case Study 2: Managing Variants in an Automotive Electronics Company
An automotive electronics company needed to manage multiple variants of their PCBs. By using Arena PLM and implementing a single BOM with conditional statements, they were able to efficiently manage variants, reduce the risk of errors, and improve time-to-market.
Case Study 3: Overcoming Component Availability Issues in an Industrial Equipment Manufacturer
An industrial equipment manufacturer faced frequent component availability issues. By maintaining a flexible BOM and establishing relationships with multiple suppliers, they were able to mitigate the impact of supply chain disruptions and ensure continuous production.
Conclusion
Effective BOM management is essential for ensuring that products are built correctly, on time, and within budget. By following best practices such as standardizing part numbering, maintaining a single source of truth, implementing version control, and using BOM management software, companies can significantly enhance their operational efficiency and product quality. Addressing challenges such as complexity, component availability, and collaboration through careful planning and the right tools ensures smooth production and assembly, ultimately leading to successful product launches. Whether it’s a simple product or a complex assembly, the key to effective BOM management lies in balancing flexibility, accuracy, and collaboration.