Introduction
Flexible printed circuits (FPCs), commonly referred to as flex circuits, have become increasingly popular in modern electronics due to their ability to bend, fold, and conform to unique shapes and spaces. Unlike traditional rigid PCBs, flex circuits offer unparalleled design flexibility, making them ideal for applications in consumer electronics, medical devices, automotive systems, and aerospace. However, designing flex circuits presents unique challenges that go beyond the drawing board. This article delves into the lessons learned in flex design, exploring best practices, common pitfalls, and real-world insights to help engineers navigate the complexities of flex circuit design.
Understanding Flex Circuits
What are Flex Circuits?
Flex circuits are made from flexible polymer substrates, such as polyimide, which allow the circuit to bend and flex without breaking. They can be single-sided, double-sided, or multilayer, and they often incorporate rigid sections (rigid-flex) for added structural support.
Advantages of Flex Circuits
- Space Savings: Flex circuits can be bent and folded to fit into tight spaces, reducing the overall size of the device.
- Weight Reduction: Flex circuits are lighter than traditional rigid PCBs, making them ideal for weight-sensitive applications.
- Durability: The ability to flex and bend makes these circuits more resistant to mechanical stress and vibration.
- Design Freedom: Flex circuits enable innovative designs that are not possible with rigid boards.
Key Considerations in Flex Design
1. Material Selection
Choosing the right materials is crucial for the performance and reliability of flex circuits.
- Substrate Material: Polyimide is the most common substrate material due to its excellent thermal stability, flexibility, and mechanical properties.
- Conductive Material: Copper is typically used for the conductive layers, but the thickness and type (rolled annealed vs. electro-deposited) can impact flexibility and durability.
- Adhesives: The choice of adhesive can affect the flexibility and thermal performance of the circuit. Acrylic and epoxy adhesives are commonly used.
2. Layer Stack-Up
The layer stack-up design is critical for ensuring the flexibility and reliability of the circuit.
- Single-Sided vs. Multilayer: Single-sided flex circuits are the simplest and most flexible, while multilayer designs offer higher density but reduced flexibility.
- Rigid-Flex Designs: Combining rigid and flexible sections can provide structural support while maintaining flexibility where needed.
- Balanced Construction: Ensure a symmetrical layer stack-up to prevent warping and improve mechanical stability.
3. Bend Radius
The bend radius is a key factor in determining the durability and longevity of a flex circuit.
- Minimum Bend Radius: The minimum bend radius should be carefully calculated based on the material thickness and flexibility. A general rule of thumb is to use a bend radius of at least 10 times the thickness of the flex circuit.
- Dynamic vs. Static Bending: Dynamic bending (repeated flexing) requires a larger bend radius compared to static bending (one-time or infrequent flexing).
4. Routing and Trace Design
Proper routing and trace design are essential for maintaining signal integrity and mechanical reliability.
- Trace Width and Spacing: Use appropriate trace widths and spacing to ensure electrical performance and manufacturability. Avoid sharp corners and use curved traces to reduce stress.
- Staggered Traces: In multilayer designs, stagger the traces to avoid creating a neutral bend axis, which can lead to cracking.
- Teardrops: Use teardrops at the junction of traces and pads to reduce stress and improve reliability.
5. Coverlay and Stiffeners
Coverlay and stiffeners provide additional protection and support for flex circuits.
- Coverlay: A flexible polymer layer (typically polyimide) that covers and protects the traces. It also provides electrical insulation.
- Stiffeners: Rigid materials (such as FR4 or polyimide) added to specific areas to provide mechanical support and facilitate component mounting.
6. Thermal Management
Thermal management is critical for ensuring the reliability of flex circuits, especially in high-power applications.
- Thermal Vias: Use thermal vias to dissipate heat from high-power components.
- Heat Spreaders: Incorporate heat spreaders or thermal pads to manage heat distribution.
- Material Selection: Choose materials with good thermal conductivity and stability.
Best Practices in Flex Design
1. Collaborate with Manufacturers Early
Engaging with your flex circuit manufacturer early in the design process can help identify potential issues and optimize the design for manufacturability.
- Design for Manufacturability (DFM): Work with the manufacturer to ensure the design meets their DFM guidelines.
- Prototyping: Build prototypes to test and validate the design before full-scale production.
- Feedback Loop: Establish a feedback loop with the manufacturer to address any issues and refine the design.
2. Simulate and Test
Simulation and testing are essential for validating the performance and reliability of flex circuits.
- FEA Analysis: Use finite element analysis (FEA) to simulate mechanical stress and bending.
- Signal Integrity Analysis: Perform signal integrity analysis to ensure electrical performance.
- Environmental Testing: Conduct environmental testing (thermal, vibration, humidity) to validate the design under real-world conditions.
3. Document and Communicate
Thorough documentation and clear communication are key to successful flex circuit design.
- Design Guidelines: Create and share design guidelines with the team to ensure consistency.
- Change Management: Implement a robust change management process to track and communicate design changes.
- Manufacturing Drawings: Provide detailed manufacturing drawings and instructions to the manufacturer.
4. Plan for Assembly and Integration
Consider the assembly and integration process when designing flex circuits.
- Component Placement: Place components strategically to minimize stress on the flex circuit during assembly and use.
- Connector Selection: Choose connectors that are compatible with the flex circuit and provide reliable connections.
- Handling and Installation: Provide guidelines for handling and installing the flex circuit to prevent damage.
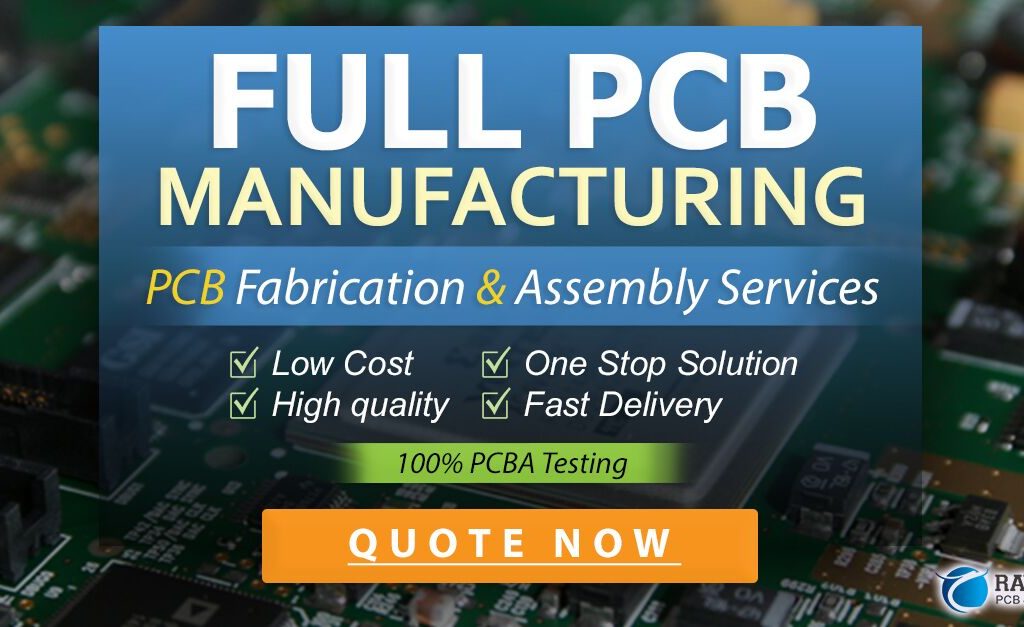
Common Pitfalls and Lessons Learned
1. Underestimating the Bend Radius
One of the most common mistakes in flex design is underestimating the bend radius, leading to mechanical failure.
- Lesson Learned: Always calculate and adhere to the minimum bend radius, considering both static and dynamic bending requirements.
2. Ignoring Material Properties
Ignoring the properties of materials can result in poor performance and reliability.
- Lesson Learned: Carefully select materials based on their thermal, mechanical, and electrical properties, and consider how they interact with each other.
3. Overlooking Thermal Management
Neglecting thermal management can lead to overheating and failure of the flex circuit.
- Lesson Learned: Incorporate thermal management strategies, such as thermal vias and heat spreaders, into the design from the outset.
4. Inadequate Testing
Skipping or inadequately performing testing can result in unforeseen issues during production or use.
- Lesson Learned: Conduct thorough simulation and testing, including environmental and mechanical stress tests, to validate the design.
5. Poor Communication with Manufacturers
Lack of communication with manufacturers can lead to misunderstandings and design issues.
- Lesson Learned: Establish clear and open communication channels with the manufacturer, and involve them early in the design process.
Case Studies
Case Study 1: Flex Circuit in Wearable Technology
A wearable technology company designed a flex circuit for a fitness tracker. Initially, they underestimated the bend radius, leading to mechanical failure during testing. By collaborating with their manufacturer and conducting FEA analysis, they optimized the bend radius and material selection, resulting in a durable and reliable flex circuit.
Case Study 2: Rigid-Flex Design in Medical Devices
A medical device manufacturer developed a rigid-flex circuit for a portable diagnostic device. They faced challenges with thermal management and signal integrity. Through iterative prototyping and testing, they incorporated thermal vias and optimized trace routing, achieving a high-performance design that met all regulatory requirements.
Case Study 3: Automotive Flex Circuit
An automotive company designed a flex circuit for a vehicle’s infotainment system. They initially overlooked the importance of material properties, leading to premature failure under high-temperature conditions. By selecting high-temperature polyimide and improving thermal management, they enhanced the reliability and longevity of the flex circuit.
Conclusion
Designing flex circuits requires a deep understanding of materials, mechanical properties, and manufacturing processes. By following best practices such as collaborating with manufacturers early, simulating and testing thoroughly, documenting and communicating effectively, and planning for assembly and integration, engineers can overcome the unique challenges of flex design. Learning from common pitfalls and real-world case studies further enhances the ability to create reliable and high-performance flex circuits. Ultimately, mastering flex design opens up new possibilities for innovation and enables the development of cutting-edge electronic devices that push the boundaries of traditional PCB design.