Introduction
Printed Circuit Board (PCB) reference designs are invaluable resources for engineers and designers, providing a foundation upon which to build custom solutions. These pre-designed circuits, often created by component manufacturers or experienced designers, offer proven solutions for common design challenges. By leveraging reference designs, engineers can accelerate development, reduce risk, and improve the overall quality of their PCB designs. However, effectively utilizing reference designs requires a strategic approach. This article explores the best practices for using PCB reference designs, ensuring that you maximize their benefits while avoiding common pitfalls.
Understanding PCB Reference Designs
What are PCB Reference Designs?
PCB reference designs are complete, tested circuit designs that serve as a starting point for developing custom PCBs. They typically include schematics, layout files, bill of materials (BOM), and sometimes firmware or software. These designs are often provided by semiconductor manufacturers, such as Texas Instruments, Analog Devices, and Microchip, to showcase their components in real-world applications.
Benefits of Using Reference Designs
- Accelerated Development: Reduces the time required to design and test new circuits.
- Proven Solutions: Leverages tested and validated designs, reducing the risk of errors.
- Cost Savings: Minimizes the need for extensive prototyping and testing.
- Learning Resource: Provides insights into best practices and advanced design techniques.
Best Practices for Using PCB Reference Designs
1. Choose the Right Reference Design
Selecting an appropriate reference design is crucial for ensuring that it meets your project requirements.
- Match Specifications: Ensure the reference design aligns with your performance, power, and size requirements.
- Component Availability: Verify that the components used in the reference design are readily available and suitable for your supply chain.
- Application Relevance: Choose a reference design that is relevant to your application, whether it’s for power management, signal processing, or communication.
2. Thoroughly Review the Documentation
Comprehensive documentation is key to understanding and effectively utilizing a reference design.
- Schematics: Carefully review the schematics to understand the circuit topology and component connections.
- Layout Files: Examine the PCB layout files to gain insights into placement, routing, and layer stack-up.
- BOM: Analyze the bill of materials to ensure all components are available and suitable for your design.
- Application Notes: Read any accompanying application notes or design guides for additional context and best practices.
3. Understand the Design Intent
Grasping the intent behind the reference design helps you adapt it to your specific needs.
- Functional Blocks: Identify the key functional blocks and their roles in the circuit.
- Performance Metrics: Understand the performance metrics and how they were achieved.
- Design Trade-offs: Recognize any trade-offs made in the design, such as cost vs. performance, and consider how they impact your project.
4. Validate the Reference Design
Before integrating a reference design into your project, it’s essential to validate its performance and suitability.
- Simulation: Use simulation tools to verify the circuit’s behavior under different conditions.
- Prototyping: Build a prototype to test the reference design in a real-world environment.
- Testing: Conduct thorough testing to ensure the design meets your performance and reliability requirements.
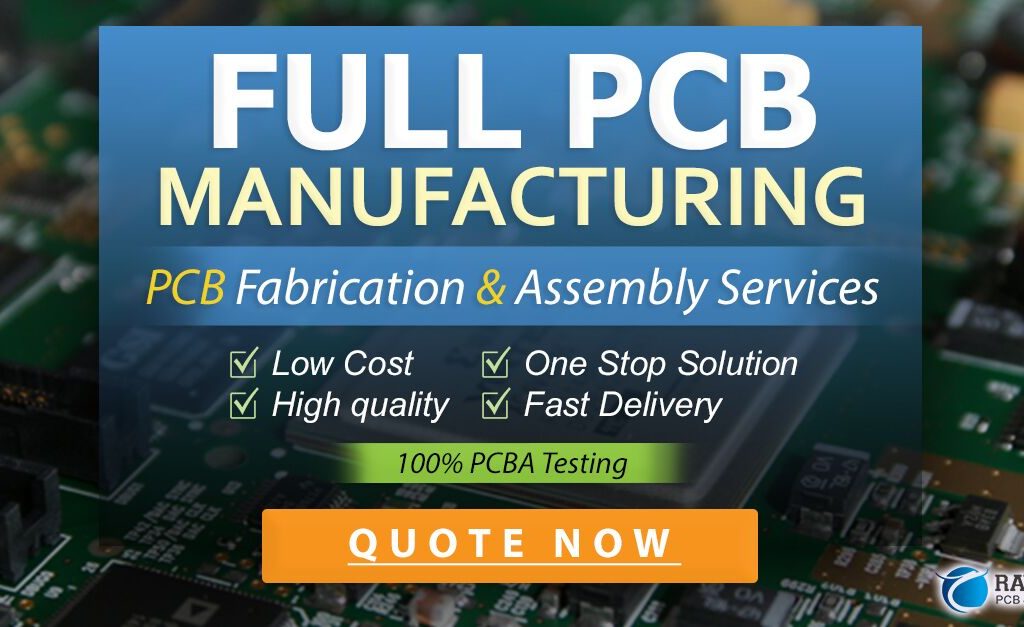
5. Customize for Your Application
While reference designs provide a solid foundation, customization is often necessary to meet specific project requirements.
- Component Substitution: Replace components with alternatives that better suit your design constraints, such as cost, availability, or performance.
- Circuit Modifications: Modify the circuit to add or remove features, adjust performance parameters, or integrate with other subsystems.
- Layout Adjustments: Adapt the PCB layout to fit your form factor, thermal management, and signal integrity requirements.
6. Ensure Compatibility with Your Design Environment
Integrating a reference design into your existing design environment requires careful consideration.
- Design Tools: Ensure compatibility with your PCB design tools, such as Altium, Eagle, or KiCad.
- File Formats: Convert reference design files to formats supported by your tools if necessary.
- Design Rules: Apply your design rules and constraints to the reference design to ensure consistency with your overall project.
7. Leverage Manufacturer Support
Many component manufacturers offer extensive support for their reference designs, which can be invaluable during the design process.
- Technical Support: Reach out to the manufacturer’s technical support team for assistance with the reference design.
- Community Forums: Participate in manufacturer forums and communities to seek advice and share experiences with other engineers.
- Training Resources: Utilize training resources, such as webinars, tutorials, and documentation, provided by the manufacturer.
8. Document Your Customizations
Thorough documentation of any customizations made to the reference design is essential for future reference and maintenance.
- Change Logs: Maintain a detailed change log that records all modifications, including the rationale behind each change.
- Updated Schematics: Update the schematics to reflect any changes made to the circuit.
- Revised BOM: Ensure the bill of materials is updated to include any new or substituted components.
9. Conduct Design Reviews
Regular design reviews help ensure that the reference design is being used effectively and that any customizations are appropriate.
- Peer Reviews: Involve peers in the review process to gain different perspectives and catch potential issues.
- Cross-Functional Reviews: Include team members from different disciplines, such as hardware, software, and mechanical engineering, to ensure a holistic review.
- Iterative Process: Treat design reviews as an iterative process, continuously refining the design based on feedback and testing results.
10. Plan for Future Updates
Reference designs may evolve over time, and planning for future updates can help keep your design current.
- Version Control: Implement version control for your design files to track changes and updates.
- Component Lifecycle: Monitor the lifecycle of components used in the reference design to anticipate obsolescence and plan for replacements.
- Manufacturer Updates: Stay informed about updates to the reference design from the manufacturer, such as new versions or improved components.
Common Challenges and Solutions
1. Component Obsolescence
Components used in reference designs may become obsolete, impacting the availability and longevity of your design.
- Solution: Regularly review the BOM and identify alternative components that can be used as replacements. Engage with the manufacturer for recommendations on equivalent parts.
2. Performance Variability
The performance of a reference design may vary when adapted to different applications or environments.
- Solution: Conduct thorough testing and validation to ensure the design meets your specific performance requirements. Use simulation tools to predict performance under different conditions.
3. Integration Issues
Integrating a reference design with other subsystems or existing designs can present challenges.
- Solution: Carefully plan the integration process, considering factors such as signal integrity, power distribution, and thermal management. Use design reviews to identify and address potential integration issues.
4. Intellectual Property Concerns
Using a reference design may raise intellectual property (IP) concerns, especially if the design is heavily customized.
- Solution: Review the licensing terms of the reference design and consult with legal experts to ensure compliance with IP regulations. Document all customizations to clearly distinguish your contributions.
Case Studies
Case Study 1: Accelerating Development with a Power Management Reference Design
A consumer electronics company used a power management reference design from a leading semiconductor manufacturer to accelerate the development of a new product. By thoroughly reviewing the documentation, validating the design through simulation and prototyping, and customizing it to fit their specific requirements, they were able to reduce development time by 30% and achieve a highly efficient power management solution.
Case Study 2: Customizing a Communication Module Reference Design
An IoT startup leveraged a communication module reference design to develop a custom solution for their smart devices. They replaced certain components with lower-cost alternatives, adjusted the circuit to meet their power consumption targets, and adapted the PCB layout to fit their compact form factor. By documenting all customizations and conducting regular design reviews, they successfully integrated the reference design into their product, achieving a reliable and cost-effective solution.
Case Study 3: Overcoming Component Obsolescence in an Industrial Control Reference Design
An industrial control systems manufacturer faced component obsolescence issues with a reference design they had been using for several years. By working closely with the component manufacturer and identifying suitable alternative parts, they updated the BOM and revised the schematics and layout accordingly. This proactive approach allowed them to continue using the reference design without disrupting production.
Conclusion
PCB reference designs are powerful tools that can significantly enhance the efficiency and quality of your PCB development process. By following best practices such as choosing the right reference design, thoroughly reviewing documentation, understanding design intent, validating the design, customizing for your application, and leveraging manufacturer support, you can maximize the benefits of reference designs while minimizing potential risks. Additionally, addressing common challenges like component obsolescence, performance variability, and integration issues through careful planning and documentation ensures a smooth and successful design process. Ultimately, effective use of PCB reference designs can lead to faster development cycles, reduced costs, and higher-quality products.