Introduction
In the ever-evolving world of electronics, the complexity of devices continues to grow, often requiring multiple printed circuit boards (PCBs) to achieve the desired functionality. Multi-board systems are common in applications ranging from consumer electronics and automotive systems to industrial machinery and aerospace technology. However, designing and interconnecting multiple PCBs presents unique challenges that go beyond single-board design. This article explores the best practices for multi-board interconnect solutions, providing a comprehensive guide to ensure reliable, efficient, and high-performance multi-board systems.
Understanding Multi-Board Systems
What are Multi-Board Systems?
Multi-board systems consist of two or more PCBs that work together to perform a specific function. These boards are interconnected through various means, such as connectors, cables, or flexible circuits, to form a cohesive system.
Applications of Multi-Board Systems
- Consumer Electronics: Smartphones, laptops, and gaming consoles often use multi-board designs to separate different functionalities (e.g., mainboard, display, and battery).
- Automotive Systems: Modern vehicles incorporate multiple PCBs for engine control, infotainment, and advanced driver-assistance systems (ADAS).
- Industrial Machinery: Complex machinery uses multi-board systems for control, monitoring, and communication.
- Aerospace and Defense: Avionics and defense systems rely on multi-board designs for redundancy, reliability, and modularity.
Key Considerations in Multi-Board Interconnect Solutions
1. Interconnect Types
Choosing the right type of interconnect is crucial for the performance and reliability of multi-board systems.
- Board-to-Board Connectors: These connectors provide a reliable and robust connection between PCBs. They come in various form factors, including mezzanine, stacking, and edge connectors.
- Cables and Harnesses: Flexible cables and harnesses are used for connecting boards that are not in close proximity. They offer flexibility in design but can introduce signal integrity challenges.
- Flex and Rigid-Flex Circuits: Flexible and rigid-flex circuits provide a compact and reliable solution for interconnecting multiple boards, especially in space-constrained applications.
- Backplanes: Backplanes are used in systems where multiple daughterboards need to connect to a single motherboard. They offer high-density interconnects and are common in server and telecommunications equipment.
2. Signal Integrity
Maintaining signal integrity is critical in multi-board systems, especially for high-speed signals.
- Impedance Matching: Ensure consistent impedance across interconnects to prevent reflections and signal degradation.
- Crosstalk: Minimize crosstalk by maintaining adequate spacing between signal lines and using shielding where necessary.
- Length Matching: Match the lengths of differential pairs and critical signals to ensure synchronous arrival and reduce skew.
3. Power Distribution
Efficient power distribution is essential for the reliable operation of multi-board systems.
- Power Planes: Use dedicated power planes to distribute power evenly and reduce voltage drops.
- Decoupling Capacitors: Place decoupling capacitors close to power pins to filter noise and stabilize the power supply.
- Current Capacity: Ensure that interconnects can handle the required current without excessive voltage drop or heating.
4. Thermal Management
Proper thermal management is crucial to prevent overheating and ensure long-term reliability.
- Heat Dissipation: Design interconnects and board layouts to facilitate heat dissipation, using thermal vias and heat sinks where necessary.
- Material Selection: Choose materials with good thermal conductivity for interconnects and PCBs.
- Airflow: Consider the overall system airflow and ensure that it is not obstructed by interconnects or cables.
5. Mechanical Considerations
Mechanical stability and robustness are important for the durability of multi-board systems.
- Mounting and Alignment: Ensure that boards and connectors are properly aligned and securely mounted to prevent mechanical stress and misalignment.
- Vibration and Shock: Design interconnects to withstand vibration and shock, especially in automotive and aerospace applications.
- Connector Durability: Choose connectors with appropriate durability and mating cycles for the application.
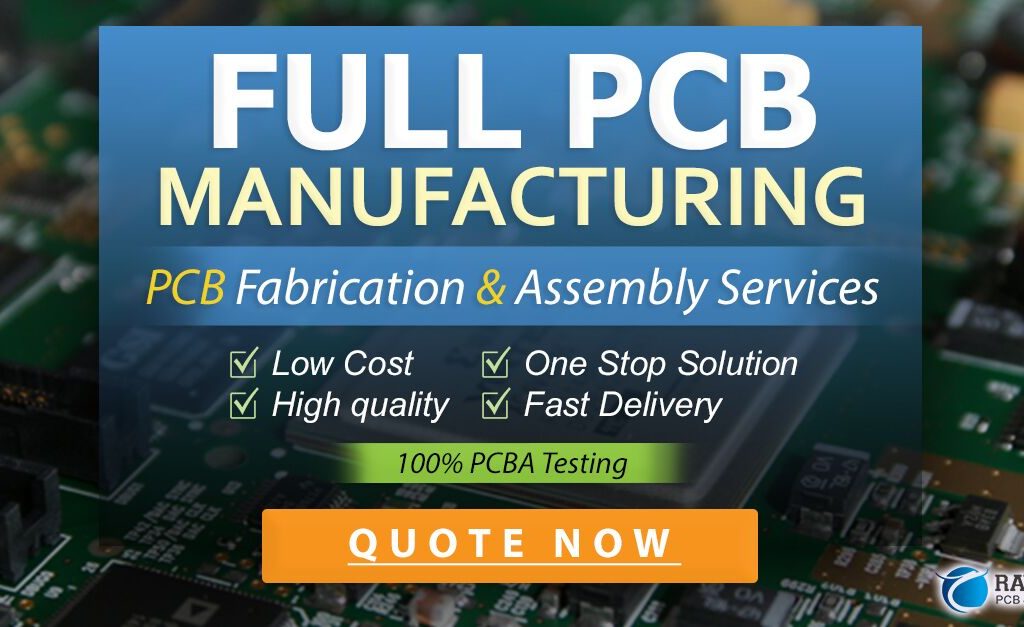
Best Practices for Multi-Board Interconnect Solutions
1. Early Planning and System Architecture
Developing a comprehensive system architecture early in the design process is crucial for successful multi-board interconnect solutions.
- Functional Partitioning: Partition the system into logical functional blocks and assign them to different boards based on performance, power, and space requirements.
- Interconnect Strategy: Define the interconnect strategy, including the types of connectors, cables, or flex circuits to be used.
- Signal and Power Distribution: Plan the distribution of signals and power across the boards, considering signal integrity and power delivery requirements.
2. Use High-Quality Connectors
High-quality connectors are essential for reliable multi-board interconnects.
- Reliability: Choose connectors with proven reliability and appropriate specifications for the application.
- Mating Cycles: Consider the number of mating cycles required and select connectors that can withstand the expected usage.
- Signal Integrity: Use connectors designed for high-speed signals to maintain signal integrity.
3. Optimize Signal Routing
Proper signal routing is critical for maintaining signal integrity and minimizing crosstalk.
- Layer Stack-Up: Plan the layer stack-up to allocate sufficient layers for signal routing and power distribution.
- Differential Pairs: Route differential pairs together with consistent spacing and length matching.
- Ground Planes: Use ground planes to provide a low-impedance return path and reduce electromagnetic interference (EMI).
4. Implement Robust Power Distribution
Efficient power distribution is key to the reliable operation of multi-board systems.
- Power Planes: Use dedicated power planes to distribute power evenly and reduce voltage drops.
- Decoupling Capacitors: Place decoupling capacitors close to power pins to filter noise and stabilize the power supply.
- Current Capacity: Ensure that interconnects can handle the required current without excessive voltage drop or heating.
5. Conduct Thorough Signal Integrity Analysis
Signal integrity analysis is essential for identifying and addressing potential issues in multi-board interconnects.
- Simulation Tools: Use simulation tools to analyze signal integrity, including impedance, crosstalk, and timing.
- Iterative Refinement: Iteratively refine the design based on simulation results to achieve optimal performance.
- Prototyping: Build prototypes to validate the design and identify any signal integrity issues early.
6. Ensure Mechanical Robustness
Mechanical stability and robustness are important for the durability of multi-board systems.
- Mounting and Alignment: Ensure that boards and connectors are properly aligned and securely mounted to prevent mechanical stress and misalignment.
- Vibration and Shock: Design interconnects to withstand vibration and shock, especially in automotive and aerospace applications.
- Connector Durability: Choose connectors with appropriate durability and mating cycles for the application.
7. Collaborate with Manufacturers
Collaborating with PCB and connector manufacturers can help ensure that the multi-board interconnect design is manufacturable and reliable.
- DFM Guidelines: Follow the manufacturer’s design for manufacturability (DFM) guidelines to avoid common pitfalls.
- Prototyping: Build prototypes to validate the design and identify any manufacturing issues early.
- Feedback Loop: Establish a feedback loop with the manufacturer to address any issues and refine the design.
Common Pitfalls and Lessons Learned
1. Insufficient Signal Integrity Analysis
Neglecting signal integrity analysis can result in performance issues and failed prototypes.
- Lesson Learned: Conduct thorough signal integrity analysis and iterative refinement to achieve optimal performance.
2. Poor Power Distribution
Inefficient power distribution can lead to voltage drops, noise, and unreliable operation.
- Lesson Learned: Implement robust power distribution strategies, including dedicated power planes and decoupling capacitors.
3. Ignoring Mechanical Considerations
Overlooking mechanical considerations can result in misalignment, stress, and failure of interconnects.
- Lesson Learned: Ensure proper mounting, alignment, and durability of interconnects to withstand mechanical stress.
4. Overlooking Thermal Management
Neglecting thermal management can lead to overheating and reliability issues.
- Lesson Learned: Incorporate thermal management strategies, such as thermal vias and heat sinks, into the design from the outset.
Case Studies
Case Study 1: Multi-Board System in a Smartphone
A smartphone manufacturer designed a multi-board system with separate boards for the main processor, display, and battery. By using high-quality board-to-board connectors and optimizing signal routing, they achieved reliable interconnects and maintained signal integrity. Thorough signal integrity analysis and prototyping ensured a successful product launch.
Case Study 2: Automotive Control Unit
An automotive control unit required robust interconnects for its multi-board design. The design team implemented a combination of board-to-board connectors and flexible circuits, ensuring reliable connections under vibration and shock. Collaboration with the connector manufacturer and thorough testing validated the design, resulting in a durable and reliable control unit.
Case Study 3: Industrial Machinery
An industrial machinery manufacturer developed a multi-board system for control and monitoring. By using a backplane for high-density interconnects and optimizing power distribution, they achieved efficient and reliable operation. Signal integrity analysis and iterative refinement ensured optimal performance, leading to a successful implementation.
Conclusion
Designing and interconnecting multiple PCBs in a multi-board system presents unique challenges that require careful planning and execution. By following best practices such as early planning, using high-quality connectors, optimizing signal routing, implementing robust power distribution, and conducting thorough signal integrity analysis, engineers can overcome these challenges and create reliable, efficient, and high-performance multi-board systems. Learning from common pitfalls and real-world case studies further enhances the ability to design successful multi-board interconnect solutions. Ultimately, mastering multi-board design enables the development of advanced electronic devices that leverage the full potential of modern technology.