Introduction
The Bill of Materials (BOM) is the backbone of any Printed Circuit Board (PCB) design and manufacturing process. It serves as a comprehensive list of all the components, materials, and assemblies required to build a PCB. However, creating and managing a BOM is not just about listing parts; it involves meticulous organization, accurate part numbering, and strategic planning to ensure smooth production and assembly. This article delves into the intricacies of BOM management, focusing on part numbering systems, organization strategies, and the challenges of managing complex BOMs, often likened to a game of “Packing Tetris.”
Understanding the Bill of Materials (BOM)
What is a BOM?
A BOM is a detailed list of all the items required to manufacture a product. For PCBs, this includes components like resistors, capacitors, integrated circuits, connectors, and other materials such as solder paste and substrates. The BOM is essential for procurement, manufacturing, and assembly processes.
Types of BOMs
- Engineering BOM (EBOM): Created during the design phase, it includes all components and materials required to build the product as designed.
- Manufacturing BOM (MBOM): Used during production, it includes additional details like assembly instructions, packaging, and process steps.
- Service BOM (SBOM): Used for maintenance and repair, it lists parts and assemblies needed for servicing the product.
Part Numbering Systems
Importance of Part Numbering
Part numbering is a critical aspect of BOM management. A well-structured part numbering system ensures that each component is uniquely identified, reducing the risk of errors during procurement and assembly.
Types of Part Numbering Systems
- Intelligent Part Numbers
- Description: Part numbers that encode information about the component, such as its type, value, and manufacturer.
- Advantages: Easy to understand and interpret, reduces the need for additional documentation.
- Disadvantages: Can become complex and unwieldy as the number of components grows.
- Non-Intelligent Part Numbers
- Description: Part numbers that are arbitrary and do not encode any information about the component.
- Advantages: Simple and flexible, easy to manage.
- Disadvantages: Requires additional documentation to understand the part details.
- Hybrid Part Numbers
- Description: Combines elements of both intelligent and non-intelligent systems.
- Advantages: Balances simplicity and informativeness.
- Disadvantages: Can still become complex with a large number of components.
Best Practices for Part Numbering
- Consistency: Use a consistent format for all part numbers.
- Uniqueness: Ensure each part number is unique to avoid confusion.
- Scalability: Design the system to accommodate future growth and new components.
- Documentation: Maintain detailed documentation of the part numbering system and any changes made.
Organizing the BOM
Structuring the BOM
A well-organized BOM is essential for efficient manufacturing and assembly. The structure should reflect the assembly process and make it easy to locate and identify components.
- Hierarchical Structure
- Description: Organizes components into a hierarchy, reflecting the assembly process.
- Advantages: Easy to understand and follow, mirrors the physical assembly process.
- Disadvantages: Can become complex for large assemblies.
- Flat Structure
- Description: Lists all components in a single, flat list without hierarchy.
- Advantages: Simple and easy to manage for small assemblies.
- Disadvantages: Can become unwieldy and difficult to navigate for large assemblies.
Grouping Components
Grouping similar components together can simplify the BOM and make it easier to manage.
- By Function: Group components by their function in the circuit (e.g., power supply, signal processing).
- By Type: Group components by their type (e.g., resistors, capacitors, ICs).
- By Assembly Stage: Group components by the stage of assembly (e.g., SMT, through-hole).
Managing Variants
Many PCB designs have multiple variants, each with slight differences in components or configurations. Managing these variants within the BOM is crucial.
- Variant Management: Use a single BOM with conditional statements to manage different variants.
- Separate BOMs: Create separate BOMs for each variant, ensuring clarity and reducing the risk of errors.
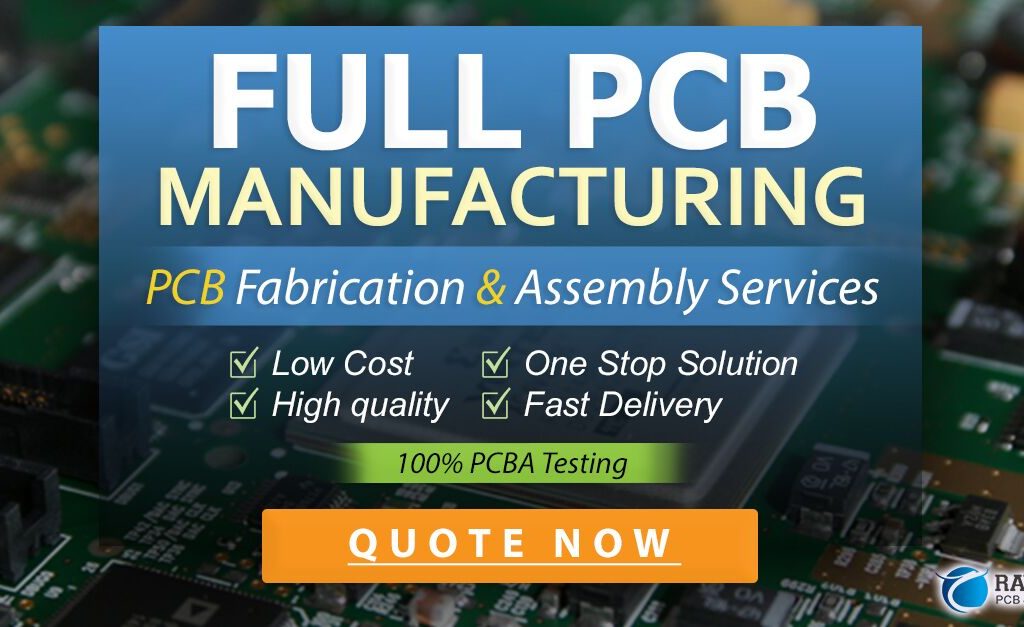
Challenges in BOM Management
Complexity and Volume
As PCB designs become more complex, the number of components in the BOM can grow exponentially, making management increasingly challenging.
- Solution: Use BOM management software to automate and streamline the process.
Component Availability
Component availability can fluctuate due to supply chain issues, obsolescence, or changes in demand.
- Solution: Maintain a flexible BOM and establish relationships with multiple suppliers.
Version Control
Keeping track of changes and ensuring that the correct version of the BOM is used is critical.
- Solution: Implement robust version control practices and use BOM management tools that support versioning.
Collaboration
BOM management often involves multiple stakeholders, including designers, procurement, and manufacturing teams.
- Solution: Use collaborative tools and platforms that allow real-time updates and communication.
BOM Management Tools and Software
Benefits of BOM Management Software
- Automation: Automates repetitive tasks, reducing the risk of errors.
- Integration: Integrates with other tools like CAD, ERP, and PLM systems.
- Visibility: Provides real-time visibility into the BOM, making it easier to track changes and manage components.
Popular BOM Management Tools
- Altium Designer
- Features: Integrated BOM management, real-time updates, and collaboration tools.
- Advantages: Seamless integration with PCB design tools, comprehensive features.
- Arena PLM
- Features: Cloud-based BOM management, version control, and collaboration.
- Advantages: Scalable, easy to use, and accessible from anywhere.
- Siemens Teamcenter
- Features: Comprehensive PLM and BOM management, integration with CAD and ERP systems.
- Advantages: Robust features, suitable for large enterprises.
Case Studies
Case Study 1: Streamlining BOM Management in a Consumer Electronics Company
A consumer electronics company faced challenges with managing the BOM for their complex PCB designs. By implementing Altium Designer and adopting a hierarchical BOM structure, they were able to streamline their BOM management process, reduce errors, and improve collaboration between design and manufacturing teams.
Case Study 2: Managing Variants in an Automotive Electronics Company
An automotive electronics company needed to manage multiple variants of their PCBs. By using Arena PLM and implementing a single BOM with conditional statements, they were able to efficiently manage variants, reduce the risk of errors, and improve time-to-market.
Case Study 3: Overcoming Component Availability Issues in an Industrial Equipment Manufacturer
An industrial equipment manufacturer faced frequent component availability issues. By maintaining a flexible BOM and establishing relationships with multiple suppliers, they were able to mitigate the impact of supply chain disruptions and ensure continuous production.
Conclusion
Managing the Bill of Materials for PCB design is a complex and critical task that requires careful planning, organization, and the right tools. A well-structured part numbering system, organized BOM, and effective management strategies can significantly enhance the efficiency and accuracy of the manufacturing process. By addressing challenges such as complexity, component availability, and version control, and leveraging BOM management software, companies can ensure smooth production and assembly, ultimately leading to successful product launches. Whether it’s a game of “Packing Tetris” or a meticulously organized system, the key to effective BOM management lies in balancing flexibility, accuracy, and collaboration.