Introduction
In the realm of electronics, the design of a Power Distribution Printed Circuit Board (PCB) is a critical aspect that can significantly influence the performance, reliability, and efficiency of the entire system. Whether you’re working on a simple consumer device or a complex industrial machine, the power distribution PCB serves as the backbone, ensuring that every component receives the appropriate voltage and current it needs to function correctly. This article aims to provide a comprehensive guide to designing a power distribution PCB, covering everything from basic principles to advanced techniques, ensuring you become an expert in this essential field.
Understanding the Basics of Power Distribution PCBs
What is a Power Distribution PCB?
A Power Distribution PCB is a specialized type of printed circuit board designed to distribute electrical power from a source (such as a battery or power supply) to various components and subsystems within an electronic device. Unlike signal PCBs, which primarily handle data and control signals, power distribution PCBs are optimized to handle higher currents and voltages, ensuring stable and efficient power delivery.
Key Components of a Power Distribution PCB
- Power Input Connectors: These are the entry points for power into the PCB, typically connected to an external power source.
- Voltage Regulators: These components ensure that the voltage levels are stable and within the required range for each part of the circuit.
- Capacitors and Inductors: Used for filtering and smoothing the power supply, reducing noise and ripple.
- Trace Routing: The conductive paths that carry current from the power source to the various components.
- Heat Dissipation Elements: Such as heat sinks and thermal vias, which help manage the heat generated by high-power components.
- Protection Circuits: Including fuses, circuit breakers, and transient voltage suppressors to protect the PCB from overcurrent, overvoltage, and other potential hazards.
Design Considerations for Power Distribution PCBs
1. Current Carrying Capacity
One of the most critical aspects of power distribution PCB design is ensuring that the traces can handle the required current without overheating or causing voltage drops. The current carrying capacity of a trace depends on its width, thickness (copper weight), and the ambient temperature.
- Trace Width Calculation: Use online calculators or PCB design software to determine the appropriate trace width based on the expected current and acceptable temperature rise.
- Copper Weight: Heavier copper (e.g., 2 oz/ft²) can carry more current than standard 1 oz/ft² copper.
- Thermal Management: Ensure adequate spacing between high-current traces and consider using thermal vias to dissipate heat.
2. Voltage Drop and IR Loss
Voltage drop occurs due to the resistance of the traces, leading to a loss of voltage between the power source and the load. This can be particularly problematic in low-voltage systems.
- Minimize Trace Length: Keep power traces as short as possible to reduce resistance.
- Use Wider Traces: Wider traces have lower resistance, reducing voltage drop.
- Optimize Layer Stackup: Use multiple layers for power distribution to reduce the overall resistance.
3. Power Integrity
Power integrity refers to the quality of the power delivered to the components. Poor power integrity can lead to noise, instability, and malfunction.
- Decoupling Capacitors: Place decoupling capacitors close to the power pins of ICs to filter out high-frequency noise.
- Power Planes: Use dedicated power planes to provide a low-impedance path for current flow.
- Grounding: Ensure a solid ground plane to minimize ground bounce and noise.
4. Thermal Management
High-power components and traces generate heat, which can affect the performance and lifespan of the PCB.
- Heat Sinks: Attach heat sinks to high-power components to dissipate heat.
- Thermal Vias: Use thermal vias to transfer heat from the component to the opposite side of the PCB or to an internal copper layer.
- Component Placement: Place heat-generating components away from sensitive areas and ensure adequate airflow.
5. EMI/EMC Considerations
Electromagnetic Interference (EMI) and Electromagnetic Compatibility (EMC) are critical in power distribution PCBs, especially in high-frequency applications.
- Shielding: Use shielding techniques to contain EMI, such as grounded metal enclosures or conductive coatings.
- Filtering: Implement filtering circuits to reduce noise and prevent it from propagating through the power distribution network.
- Layout Optimization: Carefully plan the layout to minimize loop areas and reduce the potential for EMI.
6. Protection Circuits
Protection circuits are essential to safeguard the PCB and its components from potential damage due to overcurrent, overvoltage, or transient events.
- Fuses and Circuit Breakers: Use fuses or circuit breakers to protect against overcurrent conditions.
- TVS Diodes: Transient Voltage Suppression (TVS) diodes can protect against voltage spikes.
- Reverse Polarity Protection: Implement diodes or MOSFETs to prevent damage from reverse polarity connections.
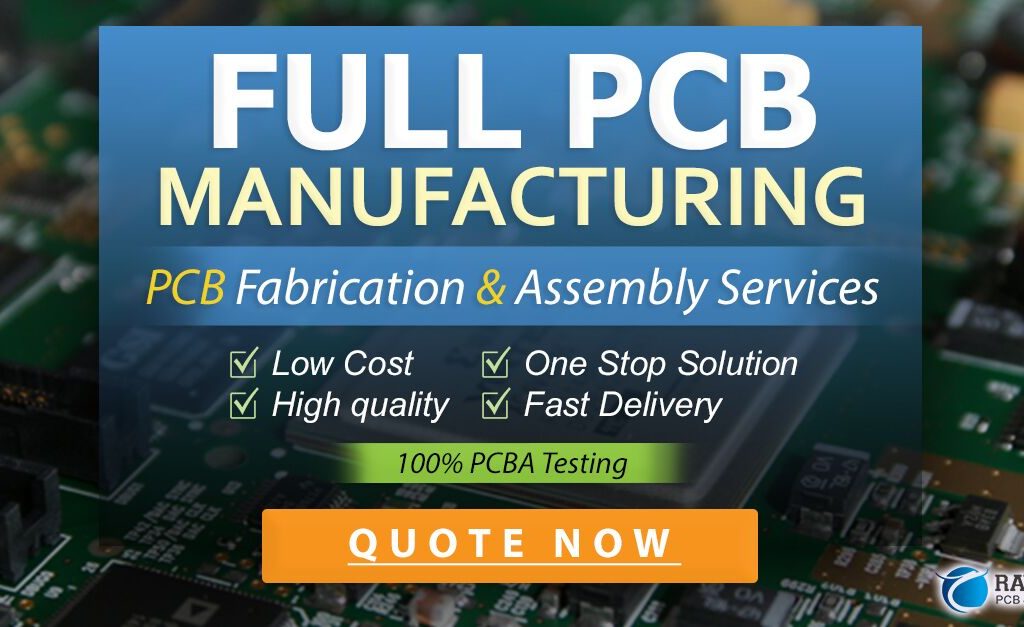
Advanced Techniques in Power Distribution PCB Design
1. Multi-Layer PCBs
Multi-layer PCBs offer several advantages for power distribution, including reduced EMI, improved power integrity, and better thermal management.
- Power and Ground Planes: Dedicate entire layers to power and ground planes to provide low-impedance paths and reduce noise.
- Signal Integrity: Separate signal layers from power layers to minimize interference.
- Via Stitching: Use via stitching to connect multiple ground planes, reducing ground impedance and improving thermal performance.
2. High-Density Interconnect (HDI) PCBs
HDI PCBs are designed with finer traces and smaller vias, allowing for higher component density and improved performance.
- Microvias: Use microvias to connect different layers, reducing the overall size of the PCB.
- Fine Pitch Components: HDI technology allows for the use of fine-pitch components, enabling more compact designs.
- Improved Signal Integrity: The reduced trace lengths and better layer stacking in HDI PCBs can enhance signal integrity.
3. Embedded Components
Embedding components within the PCB can save space, reduce parasitic inductance, and improve performance.
- Passive Components: Embed resistors, capacitors, and inductors within the PCB layers.
- Active Components: In some advanced designs, active components like ICs can also be embedded.
- Thermal Management: Embedded components can be placed closer to heat sinks or thermal vias, improving thermal performance.
4. Simulation and Analysis
Simulation tools are invaluable for optimizing power distribution PCB designs, allowing you to predict and address potential issues before manufacturing.
- Power Integrity Analysis: Use simulation tools to analyze voltage drop, current density, and power plane resonance.
- Thermal Analysis: Simulate thermal performance to identify hot spots and optimize heat dissipation.
- Signal Integrity Analysis: Analyze signal integrity to ensure that high-speed signals are not affected by power distribution noise.
5. Design for Manufacturability (DFM)
Designing for manufacturability ensures that your PCB can be efficiently and reliably produced.
- Component Placement: Follow DFM guidelines for component placement to avoid manufacturing issues.
- Trace and Space: Adhere to the manufacturer’s recommended trace widths and spacing.
- Panelization: Design the PCB for panelization to optimize the manufacturing process and reduce costs.
Best Practices for Power Distribution PCB Design
1. Start with a Clear Schematic
A well-defined schematic is the foundation of any successful PCB design. Ensure that your schematic accurately represents the power distribution network, including all components, connections, and protection circuits.
2. Use a Hierarchical Design Approach
Break down the power distribution network into smaller, manageable sections. This hierarchical approach makes it easier to design, simulate, and troubleshoot each part of the network.
3. Optimize Component Selection
Choose components that are specifically designed for power distribution applications. Consider factors such as current rating, voltage rating, thermal performance, and package size.
4. Follow Industry Standards
Adhere to industry standards and guidelines for PCB design, such as IPC-2221 for generic PCB design and IPC-2152 for determining current-carrying capacity.
5. Collaborate with Manufacturers
Work closely with your PCB manufacturer to ensure that your design meets their capabilities and requirements. Early collaboration can help avoid costly redesigns and delays.
6. Test and Validate
After manufacturing, thoroughly test and validate the power distribution PCB to ensure it meets the design specifications. Use tools such as oscilloscopes, multimeters, and thermal cameras to verify performance.
Conclusion
Designing a power distribution PCB is a complex but rewarding task that requires a deep understanding of electrical principles, thermal management, and manufacturing processes. By following the guidelines and best practices outlined in this article, you can become an expert in designing power distribution PCBs that are efficient, reliable, and optimized for performance. Whether you’re working on a simple project or a complex system, mastering the art of power distribution PCB design will undoubtedly enhance the quality and success of your electronic designs.