Mixed-signal PCB design, which combines both analog and digital circuits, is a critical aspect of modern electronics. One of the most important components in mixed-signal systems is the Analog-to-Digital Converter (ADC), which bridges the gap between the analog and digital domains. The performance of an ADC is heavily influenced by its sampling rate and the layout of the PCB. This article provides an in-depth exploration of ADC sampling rates and layout considerations for mixed-signal boards, offering practical insights and best practices to ensure optimal performance.
1. Understanding ADC Sampling Rate
1.1 What is ADC Sampling Rate?
The sampling rate of an ADC refers to the number of samples it takes per second from an analog signal to convert it into a digital representation. It is typically measured in samples per second (SPS) or Hertz (Hz). For example, an ADC with a sampling rate of 1 MSPS (Mega Samples Per Second) can take one million samples every second.
1.2 Importance of Sampling Rate
The sampling rate is a critical parameter because it directly affects the accuracy and fidelity of the digital representation of the analog signal. According to the Nyquist-Shannon sampling theorem, the sampling rate must be at least twice the highest frequency component of the analog signal (known as the Nyquist rate) to avoid aliasing and ensure accurate reconstruction of the signal.
- Aliasing: If the sampling rate is too low, higher-frequency components of the signal can “fold back” into the lower frequency range, causing distortion and errors in the digital output.
- Signal Fidelity: A higher sampling rate allows for better resolution and more accurate representation of the analog signal, especially for high-frequency or rapidly changing signals.
1.3 Choosing the Right Sampling Rate
Selecting the appropriate sampling rate depends on the application and the characteristics of the analog signal:
- Low-Frequency Signals: For signals with low-frequency components (e.g., temperature sensors), a lower sampling rate may suffice.
- High-Frequency Signals: For high-frequency signals (e.g., audio, video, or RF signals), a higher sampling rate is required to capture the details accurately.
- Oversampling: In some cases, oversampling (sampling at a rate much higher than the Nyquist rate) is used to improve resolution and reduce noise.
2. Key Factors Affecting ADC Performance
2.1 Signal-to-Noise Ratio (SNR)
The SNR is a measure of the quality of the ADC’s output. A higher SNR indicates a cleaner signal with less noise. The sampling rate, along with the ADC’s resolution and input signal quality, influences the SNR.
2.2 Quantization Noise
Quantization noise is introduced during the analog-to-digital conversion process. It is inversely proportional to the ADC’s resolution and can be reduced by increasing the sampling rate or using higher-resolution ADCs.
2.3 Jitter
Jitter refers to the timing uncertainty in the sampling process. Excessive jitter can degrade the ADC’s performance, especially at high sampling rates. Careful clock design and layout are essential to minimize jitter.
2.4 Power Consumption
Higher sampling rates generally require more power, which can be a concern in battery-powered or low-power applications. Designers must balance performance and power consumption based on the application’s requirements.
3. Layout Considerations for Mixed-Signal Boards
The layout of a mixed-signal PCB plays a crucial role in ensuring the performance and reliability of the ADC and the overall system. Poor layout practices can lead to noise coupling, signal integrity issues, and degraded ADC performance. Below are key layout considerations for mixed-signal boards:
3.1 Partitioning the PCB
- Analog and Digital Sections: Physically separate the analog and digital sections of the PCB to minimize noise coupling. Place the ADC at the boundary between the two sections.
- Ground Planes: Use separate ground planes for the analog and digital sections, connected at a single point (star ground) to prevent ground loops and noise coupling.
3.2 Power Supply Design
- Decoupling Capacitors: Place decoupling capacitors close to the ADC’s power pins to filter high-frequency noise and ensure stable power delivery.
- Separate Power Rails: Use separate power rails for the analog and digital sections, with appropriate filtering to prevent noise from the digital section from affecting the analog section.
3.3 Signal Routing
- Analog Signal Traces: Route analog signal traces away from digital traces to minimize crosstalk. Use short, direct traces for critical analog signals.
- Differential Pairs: For differential analog signals (e.g., from sensors), route the traces as a tightly coupled differential pair to maintain signal integrity.
- Impedance Matching: Ensure proper impedance matching for high-frequency signals to prevent reflections and signal degradation.
3.4 Clock Distribution
- Clock Traces: Route clock traces carefully to minimize jitter and noise. Use a dedicated clock buffer or oscillator close to the ADC.
- Shielding: Shield clock traces and sensitive analog traces to reduce electromagnetic interference (EMI).
3.5 Thermal Management
- Heat Dissipation: Ensure adequate heat dissipation for the ADC and other components, especially in high-speed or high-power designs. Use thermal vias and heatsinks if necessary.
- Thermal Coupling: Avoid placing heat-generating components (e.g., power regulators) near the ADC or sensitive analog components.
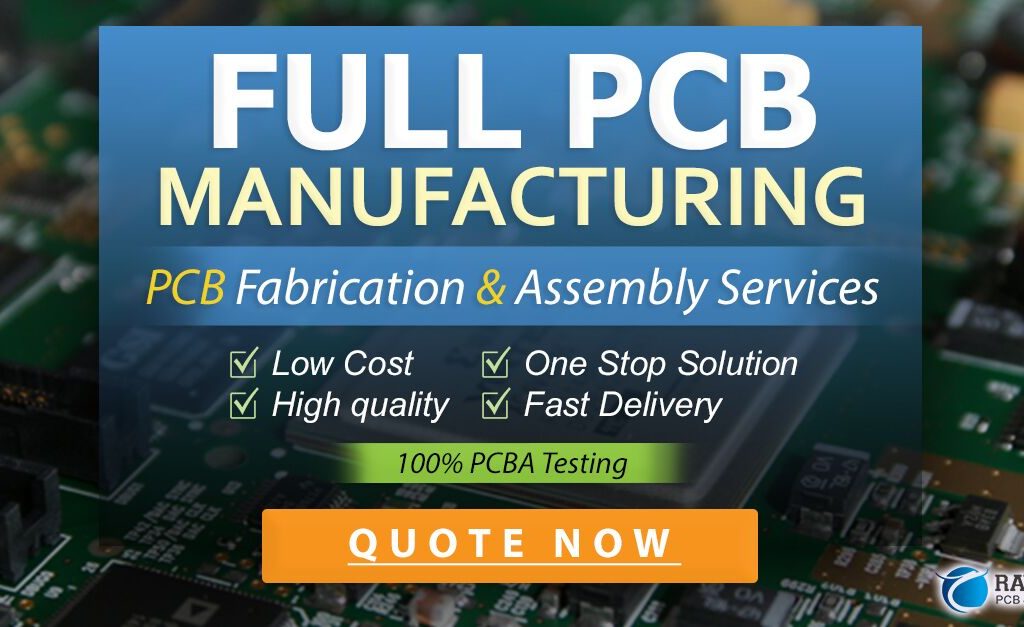
4. Best Practices for ADC Layout
4.1 Use a Multi-Layer PCB
A multi-layer PCB provides better control over signal integrity and noise management. Use dedicated layers for power, ground, and signal routing to minimize interference.
4.2 Minimize Parasitic Capacitance and Inductance
Parasitic capacitance and inductance can degrade the performance of high-speed signals. Use short traces, avoid sharp bends, and minimize the use of vias for critical signals.
4.3 Optimize Component Placement
Place the ADC and its associated components (e.g., decoupling capacitors, clock oscillator) close together to minimize trace lengths and reduce noise.
4.4 Perform Signal Integrity Analysis
Use simulation tools to analyze signal integrity, including crosstalk, reflections, and impedance matching. This helps identify and resolve potential issues before manufacturing.
4.5 Test and Validate the Design
After completing the layout, perform thorough testing and validation to ensure the ADC and the overall system meet performance requirements. Use tools such as oscilloscopes, spectrum analyzers, and signal generators to verify signal quality and noise levels.
5. Case Study: High-Speed ADC Layout
To illustrate the importance of layout considerations, let’s examine a case study involving a high-speed ADC used in a data acquisition system.
5.1 Design Requirements
- ADC Specifications: 16-bit resolution, 100 MSPS sampling rate.
- Input Signal: Analog signal with a bandwidth of 40 MHz.
- Power Supply: 3.3V analog, 1.8V digital.
5.2 Layout Challenges
- Noise Coupling: The high-speed digital signals can couple noise into the analog section, degrading the ADC’s performance.
- Signal Integrity: Maintaining signal integrity for the high-frequency analog input and clock signals is critical.
- Thermal Management: The ADC and other components generate heat, which must be managed to ensure reliability.
5.3 Layout Solutions
- Partitioning: The PCB was partitioned into analog and digital sections, with the ADC placed at the boundary.
- Ground Planes: Separate ground planes were used for the analog and digital sections, connected at a single point.
- Decoupling Capacitors: Decoupling capacitors were placed close to the ADC’s power pins to filter noise.
- Differential Routing: The analog input signal was routed as a differential pair to maintain signal integrity.
- Clock Routing: A dedicated clock buffer was used, and the clock trace was shielded to minimize jitter.
- Thermal Vias: Thermal vias were added under the ADC to dissipate heat effectively.
5.4 Results
The final design achieved excellent performance, with a high SNR and minimal noise coupling. The ADC’s output accurately represented the analog input signal, meeting the system’s requirements.
6. Conclusion
The sampling rate and layout of an ADC are critical factors in the performance of mixed-signal boards. By understanding the principles of ADC sampling and implementing best practices for PCB layout, designers can ensure optimal performance, minimize noise, and achieve reliable operation in mixed-signal systems. Whether you’re designing a high-speed data acquisition system or a low-power sensor interface, careful attention to ADC sampling rate and layout will help you deliver high-quality results.
This guide provides a comprehensive overview of ADC sampling rates and layout considerations for mixed-signal boards. By following the principles and best practices outlined here, you can design mixed-signal PCBs that meet the demands of modern electronics applications.