Printed Circuit Board (PCB) design is a critical aspect of modern electronics, and the stackup—the arrangement of copper and insulating layers—plays a vital role in determining the performance, reliability, and manufacturability of the board. A 6-layer PCB stackup is a popular choice for many applications, offering a balance between complexity, cost, and performance. It is commonly used in high-speed digital designs, RF circuits, and mixed-signal systems where signal integrity, power integrity, and thermal management are critical.
In this article, we will explore the design guidelines for a 6-layer PCB stackup. We will cover the key considerations, layer arrangement strategies, and best practices to help you create a robust and efficient design. Whether you’re designing a high-speed digital system or a mixed-signal board, these guidelines will ensure your 6-layer PCB meets the required performance and reliability standards.
1. Understanding the Basics of PCB Stackup
Before diving into the specifics of a 6-layer stackup, it’s essential to understand the fundamentals of PCB stackup design.
What is a PCB Stackup?
A PCB stackup refers to the arrangement of copper and insulating layers in a multilayer PCB. It defines the number of layers, their order, and the materials used. A well-designed stackup ensures proper signal integrity, power distribution, and thermal management.
Why is Stackup Important?
- Signal Integrity: Proper layer arrangement minimizes crosstalk, electromagnetic interference (EMI), and signal reflections.
- Power Integrity: A well-designed stackup ensures stable power delivery to all components.
- Thermal Management: The stackup influences heat dissipation, which is critical for high-power designs.
- Manufacturability: A good stackup simplifies the manufacturing process and reduces costs.
2. Key Considerations for 6-Layer PCB Stackup Design
Designing a 6-layer PCB stackup requires careful consideration of several factors to ensure optimal performance and manufacturability.
1. Signal Integrity
- Impedance Control: Match the impedance of signal traces to the system requirements (e.g., 50Ω for single-ended signals, 100Ω for differential pairs).
- Crosstalk Reduction: Use ground planes to shield signal layers and minimize crosstalk.
- Signal Layer Placement: Place high-speed signal layers adjacent to ground planes for better return paths.
2. Power Integrity
- Power Plane Distribution: Dedicate layers to power planes to ensure stable voltage distribution.
- Decoupling Capacitors: Place decoupling capacitors close to power pins to reduce noise and improve transient response.
3. Thermal Management
- Copper Thickness: Use thicker copper for power planes to improve current-carrying capacity and heat dissipation.
- Thermal Vias: Add thermal vias to transfer heat from components to inner layers or the opposite side of the board.
4. Manufacturability
- Layer Symmetry: Maintain symmetry in the stackup to prevent warping during manufacturing.
- Material Selection: Choose materials with appropriate dielectric constants and thermal properties for your application.
3. Common 6-Layer PCB Stackup Configurations
There are several ways to arrange the layers in a 6-layer PCB stackup, each with its advantages and trade-offs. Below are three common configurations:
Configuration 1: Signal-Ground-Signal-Power-Signal-Ground
- Layer 1: Top Signal Layer (High-speed signals)
- Layer 2: Ground Plane
- Layer 3: Signal Layer (Low-speed signals)
- Layer 4: Power Plane
- Layer 5: Signal Layer (Low-speed signals)
- Layer 6: Bottom Signal Layer (High-speed signals)
Advantages:
- Excellent signal integrity for high-speed signals on Layers 1 and 6.
- Ground planes provide shielding and reduce EMI.
- Power plane ensures stable voltage distribution.
Disadvantages:
- Limited signal layers for routing.
Configuration 2: Signal-Signal-Ground-Power-Signal-Signal
- Layer 1: Top Signal Layer (High-speed signals)
- Layer 2: Signal Layer (Low-speed signals)
- Layer 3: Ground Plane
- Layer 4: Power Plane
- Layer 5: Signal Layer (Low-speed signals)
- Layer 6: Bottom Signal Layer (High-speed signals)
Advantages:
- More signal layers for routing.
- Ground and power planes provide shielding and stable power.
Disadvantages:
- High-speed signals on Layers 1 and 6 may experience crosstalk if not properly shielded.
Configuration 3: Signal-Ground-Signal-Signal-Power-Ground
- Layer 1: Top Signal Layer (High-speed signals)
- Layer 2: Ground Plane
- Layer 3: Signal Layer (High-speed signals)
- Layer 4: Signal Layer (Low-speed signals)
- Layer 5: Power Plane
- Layer 6: Bottom Ground Plane
Advantages:
- Excellent shielding for high-speed signals on Layers 1 and 3.
- Ground and power planes ensure stable power and reduce EMI.
Disadvantages:
- Limited signal layers for routing.
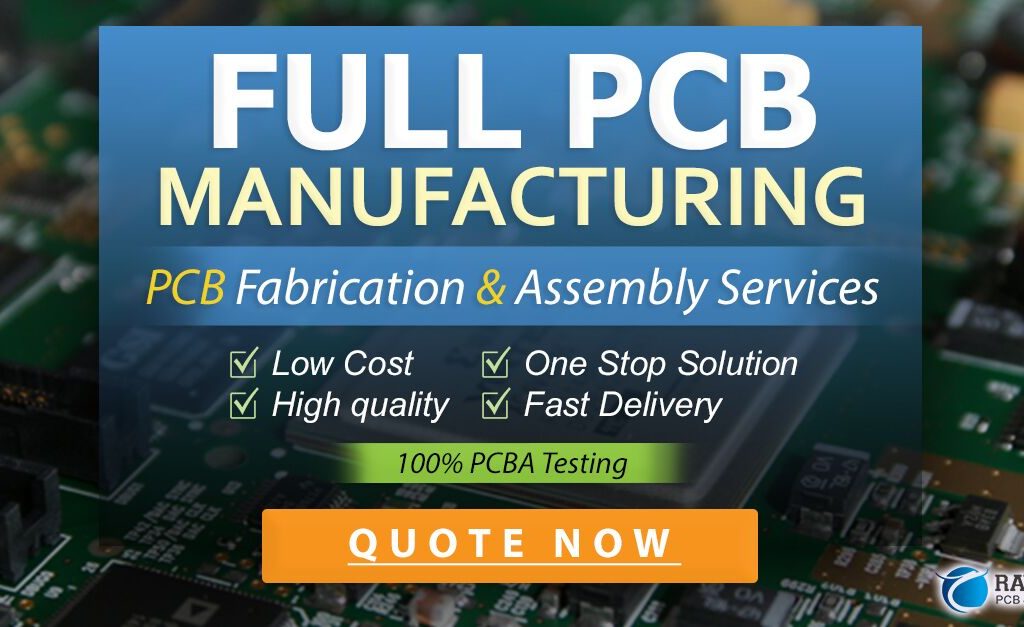
4. Step-by-Step Design Guidelines for a 6-Layer PCB Stackup
Now that we’ve covered the key considerations and common configurations, let’s walk through the step-by-step design process for a 6-layer PCB stackup.
Step 1: Define the Requirements
- Application: Determine the application (e.g., high-speed digital, RF, mixed-signal) and its specific requirements.
- Impedance: Specify the impedance requirements for signal traces.
- Power Requirements: Identify the voltage and current requirements for power planes.
Step 2: Choose the Stackup Configuration
Select a stackup configuration based on the application and requirements. For example, use Configuration 1 for high-speed digital designs or Configuration 3 for mixed-signal designs.
Step 3: Select Materials
- Dielectric Material: Choose a material with the appropriate dielectric constant (Dk) and loss tangent (Df). Common materials include FR-4, Rogers, and Isola.
- Copper Thickness: Select the copper thickness for signal and power layers. Typical values are 1 oz (35 µm) for signal layers and 2 oz (70 µm) for power layers.
Step 4: Assign Layers
Assign layers based on the chosen configuration. For example:
- Layer 1: Top Signal Layer (High-speed signals)
- Layer 2: Ground Plane
- Layer 3: Signal Layer (Low-speed signals)
- Layer 4: Power Plane
- Layer 5: Signal Layer (Low-speed signals)
- Layer 6: Bottom Signal Layer (High-speed signals)
Step 5: Design the Power and Ground Planes
- Power Plane: Ensure the power plane covers the entire layer and provides stable voltage distribution.
- Ground Plane: Use solid ground planes to provide shielding and low-impedance return paths for signals.
Step 6: Route Signal Traces
- High-Speed Signals: Route high-speed signals on Layers 1 and 6, adjacent to ground planes.
- Low-Speed Signals: Route low-speed signals on inner signal layers (Layers 3 and 5).
- Differential Pairs: Route differential pairs with consistent spacing and length matching.
Step 7: Add Decoupling Capacitors
Place decoupling capacitors close to power pins to reduce noise and improve transient response.
Step 8: Implement Thermal Management
- Thermal Vias: Add thermal vias under high-power components to transfer heat to inner layers or the opposite side of the board.
- Heat Sinks: Use heat sinks for components that generate significant heat.
Step 9: Verify the Design
- Signal Integrity Analysis: Perform signal integrity analysis to check for reflections, crosstalk, and impedance mismatches.
- Power Integrity Analysis: Verify stable power distribution and transient response.
- Thermal Analysis: Ensure the design can handle the thermal load without overheating.
5. Best Practices for 6-Layer PCB Stackup Design
To ensure a successful 6-layer PCB stackup design, follow these best practices:
1. Maintain Symmetry
Keep the stackup symmetrical to prevent warping during manufacturing. For example, use the same copper thickness and dielectric material for corresponding layers.
2. Use Ground Planes for Shielding
Place ground planes adjacent to high-speed signal layers to provide shielding and reduce EMI.
3. Minimize Crosstalk
Route high-speed signals on separate layers and use ground planes to minimize crosstalk.
4. Optimize Power Distribution
Use dedicated power planes and place decoupling capacitors close to power pins to ensure stable voltage distribution.
5. Perform Simulations
Use simulation tools to analyze signal integrity, power integrity, and thermal performance before finalizing the design.
Conclusion
Designing a 6-layer PCB stackup requires careful consideration of signal integrity, power integrity, thermal management, and manufacturability. By following the guidelines and best practices outlined in this article, you can create a robust and efficient design that meets the performance and reliability requirements of your application.
For your boss or team, understanding the importance of a well-designed stackup can lead to better product performance, reduced costs, and faster time-to-market. Whether you’re working on a high-speed digital system or a mixed-signal board, these guidelines will help you achieve success in your PCB design projects.