Rigid-flex PCBs combine rigid PCBs and flexible circuits
Rigid-flex PCBs, also known as rigid flex circuits or flex-rigid boards, combine rigid printed circuit boards (PCBs) and flexible circuits into a single structure. They provide designers with the ability to produce 3D, interconnected electronic assemblies.
Rigid flex PCBs contain both rigid sections, made of materials like FR-4, and flexible sections made of materials like polyimide. The rigid areas provide mechanical support and mounting surfaces, while the flexible areas allow dynamic flexing and 3D configuration.
Components can be mounted on both rigid and flex sections.
Advantages of Rigid Flex PCBs
Here are some of the key benefits offered by rigid flex circuits:
- 3D configuration – Rigid flex PCBs can be folded and shaped into 3D structures, enabling innovative and space-saving product designs.
- Flexibility – Dynamic flexing is possible in certain areas to accommodate movement or vary form factors.
- Reliability – Rigid portions provide stability while flexible portions allow motion without compromising circuit integrity.
- Weight savings – By eliminating wires and connectors, rigid flex PCBs are lighter than using separate rigid PCBs and cables.
- Enhanced performance – Superior electrical performance is achieved through integrated, interleaved rigid and flex sections.
How Rigid Flexible Printed Circuit Boards Are Constructed
Rigid flex PCB construction involves combining rigid and flexible circuit technologies into a single assembly. Here are the main construction steps:
- Fabricate separate rigid and flex circuits
- Align layers and laminate together using adhesive sheets
- Etch to form tracks and vias
- Connect circuits using plated through holes
- Solder components on rigid sections
- Shielding and/or conformal coating as needed
- Singulate into separate rigid flex boards
Rigid sections consist of rigid laminates like FR-4 with copper layers processed using standard PCB fabrication. Flex sections use thin polyimide laminates with copper traces. The two are integrated using adhesive sheets or thermal bonding.
Plated through holes and vias provide interconnection points between the rigid and flex sections. Components are soldered onto the rigid portions, while the flexible sections remain component-free.
Typical Applications of Rigid Flexible PCBs
Some common applications that benefit from using rigid flex PCB technology include:
- Medical Devices – Hearing aids, wearables, implants
- Military/Aerospace – Avionics, navigation, communications
- Consumer Electronics – Cellphones, laptops, cameras
- Automotive – Instrument clusters, engine control units
- Industrial – Robotics, automation equipment
Rigid flex PCBs support complex 3D arrangements in small spaces, dynamic flexing actions, and clean interconnectivity between different modules – ideal for many advanced electronic devices.
Design Considerations for Rigid Flex Circuits
Designing effective rigid flex PCBs requires paying attention to flex, component layout, layer stackup, and other considerations:
Flex design
- Minimum bend radius
- Flex thickness
- Polyimide vs polymide adhesive
- Copper thickness – 1oz or 2oz
- Stiffeners to control bend areas
Layer stackup
- Rigid sections – Multiple layers possible
- Flex sections – Typically 2 to 4 layers
- Z-axis interconnects between rigid and flex
Component placement
- Minimize component holes in flex area
- Ensure clearance around drill holes
- Optimize placement for routing
Board outline
- Breakaway tabs
- Non-linear, complex shapes
- Panelization considerations
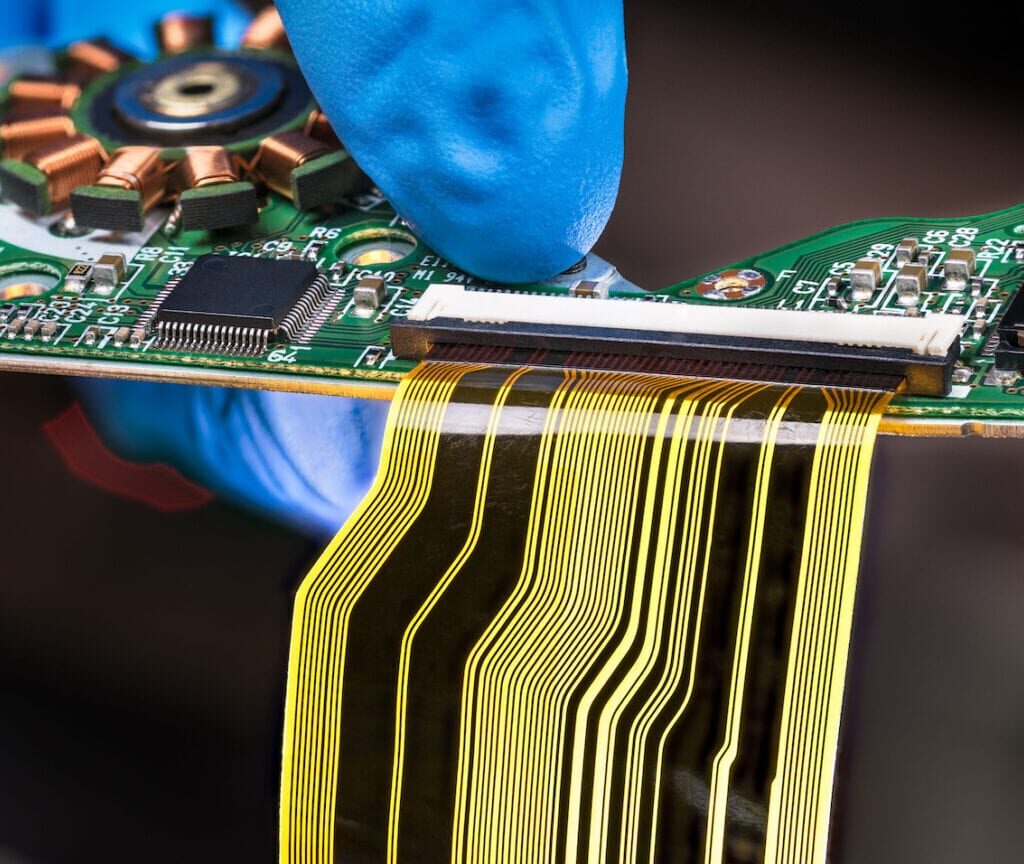
Proper rigid flex design is critical for manufacturing success and reliable performance.
Pros and Cons of Rigid Flexible PCBs
Advantages
- 3D configuration flexibility
- Dynamic flexing ability
- Reduced wiring and connectors
- Lighter weight and lower cost
- More compact, space saving design
- Improved reliability
- Enhanced electrical performance
Disadvantages
- More complex design and fabrication
- Can require special handling during assembly
- Limited number of flex cycles
- Generally more expensive than rigid PCBs
- Repair and rework is more difficult
- Rigid sections can impose minimum bend radius
Manufacturing and Assembling Rigid Flexible Circuits
Producing rigid flex PCBs requires specialized fabrication processes capable of integrating flex and rigid technologies. Photolithographic patterning forms the conductive traces on both rigid and flexible substrates.
Typical rigid flex manufacturing steps:
- Fabrication of individual flexible and rigid layers
- Cleaning and surface treatment
- Layer alignment and lamination
- Drilling of plated through holes
- Electrical testing
- Etching of traces
- Addition of cover layers
- Solder mask and silkscreen application
The rigid portions go through SMT assembly, while components are not mounted on the flexible areas. Care must be taken during assembly to avoid damaging flex areas.
Testing and inspection ensures quality and reliability of the completed rigid flex boards prior to shipment.
Frequently Asked Questions About Rigid Flexible PCBs
What materials are used to make rigid flex PCBs?
The rigid portions of rigid flex PCBs typically use standard FR-4 circuit board laminates. The flexible sections use polyimide films like Kapton or UPILEX with adhesive layers. Flexible substrates are usually 25μm-100μm thick.
What is the minimum bend radius for flexible parts of a rigid flex board?
The minimum bend radius depends on the thickness of the flex layer. A common estimate is to make the minimum bend radius at least 10 times the flex layer thickness. For a 50μm thick polyimide layer, the minimum bend radius would be approximately 0.5mm.
Can components be mounted directly on the flexible sections?
Generally components are only mounted on the rigid portions of a rigid flex PCB. It is best to keep flexible sections component-free to avoid points of high stress and potential cracks. Wires or ribbons can connect the rigid sections.
How many flex cycles can a rigid flex board withstand?
The lifetime flex cycle rating depends on many factors like conductor thickness, polyimide material, bend radius, and flex angle. Typical cycle life ratings range from a few thousand to over 25,000 dynamic flex cycles.
How are components interconnected between rigid and flex sections?
Plated through holes and buried/blind vias can provide interconnects between layers of rigid and flex sections. Careful registration during lamination helps achieve reliable interconnections.
Conclusion
Rigid flex PCBs offer unique benefits for many modern electronic devices with their ability to combine rigid board stability and dynamic flexing. While requiring advanced design and manufacturing processes, rigid flex circuits enable lighter, thinner, and more reliable products with enhanced performance. With attention to layout, material selection and assembly processes, rigid flex PCBs can be designed and produced successfully. Continued improvements in flex materials and fabrication will expand rigid flex applications further.