h2. Introduction to Flexible PCBs
Flexible printed circuit boards (flex PCBs) provide connections between components in electronic devices where rigid boards are impractical. They can flex, bend, fold or twist to accommodate space constraints or moving parts within an assembly. Common applications include:
- Wearable electronics
- Medical devices
- Consumer electronics like laptops, mobile phones, cameras etc.
- Automotive electronics
- Internet of Things (IoT) devices
- Aerospace and defense products
Flex PCBs provide several advantages over traditional rigid PCBs:
- Can conform to tight spaces and moving parts
- Lightweight and thin profile
- Highly durable and reliable
- Allows for complex circuit designs
- Can be folded into 3D configurations
- Facilitates assembly by integrating multiple connectors and components
However, flex PCBs require specialized design expertise and manufacturing processes. This guide covers key considerations when selecting a flexible PCB supplier as a designer.
h2. Critical Supplier Capabilities for Flex PCBs
Choosing the right manufacturer is crucial to ensure flex PCB quality, capabilities and on-time delivery. Here are key capabilities to look for:
h3. Proven Experience and Expertise
- Look for manufacturers who are flex PCB specialists, not just rigid PCB shops offering flex as an additional service
- They should have extensive experience designing and producing complex flex circuits
- Ask for customer references from recent flex PCB projects similar to yours
- Ensure they have in-house engineering experts who can provide design support and DFM analysis
h3. Manufacturing Certifications
- Key certifications like ISO 9001 quality management and IPC standards for flex PCB fabrication validate capabilities
- Certified facilities follow standardized processes which improves quality and reliability
h3. Range of Flex Materials and Layer Counts
- Supplier should offer a wide range of flexible materials including polyimide, polyester, PEEK, stainless steel, etc.
- Look for capabilities to produce high layer count flex boards >6 layers
- Availability of different dielectric films, copper weights and laminate thickness provides more design options
h3. Fine Line PCB Capabilities
- Many flex designs require fine features and spacing – trace/space width below 5 mils (~0.127mm)
- Manufacturer should have equipment and processes optimized for high-density interconnects
h3. Rigid-Flex PCB Technology
- Many designs need a combination of flexible and rigid sections in one assembly
- Ensure the supplier has mature rigid-flex fabrication capabilities – laminating flex to rigid layers
h3. Advanced Testing and Inspection
- Flex PCBs require thorough inspection during fabrication
- Supplier should utilize automated optical, electrical, and functional testing
- This ensures reliability – helpful for high-volume or mission-critical applications
h3. Prototyping and Low Volume Support
- Look for quick-turn prototyping capabilities in addition to volume production
- Supplier should be willing to produce low volume orders without high minimums
h2. Supplier Evaluation Criteria
Here are key criteria to assess flexible PCB manufacturers:
Criteria | Details |
---|---|
Years in Business | Look for 10+ years experience in flex PCB manufacturing |
Location | Domestic manufacturing provides better communication and product control |
Types of Customers Served | Experience supporting similar customers suggests ability to manage your projects |
Quality Management | ISO 9001 and IPC certification indicates standardized quality processes |
Manufacturing Capabilities | Assess available materials, layer counts, tolerances, densities etc. |
Technology | Look for latest equipment, automation, software tools for design, DFM, testing etc. |
Supply Chain Management | Evaluate their supply chain relationships and business continuity planning |
NPI Process | Review new product introduction, prototyping, design review and DFM analysis capabilities |
Testing and Inspection | Automated test, inspection and AOI needed for quality and reliability |
Qualifications | Gauge experience of engineering team, facility, manufacturing engineers and operators |
Support Policies | Evaluate support for low volume orders, quick-turnaround, design support etc. |
Pricing and Contracts | Reasonable pricing models, support for long or short term contracts |
Documentation | Clear quality control, manufacturing and testing documentation ensures traceability |
Thoroughly vet potential suppliers based on these criteria before placing production orders. Send initial inquiries to 5-6 suppliers and have detailed discussions on their capabilities. Request facility tours and product samples to make the final selection.
h2. Flex PCB Design Considerations
Collaborate with your chosen manufacturing partner early in the design phase. Here are some flex PCB design guidelines they can provide guidance on:
h3. Layout
- Optimize component placement to minimize flex layer lengths and unnecessary bends
- Avoid sharp 90 degree angles – use rounded corners with large radii
- Watch for clearance between components, copper traces, and board outline
- Plan ahead for rigid sections, connectors, and vias
h3. Materials
- Select flex material based on flexibility, bend cycles, temperature range, chemical resistance needed
- Consider adhesive type, thickness, Tg to withstand soldering and other processes
- Match copper weight to current loads and layout densities
h3. Stackup
- Use thinner dielectrics for tight bend radii while ensuring isolation
- Minimize number of layers where possible
- Balance layer count against space constraints
- Allow for shielding layers if needed
h3. High Density Interconnects
- Use larger pad sizes and capture pads for fine pitch ICs
- Assume reductions in line width/space vs normal fabrication
- Review DFM analysis on trace/space, annular rings, drill sizes, etc.
- Discuss requirements for microvias
Following design best practices will maximize first-pass success and avoid performance issues or delays.
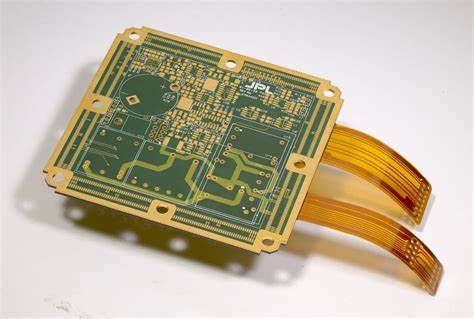
h2. Ordering and Working with Flex Suppliers
Here are some tips for smooth procurement once a flex PCB supplier is selected:
- Provide complete design files – gerbers, drill data, netlist, mechanical drawings etc.
- Do design reviews together and incorporate DFM feedback
- Clearly specify special requirements like material, finishes, tolerances etc.
- Define quality expectations and test/inspection plan upfront
- Start with a small-batch prototype order to de-risk the design
- Leave ample time for manufacturing, especially if re-spins are needed
- Monitor work-in-progress and stay updated on order status
- Once produced, inspect boards thoroughly before accepting the lot
- Provide feedback to improve processes for future orders
- Foster an open and collaborative relationship with supplier reps
- Plan ahead and forecast order volumes when possible
Careful selection of the right flexible PCB manufacturer combined with close collaboration will lead to a successful project. Assess all aspects of capabilities, experience, quality, support and communication when choosing among flex PCB suppliers.
h2. FAQ on Flex PCB Sourcing
h3. What are some leading flex PCB manufacturers I should consider?
Some well-known flexible PCB manufacturers include Compass Circuits, Flexible Circuit Technologies (FCT), All Flex, Minco, Epec, Summit Interconnect, Streamline Circuits and Rayming Technology. However, there are many capable flex PCB suppliers to evaluate.
h3. What minimum order quantities do manufacturers require?
Minimums vary between suppliers. Some provide low-volume prototyping with minimums around 100 pieces, while others require 1,000-2,000+ pieces for volume production orders. Communicate your volume needs upfront.
h3. How long does it take to manufacture flex PCBs?
Typical lead times range from 2-8 weeks, depending on order complexity. Prototypes can often ship in 1-2 weeks. Discuss production schedules with your supplier.
h3. What design support do manufacturers provide?
Many provide free DFM analysis, stackup recommendations, material selection consulting and design reviews. Some even offer free PCB layout services. Utilize their expertise.
h3. How are flex PCBs tested during production?
Standard testing includes automated optical and electrical inspection, resistance measurements, continuity tests and visual inspection during fabrication. Functional testing can also be implemented.
h3. How are flex PCBs packaged for shipping?
Flex boards are wrapped, bagged and boxed to avoid damage during shipment. Some suppliers offer specialized flex board shipping racks. Ensure boards are not creased during transit.
With careful supplier selection, upfront planning and clear communications, designers can produce high-quality flex PCB assemblies that meet requirements for performance, quality and reliability. Leverage your manufacturer’s expertise throughout the procurement process.