Introduction to PCB Quoting
When it comes to electronic product development, printed circuit boards (PCBs) play a crucial role. PCBs are the backbone of most electronic devices, connecting components and enabling functionality. To bring your PCB design to life, you need to obtain a quote from a PCB manufacturer. In this article, we will dive deep into the process of quoting a PCB, covering essential factors, considerations, and best practices to ensure you get an accurate and competitive quote for your project.
Understanding the PCB Quoting Process
Key Factors Influencing PCB Quotes
Several key factors impact the cost of manufacturing a PCB. These factors include:
- PCB Size and Shape
- The dimensions of your PCB (length, width, and thickness) directly influence the cost.
- Larger PCBs require more material and processing time, resulting in higher costs.
-
Complex shapes or non-standard dimensions may incur additional charges.
-
Number of Layers
- PCBs can have varying numbers of layers, from single-sided to multi-layer boards.
- The more layers your PCB has, the higher the manufacturing cost will be.
-
Each additional layer requires more material, processing, and time.
-
Material Selection
- The choice of PCB material affects both performance and cost.
- Common materials include FR-4, high-frequency laminates, and flexible substrates.
-
Specialty materials like high-temperature or low-loss laminates come at a premium.
-
Copper Weight and Trace Width
- The amount of copper used in the PCB layers is specified by the copper weight.
- Higher copper weights provide better current carrying capacity but increase costs.
-
Trace width and spacing also impact manufacturing complexity and cost.
-
Surface Finish
- The surface finish on the PCB pads and exposed copper areas affects solderability and durability.
- Common surface finishes include HASL (Hot Air Solder Leveling), ENIG (Electroless Nickel Immersion Gold), and OSP (Organic Solderability Preservative).
-
Each surface finish has its own characteristics and associated costs.
-
Quantity and Lead Time
- The quantity of PCBs you order significantly influences the unit price.
- Higher quantities often result in lower per-unit costs due to economies of scale.
-
Rush orders or short lead times may incur additional charges.
-
Additional Requirements
- Special requirements such as impedance control, controlled dielectric thickness, or tight tolerances can add to the manufacturing cost.
- Value-added services like assembly, testing, or packaging also affect the overall quote.
Gathering Necessary Information for PCB Quoting
To obtain an accurate PCB quote, you need to provide the manufacturer with comprehensive information about your project. Here’s what you should prepare:
- Bill of Materials (BOM)
- A complete list of components used in your PCB design.
-
Include part numbers, quantities, and any special requirements.
-
Gerber Files
- Industry-standard files that contain the PCB layout and design information.
- Generated from your PCB design software.
-
Include all necessary layers (e.g., copper, solder mask, silkscreen).
-
Drill Files
- Specify the locations and sizes of all the holes in your PCB.
-
Essential for accurate drilling and manufacturing.
-
Fabrication Drawings
- Detailed drawings that provide additional information about your PCB.
-
Include dimensions, tolerances, and any special instructions.
-
PCB Specifications
- Clearly define the PCB requirements, such as layer count, material, copper weight, surface finish, and any special features.
- Provide information about the intended application and operating environment.
Choosing the Right PCB Manufacturer
Selecting a reliable and experienced PCB manufacturer is crucial for ensuring the quality and success of your project. Consider the following factors when choosing a PCB manufacturer:
- Certifications and Standards
- Look for manufacturers with relevant certifications (e.g., ISO 9001, UL, RoHS).
-
Ensure they adhere to industry standards and regulations.
-
Manufacturing Capabilities
- Assess the manufacturer’s capabilities in terms of PCB technology, materials, and processes.
-
Ensure they can handle your specific requirements and complexity.
-
Quality Control Measures
- Inquire about the manufacturer’s quality control processes and procedures.
-
Look for manufacturers with robust testing and inspection systems.
-
Customer Support and Communication
- Evaluate the manufacturer’s responsiveness and communication channels.
-
Good customer support can streamline the quoting process and address any concerns.
-
Pricing and Lead Times
- Compare quotes from multiple manufacturers to ensure competitive pricing.
-
Consider the manufacturer’s lead times and ability to meet your project timeline.
-
References and Reputation
- Seek recommendations from industry peers or online forums.
- Check the manufacturer’s references and customer reviews to gauge their reputation.
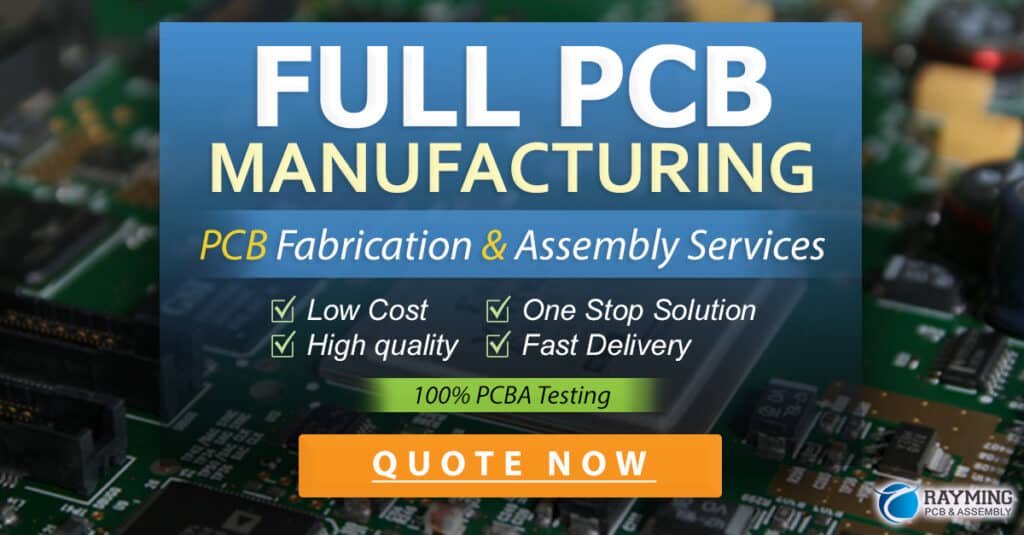
Factors Affecting PCB Quoting
PCB Design Complexity
The complexity of your PCB design significantly impacts the quoting process. Complex designs often require more advanced manufacturing techniques, specialized equipment, and skilled labor, resulting in higher costs. Here are some aspects of PCB design complexity that influence quoting:
- High Density Interconnect (HDI)
- HDI PCBs have finer pitch components, smaller vias, and tighter trace spacing.
- Manufacturing HDI PCBs requires advanced processes and equipment.
-
Higher costs are associated with HDI designs due to the increased complexity.
-
Blind and Buried Vias
- Blind vias connect an outer layer to an inner layer, while buried vias connect inner layers.
- These vias require additional drilling and plating processes.
-
The presence of blind and buried vias increases manufacturing complexity and cost.
-
Controlled Impedance
- Designs requiring controlled impedance for high-speed signals need precise trace width and spacing control.
- Specialized materials and processes are used to achieve controlled impedance.
-
Expect higher costs for controlled impedance requirements.
-
Fine Pitch Components
- Components with fine pitch leads (e.g., BGA, QFN) require precise placement and soldering.
- Manufacturing processes for fine pitch components are more complex and costly.
- The use of fine pitch components can impact the PCB quoting.
Material Selection and Availability
The choice of PCB material plays a significant role in the quoting process. Different materials have varying properties, costs, and availability. Consider the following factors related to material selection:
- Standard vs. Specialty Materials
- Standard PCB materials like FR-4 are widely available and cost-effective.
- Specialty materials, such as high-frequency laminates or flexible substrates, are more expensive.
-
The availability and lead times for specialty materials can impact quoting and delivery.
-
Material Properties
- The electrical, thermal, and mechanical properties of the PCB material affect performance and cost.
- Materials with higher performance characteristics (e.g., low loss, high Tg) come at a premium.
-
Consider the specific requirements of your application when selecting materials.
-
Laminate Thickness and Copper Weight
- The thickness of the PCB laminate and the copper weight impact material costs.
- Thicker laminates and higher copper weights require more material and processing.
-
Specify the appropriate laminate thickness and copper weight based on your design needs.
-
UL Certification
- If your PCB requires UL certification, ensure the selected material is UL-listed.
- UL-certified materials may have limited options and higher costs.
- Factor in the need for UL certification during the material selection process.
Manufacturing Capabilities and Processes
The manufacturing capabilities and processes of the PCB manufacturer significantly influence the quoting process. Different manufacturers have varying equipment, expertise, and process controls. Consider the following aspects:
- PCB Fabrication Technology
- The fabrication technology used by the manufacturer impacts the achievable feature sizes and precision.
- Advanced technologies like HDI or embedded components may not be available at all manufacturers.
-
Ensure the manufacturer’s capabilities align with your PCB design requirements.
-
Quality Control and Testing
- The level of quality control and testing employed by the manufacturer affects the overall PCB quality.
- Manufacturers with stringent quality control measures and comprehensive testing procedures may have higher costs.
-
Consider the required quality level and the associated costs when evaluating manufacturers.
-
Certifications and Standards Compliance
- Manufacturers with relevant certifications (e.g., ISO, AS9100) demonstrate adherence to industry standards.
- Compliance with specific standards (e.g., RoHS, REACH) may be necessary for certain applications.
-
Ensure the manufacturer meets the required certifications and standards for your project.
-
Lead Time and Capacity
- The manufacturer’s production capacity and lead times impact the quoting process.
- Faster lead times or high-volume production may come at a premium.
- Consider your project timeline and volume requirements when evaluating manufacturers.
Optimizing PCB Design for Cost Reduction
While obtaining quotes from PCB manufacturers, there are several design optimization strategies you can employ to reduce costs without compromising functionality or quality. Here are some tips for cost-effective PCB design:
- Minimize PCB Size
- Reduce the overall dimensions of your PCB while maintaining functionality.
- Smaller PCBs require less material and processing, resulting in lower costs.
-
Optimize component placement and routing to achieve a compact design.
-
Simplify Layer Stack-up
- Evaluate the necessity of each layer in your PCB stack-up.
- Reduce the number of layers if possible, as each additional layer adds cost.
-
Consider using a standard layer stack-up offered by the manufacturer.
-
Optimize Routing and Spacing
- Use efficient routing techniques to minimize the total trace length.
- Adhere to the manufacturer’s design rules for minimum trace width and spacing.
-
Avoid unnecessary use of fine-pitch traces or tight spacing requirements.
-
Standardize Components
- Use standard, readily available components whenever possible.
- Avoid using custom or hard-to-find components that may increase costs.
-
Standardization helps in bulk purchasing and reduces sourcing challenges.
-
Consider Panelization
- Panelize multiple PCB designs onto a single panel for production.
- Panelization allows for more efficient use of materials and reduces manufacturing costs.
-
Work with the manufacturer to optimize the panel layout and maximize cost savings.
-
Design for Manufacturing (DFM)
- Follow DFM guidelines provided by the manufacturer.
- Adhere to recommended design rules for pad sizes, hole diameters, and clearances.
-
Incorporate manufacturability considerations early in the design process.
-
Minimize Special Requirements
- Assess the necessity of special requirements like tight tolerances or controlled impedance.
- Special requirements often increase manufacturing complexity and cost.
- Relax tolerances or requirements where possible without compromising functionality.
Design Optimization Strategy | Cost Impact |
---|---|
Minimize PCB Size | Medium |
Simplify Layer Stack-up | High |
Optimize Routing and Spacing | Low |
Standardize Components | Medium |
Consider Panelization | High |
Design for Manufacturing | Medium |
Minimize Special Requirements | High |
Evaluating and Comparing PCB Quotes
Once you have received quotes from multiple PCB manufacturers, it’s essential to evaluate and compare them to make an informed decision. Here are some key factors to consider when assessing PCB quotes:
- Cost Breakdown
- Review the cost breakdown provided in the quotes.
- Identify the major cost drivers, such as material, labor, and tooling.
-
Compare the cost breakdowns across different manufacturers to understand pricing differences.
-
Total Cost of Ownership (TCO)
- Consider the total cost of ownership beyond the initial manufacturing cost.
- Factor in additional expenses like shipping, handling, and potential rework or maintenance.
-
Evaluate the long-term cost implications of choosing a particular manufacturer.
-
Lead Time and Delivery
- Compare the lead times provided by each manufacturer.
- Assess whether the quoted lead times align with your project timeline.
-
Consider the manufacturer’s track record for on-time delivery and reliability.
-
Quality and Reliability
- Evaluate the quality assurance processes and certifications of each manufacturer.
- Look for indicators of quality, such as ISO certifications or customer testimonials.
-
Consider the manufacturer’s reputation for producing reliable and high-quality PCBs.
-
Communication and Support
- Assess the responsiveness and communication quality of each manufacturer during the quoting process.
- Consider the level of technical support and assistance provided.
-
Evaluate the ease of communication and the availability of customer support channels.
-
Value-Added Services
- Compare any value-added services offered by the manufacturers.
- Consider services like assembly, testing, or box build if they align with your project needs.
- Evaluate the cost and benefits of these additional services.
Evaluation Factor | Manufacturer A | Manufacturer B | Manufacturer C |
---|---|---|---|
Cost | $XX | $YY | $ZZ |
Lead Time | X weeks | Y weeks | Z weeks |
Quality | ISO 9001 | UL Certified | ISO 9001 |
Communication | Responsive | Average | Slow |
Value-Added Services | Assembly | Testing | Box Build |
Negotiating and Finalizing the PCB Quote
After evaluating the quotes and selecting a preferred PCB manufacturer, you may have the opportunity to negotiate and finalize the quote. Here are some tips for effective negotiation:
- Clarify Assumptions and Specifications
- Ensure that all assumptions and specifications in the quote are clearly understood by both parties.
-
Address any discrepancies or ambiguities to avoid misunderstandings later in the process.
-
Discuss Cost Drivers
- Identify the main cost drivers in the quote and explore opportunities for cost optimization.
-
Discuss alternative materials, processes, or design modifications that could reduce costs without compromising quality.
-
Negotiate Volume Discounts
- If you have a high-volume order, negotiate volume discounts with the manufacturer.
-
Discuss the possibility of future business or long-term partnerships to secure better pricing.
-
Consider Payment Terms
- Negotiate favorable payment terms that align with your financial capabilities.
-
Explore options for staged payments, such as a deposit and balance upon delivery.
-
Establish Clear Milestones and Deliverables
- Define clear milestones and deliverables in the contract or purchase order.
-
Specify the expected timelines, quality requirements, and acceptance criteria.
-
Maintain Open Communication
- Foster open and transparent communication with the manufacturer throughout the negotiation process.
-
Promptly address any concerns or questions that arise to maintain a positive working relationship.
-
Review and Finalize the Contract
- Carefully review the final contract or purchase order to ensure all agreed-upon terms are accurately captured.
- Seek legal advice if necessary to ensure the contract protects your interests.
Conclusion
Quoting a PCB is a critical step in the electronic product development process. By understanding the factors that influence PCB quotes, gathering the necessary information, and selecting the right manufacturer, you can ensure a smooth and cost-effective PCB manufacturing experience. Optimizing your PCB design for cost reduction, evaluating quotes diligently, and negotiating effectively will help you achieve the best value for your project.
Remember to prioritize quality, reliability, and long-term partnerships when choosing a PCB manufacturer. A successful collaboration between you and the manufacturer will lead to the timely delivery of high-quality PCBs that meet your project requirements.
Frequently Asked Questions (FAQ)
- What information do I need to provide to get an accurate PCB quote?
-
To obtain an accurate PCB quote, you should provide the manufacturer with a bill of materials (BOM), Gerber files, drill files, fabrication drawings, and detailed PCB specifications. The more comprehensive the information you provide, the more accurate the quote will be.
-
How long does it typically take to receive a PCB quote?
-
The time it takes to receive a PCB quote varies depending on the complexity of your design and the responsiveness of the manufacturer. Generally, you can expect to receive a quote within 24 to 48 hours, but it may take longer for more complex projects or during peak seasons.
-
What is the difference between a prototype and a production PCB quote?
-
A prototype PCB quote is typically for a small quantity of boards used for testing and validation purposes. Prototype quotes may have higher per-unit costs due to the low volume and quick turnaround time. On the other hand, a production PCB quote is for larger quantities of boards intended for final product manufacturing. Production quotes often offer lower per-unit costs due to economies of scale.
-
Can I request a quote for PCB assembly as well?
-
Yes, many PCB manufacturers offer assembly services in addition to PCB fabrication. You can request a quote for PCB assembly by providing the necessary information, such as the BOM, assembly drawings, and any specific assembly requirements. Some manufacturers offer turnkey solutions that include both PCB fabrication and assembly.
-
How can I ensure the quality of the PCBs I receive?
- To ensure the quality of the PCBs you receive, choose a reputable