Introduction to PCB Coatings
Printed Circuit Boards (PCBs) are essential components in modern electronic devices. They provide a platform for mounting and interconnecting electronic components, enabling the creation of complex circuits. To ensure the reliability and longevity of PCBs, various coatings are applied to protect them from environmental factors such as moisture, dust, and corrosion. In this article, we will explore the different types of PCB coatings, their properties, and their applications.
Types of PCB Coatings
Conformal Coatings
Conformal coatings are the most common type of PCB coatings. They are thin, protective layers that conform to the shape of the PCB and its components. Conformal coatings provide insulation, moisture resistance, and protection against environmental contaminants. There are several types of conformal coatings, including:
Acrylic Conformal Coatings
Acrylic conformal coatings are widely used due to their excellent electrical insulation properties and ease of application. They offer good moisture and fungus resistance and can be easily removed for rework or repair. Acrylic coatings cure at room temperature and have a fast drying time.
Silicone Conformal Coatings
Silicone conformal coatings provide excellent high-temperature resistance and flexibility. They are resistant to moisture, chemicals, and UV light. Silicone coatings have a low modulus of elasticity, allowing them to withstand thermal cycling and mechanical stress.
Polyurethane Conformal Coatings
Polyurethane conformal coatings offer excellent abrasion and chemical resistance. They provide good moisture and fungus resistance and have a high dielectric strength. Polyurethane coatings are commonly used in harsh industrial environments.
Epoxy Conformal Coatings
Epoxy conformal coatings provide excellent chemical and abrasion resistance. They have a high dielectric strength and offer good moisture and thermal resistance. Epoxy coatings are often used in high-reliability applications, such as aerospace and military electronics.
Parylene Conformal Coatings
Parylene conformal coatings are ultra-thin, pinhole-free coatings that provide excellent moisture and chemical resistance. They are applied using a vapor deposition process, resulting in a uniform and conformal coating. Parylene coatings are biocompatible and are commonly used in medical devices.
Solder Mask Coatings
Solder mask coatings, also known as solder resist coatings, are applied to the copper traces on a PCB to prevent solder from adhering to undesired areas during the soldering process. Solder mask coatings also provide insulation and protection against oxidation and corrosion. There are two main types of solder mask coatings:
Liquid Photoimageable Solder Mask (LPSM)
LPSM is a liquid coating that is applied to the PCB and then exposed to UV light through a photomask. The exposed areas harden, while the unexposed areas remain soluble and can be washed away. LPSM provides excellent resolution and allows for fine-pitch component placement.
Dry Film Solder Mask (DFSM)
DFSM is a solid film that is laminated onto the PCB and then exposed to UV light through a photomask. The exposed areas crosslink and become insoluble, while the unexposed areas can be removed using a developer solution. DFSM is commonly used for high-volume production due to its ease of application and cost-effectiveness.
Potting Compounds
Potting compounds are thick, encapsulating materials that are used to completely fill the voids and gaps around electronic components on a PCB. Potting provides excellent mechanical protection, moisture resistance, and thermal insulation. Common potting compounds include:
Epoxy Potting Compounds
Epoxy potting compounds offer high strength, excellent adhesion, and good chemical resistance. They have a low shrinkage rate and provide excellent thermal and electrical insulation. Epoxy potting is commonly used in transformers, inductors, and high-voltage applications.
Silicone Potting Compounds
Silicone potting compounds provide excellent thermal stability and flexibility. They have a low modulus of elasticity, allowing them to withstand thermal cycling and mechanical stress. Silicone potting is often used in applications exposed to high temperatures or vibrations.
Polyurethane Potting Compounds
Polyurethane potting compounds offer good mechanical strength, flexibility, and chemical resistance. They have a low viscosity, allowing for easy flow and filling of voids. Polyurethane potting is commonly used in automotive and industrial electronics.
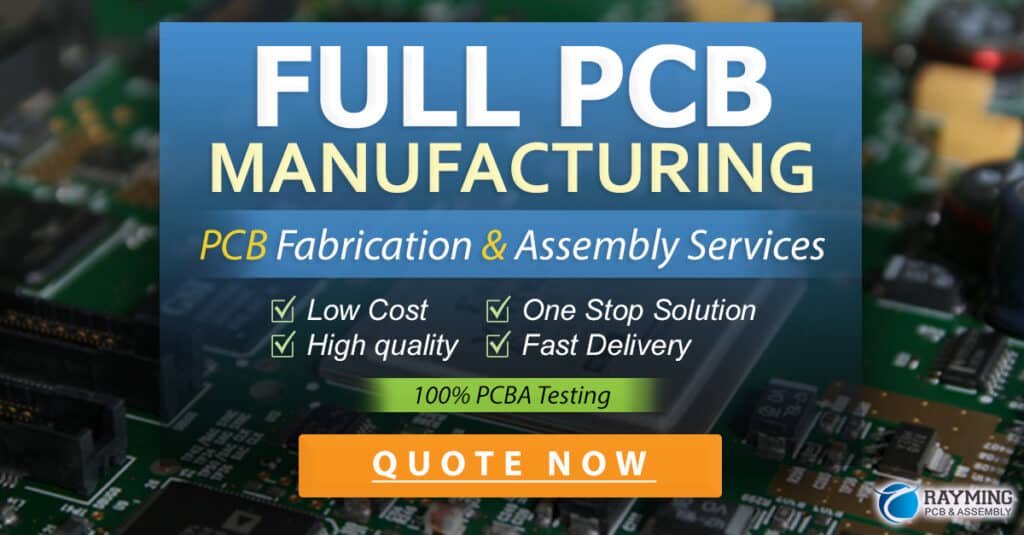
Properties of PCB Coatings
Dielectric Strength
Dielectric strength is a measure of a coating’s ability to withstand electrical breakdown. It is expressed in volts per mil (V/mil) and represents the maximum voltage gradient that the coating can withstand before electrical breakdown occurs. PCB coatings with high dielectric strength provide better insulation and protect against voltage surges.
Moisture Resistance
Moisture resistance is a critical property of PCB coatings, as moisture can lead to corrosion, short circuits, and other reliability issues. Coatings with high moisture resistance prevent the ingress of water and humidity, ensuring the long-term reliability of the PCB.
Chemical Resistance
PCB coatings should be resistant to various chemicals, including acids, bases, solvents, and oils. Chemical resistance prevents the degradation of the coating and the underlying PCB when exposed to harsh environments or cleaning agents.
Thermal Resistance
Thermal resistance is the ability of a coating to withstand high temperatures without degradation. PCB coatings with high thermal resistance protect the PCB and its components from thermal stress and ensure reliable operation in high-temperature environments.
Mechanical Properties
Mechanical properties, such as hardness, flexibility, and abrasion resistance, are important for PCB coatings. Coatings with good mechanical properties protect the PCB from physical damage, vibrations, and mechanical stress.
Application Methods for PCB Coatings
Spray Coating
Spray coating is a common method for applying conformal coatings to PCBs. The coating material is atomized and sprayed onto the PCB surface using a spray gun. Spray coating provides good coverage and can be automated for high-volume production.
Dip Coating
Dip coating involves immersing the PCB into a tank containing the coating material. The PCB is then withdrawn from the tank, and the excess coating is allowed to drip off. Dip coating provides excellent coverage and is suitable for complex PCB geometries.
Brush Coating
Brush coating is a manual method of applying coatings to PCBs. The coating material is applied using a brush, allowing for selective coating of specific areas. Brush coating is suitable for low-volume production or rework.
Selective Coating
Selective coating involves applying the coating material only to specific areas of the PCB, such as components or connectors. Selective coating can be achieved using automated dispensing systems or manual techniques, such as masking or using a dispensing needle.
Choosing the Right PCB Coating
When selecting a PCB coating, several factors should be considered:
-
Environmental conditions: Consider the environmental factors that the PCB will be exposed to, such as temperature, humidity, and chemical exposure.
-
Application requirements: Evaluate the specific requirements of the application, such as insulation, moisture resistance, and thermal stability.
-
Compatibility: Ensure that the coating material is compatible with the PCB substrate, components, and soldering processes.
-
Reworkability: Consider the ease of removing the coating for rework or repair purposes.
-
Cost: Compare the cost of different coating options, considering both material and application costs.
PCB Coating Challenges and Considerations
Coating Thickness
Achieving the optimal coating thickness is crucial for the effectiveness of PCB coatings. Insufficient thickness may not provide adequate protection, while excessive thickness can lead to issues such as reduced heat dissipation and component interference. It is important to follow the manufacturer’s guidelines and use appropriate application methods to achieve the desired coating thickness.
Coating Defects
PCB coatings may be subject to various defects, such as pinholes, bubbles, and voids. These defects can compromise the protective properties of the coating and lead to reliability issues. Proper surface preparation, mixing of the coating material, and controlled application processes can help minimize coating defects.
Coating Inspection and Testing
Regular inspection and testing of PCB coatings are necessary to ensure their effectiveness and integrity. Visual inspection can identify visible defects, while electrical testing can verify the insulation and dielectric properties of the coating. Accelerated life testing and environmental stress testing can help evaluate the long-term performance of the coating under simulated operating conditions.
Rework and Repair
PCB coatings may need to be removed for rework or repair purposes. The ease of removal depends on the type of coating and its properties. Some coatings, such as acrylic and urethane, can be easily removed using solvents, while others, like parylene, may require mechanical or thermal removal methods. It is important to consider the reworkability of the coating during the selection process.
Environmental and Safety Considerations
VOC Emissions
Some PCB coatings, particularly solvent-based ones, may contain volatile organic compounds (VOCs) that can be harmful to the environment and human health. It is important to select coatings with low VOC content and follow proper ventilation and safety guidelines during the application process.
Disposal and Recycling
Proper disposal and recycling of PCB coatings are important for environmental sustainability. Coating waste should be handled in accordance with local regulations and disposed of through authorized waste management facilities. Some coating materials, such as solder mask, can be recycled to reduce environmental impact.
Future Trends in PCB Coatings
Nanocoatings
Nanocoatings are an emerging technology that involves the application of nanoscale materials to PCBs. These coatings offer unique properties, such as enhanced thermal conductivity, self-healing capabilities, and improved durability. Nanocoatings have the potential to revolutionize PCB protection and performance in the future.
Environmentally Friendly Coatings
There is a growing trend towards the development and use of environmentally friendly PCB coatings. These coatings are formulated with bio-based materials, have low VOC content, and are recyclable. As environmental regulations become more stringent, the demand for eco-friendly coatings is expected to increase.
Smart Coatings
Smart coatings are a novel concept that involves the integration of sensing and responsive capabilities into PCB coatings. These coatings can detect changes in temperature, humidity, or mechanical stress and adapt their properties accordingly. Smart coatings have the potential to enable self-monitoring and self-healing PCBs, enhancing their reliability and longevity.
Frequently Asked Questions (FAQ)
-
What is the purpose of PCB coatings?
PCB coatings provide protection against environmental factors, such as moisture, dust, and corrosion. They also offer insulation, mechanical protection, and improve the reliability and longevity of PCBs. -
What are the most common types of PCB coatings?
The most common types of PCB coatings are conformal coatings (acrylic, silicone, polyurethane, epoxy, and parylene), solder mask coatings (liquid photoimageable and dry film), and potting compounds (epoxy, silicone, and polyurethane). -
How do I choose the right PCB coating for my application?
When choosing a PCB coating, consider factors such as environmental conditions, application requirements, compatibility with the PCB and components, reworkability, and cost. Consult with coating manufacturers and follow industry guidelines to select the most suitable coating for your specific needs. -
Can PCB coatings be removed for rework or repair?
Yes, most PCB coatings can be removed for rework or repair purposes. The ease of removal depends on the type of coating and its properties. Some coatings, like acrylic and urethane, can be removed using solvents, while others may require mechanical or thermal removal methods. -
Are there environmentally friendly options for PCB coatings?
Yes, there is a growing trend towards the development and use of environmentally friendly PCB coatings. These coatings are formulated with bio-based materials, have low VOC content, and are recyclable. As environmental regulations become more stringent, the demand for eco-friendly coatings is expected to increase.
Conclusion
PCB coatings play a vital role in protecting and enhancing the reliability of electronic devices. From conformal coatings to solder masks and potting compounds, there is a wide range of coating options available to suit different application requirements. When selecting a PCB coating, it is important to consider factors such as environmental conditions, compatibility, and reworkability. As technology advances, new trends in PCB coatings, such as nanocoatings, environmentally friendly formulations, and smart coatings, are expected to shape the future of PCB protection. By understanding the properties, application methods, and challenges associated with PCB coatings, engineers and manufacturers can make informed decisions to ensure the long-term performance and reliability of their electronic products.