Introduction to Rogers PCBs
Rogers PCBs are specialized printed circuit boards that are designed and manufactured using high-frequency laminate materials developed by Rogers Corporation. These materials offer unique properties that make them ideal for applications requiring high performance, reliability, and durability in demanding environments.
Key Characteristics of Rogers PCBs
- Low dielectric constant and dissipation factor
- Excellent thermal and mechanical stability
- High thermal conductivity
- Low moisture absorption
- Consistent electrical properties over a wide frequency range
Rogers PCBs are widely used in various industries, including:
- Telecommunications
- Aerospace and defense
- Automotive
- Medical devices
- Industrial equipment
rogers pcb materials
Rogers Corporation offers a wide range of high-performance laminate materials for PCB fabrication. Some of the most popular materials include:
1. RT/duroid® Laminates
RT/duroid® laminates are PTFE-based materials that offer excellent electrical properties, low dielectric constant, and low dissipation factor. They are ideal for high-frequency applications, such as:
- Microwave and millimeter-wave circuits
- Satellite communications
- Radar systems
- Wireless infrastructure
Material | Dielectric Constant (10 GHz) | Dissipation Factor (10 GHz) | Thermal Conductivity (W/m·K) |
---|---|---|---|
RT/duroid® 5870 | 2.33 | 0.0012 | 0.22 |
RT/duroid® 5880 | 2.20 | 0.0009 | 0.20 |
RT/duroid® 6002 | 2.94 | 0.0012 | 0.60 |
2. RO4000® Series Laminates
RO4000® series laminates are hydrocarbon ceramic materials that offer a combination of good electrical properties and mechanical stability. They are suitable for a wide range of applications, including:
- Wireless communications
- Automotive radar
- Aerospace and defense
- Industrial IoT devices
Material | Dielectric Constant (10 GHz) | Dissipation Factor (10 GHz) | Thermal Conductivity (W/m·K) |
---|---|---|---|
RO4003C™ | 3.38 | 0.0027 | 0.71 |
RO4350B™ | 3.48 | 0.0037 | 0.62 |
RO4835™ | 3.32 | 0.0030 | 0.60 |
3. TMM® Laminates
TMM® laminates are ceramic thermoset polymer materials that offer a balance of electrical and mechanical properties. They are suitable for applications requiring high reliability and performance, such as:
- Wireless base stations
- Antennas
- Radar systems
- Satellite communications
Material | Dielectric Constant (10 GHz) | Dissipation Factor (10 GHz) | Thermal Conductivity (W/m·K) |
---|---|---|---|
TMM® 3 | 3.27 | 0.0020 | 0.70 |
TMM® 4 | 4.50 | 0.0020 | 0.70 |
TMM® 10 | 9.20 | 0.0022 | 0.70 |
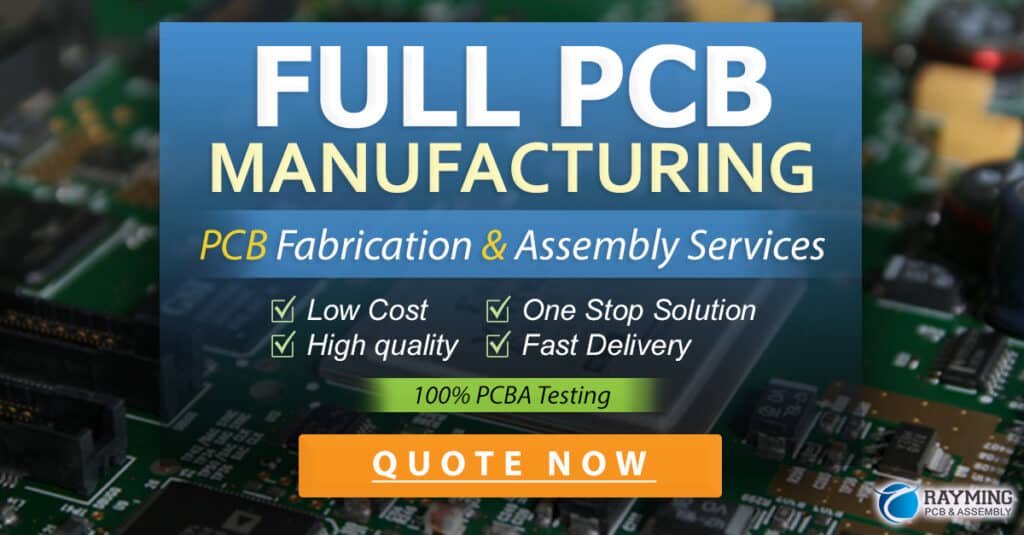
Advantages of Using Rogers PCBs
Rogers PCBs offer several advantages over conventional PCBs, making them the preferred choice for high-frequency and high-performance applications.
1. Low Signal Loss
The low dielectric constant and dissipation factor of Rogers materials minimize signal loss, ensuring better signal integrity and higher performance in high-frequency applications.
2. Improved Thermal Management
Rogers materials have high thermal conductivity, which helps dissipate heat more effectively, preventing thermal damage to components and improving overall system reliability.
3. Dimensional Stability
Rogers PCBs exhibit excellent dimensional stability over a wide temperature range, minimizing the risk of warping or twisting during manufacturing and operation.
4. Moisture Resistance
The low moisture absorption properties of Rogers materials help maintain consistent electrical performance in humid environments, reducing the risk of signal degradation or failure.
5. Design Flexibility
Rogers materials are available in a variety of thicknesses and copper weights, allowing designers to optimize their PCB layouts for specific applications and performance requirements.
Rogers PCB Manufacturing Process
The manufacturing process for Rogers PCBs is similar to that of conventional PCBs, with a few additional considerations due to the unique properties of Rogers materials.
1. Material Selection
The first step in manufacturing a Rogers PCB is selecting the appropriate laminate material based on the application requirements, such as frequency range, thermal management, and mechanical stability.
2. PCB Design
The PCB design is created using specialized software, taking into account the electrical and mechanical properties of the selected Rogers material. The design must adhere to the manufacturer’s guidelines for trace width, spacing, and other parameters.
3. Lamination
The Rogers laminate material is cut to size and laminated with copper foil using heat and pressure. The lamination process must be carefully controlled to ensure proper bonding and minimize stress on the material.
4. Drilling and Plating
Holes are drilled through the laminated board to accommodate components and vias. The holes are then plated with copper to create electrical connections between layers.
5. Etching and Solder Mask Application
The unwanted copper is etched away, leaving the desired circuit pattern. A solder mask is then applied to protect the copper traces and prevent short circuits.
6. Surface Finish
A surface finish, such as ENIG (Electroless Nickel Immersion Gold) or HASL (Hot Air Solder Leveling), is applied to the exposed copper to prevent oxidation and improve solderability.
7. Assembly and Testing
The components are then soldered onto the PCB, and the completed board is tested to ensure proper functionality and performance.
Applications of Rogers PCBs
Rogers PCBs are used in a wide range of high-frequency and high-performance applications across various industries.
1. Telecommunications
- 5G infrastructure
- Wireless base stations
- Satellite communications
- Microwave and millimeter-wave circuits
2. Aerospace and Defense
- Radar systems
- Avionics
- Military communications
- Missile guidance systems
3. Automotive
- Advanced driver assistance systems (ADAS)
- Automotive radar
- Vehicle-to-vehicle (V2V) communication
- Infotainment systems
4. Medical Devices
- MRI and CT scanners
- High-frequency ultrasound
- Wireless medical devices
- Implantable devices
5. Industrial Equipment
- Industrial IoT sensors
- High-speed data acquisition systems
- Power electronics
- Robotics and automation
Frequently Asked Questions (FAQ)
1. What is the difference between Rogers PCBs and conventional PCBs?
Rogers PCBs are made using high-performance laminate materials developed by Rogers Corporation, which offer superior electrical and mechanical properties compared to conventional PCB materials. These properties include low dielectric constant, low dissipation factor, high thermal conductivity, and excellent dimensional stability.
2. Can Rogers PCBs be manufactured using the same processes as conventional PCBs?
Yes, Rogers PCBs can be manufactured using similar processes as conventional PCBs, such as lamination, drilling, plating, and etching. However, due to the unique properties of Rogers materials, some additional considerations and adjustments may be necessary during the manufacturing process to ensure optimal results.
3. Are Rogers PCBs more expensive than conventional PCBs?
Yes, Rogers PCBs are generally more expensive than conventional PCBs due to the higher cost of the specialized laminate materials and the additional manufacturing considerations required. However, the superior performance and reliability of Rogers PCBs often justify the increased cost for high-frequency and high-performance applications.
4. How do I select the right Rogers material for my application?
Selecting the right Rogers material depends on several factors, including the frequency range, thermal management requirements, and mechanical stability needed for your specific application. It is essential to consult with the manufacturer’s technical support team or a qualified PCB designer to determine the most suitable material for your project.
5. Are there any special design considerations when working with Rogers PCBs?
Yes, designing with Rogers PCBs requires adherence to the manufacturer’s guidelines for trace width, spacing, and other parameters to ensure optimal performance and manufacturability. Additionally, designers must take into account the unique electrical and mechanical properties of the selected Rogers material when creating the PCB layout.
Conclusion
Rogers PCBs are a crucial component in many high-frequency and high-performance applications, offering superior electrical and mechanical properties compared to conventional PCBs. By understanding the key characteristics, materials, and manufacturing processes involved in creating Rogers PCBs, designers and engineers can leverage these advanced materials to develop innovative solutions for a wide range of industries, from telecommunications and aerospace to automotive and medical devices.