The Importance of PCB Production in the Electronics Industry
PCBs have revolutionized the electronics industry by providing a reliable and efficient means of connecting electronic components. The benefits of using PCBs include:
- Miniaturization: PCBs allow for the compact arrangement of components, enabling the creation of smaller and more portable devices.
- Reliability: Properly designed and manufactured PCBs ensure stable connections and minimize the risk of short circuits or component failures.
- Mass production: PCBs can be produced in large quantities, reducing manufacturing costs and enabling the widespread availability of electronic devices.
- Customization: PCBs can be designed to meet specific requirements, allowing for the creation of unique and specialized electronic products.
The PCB Design Process
The PCB design process involves several key steps:
Schematic Design
The first step in PCB design is creating a schematic diagram that represents the electrical connections between components. This diagram serves as a blueprint for the PCB layout and helps ensure that the circuit functions as intended.
Component Selection
Based on the schematic, appropriate components are selected, taking into account factors such as power requirements, operating conditions, and cost.
PCB Layout
Using specialized software, the PCB layout is created by arranging the components and routing the connections between them. The layout must adhere to design rules and guidelines to ensure proper functionality and manufacturability.
Design Verification
Before proceeding to fabrication, the PCB design undergoes thorough verification to check for errors, such as short circuits, missing connections, or design rule violations. Simulations may also be performed to assess the circuit’s performance and electromagnetic compatibility.
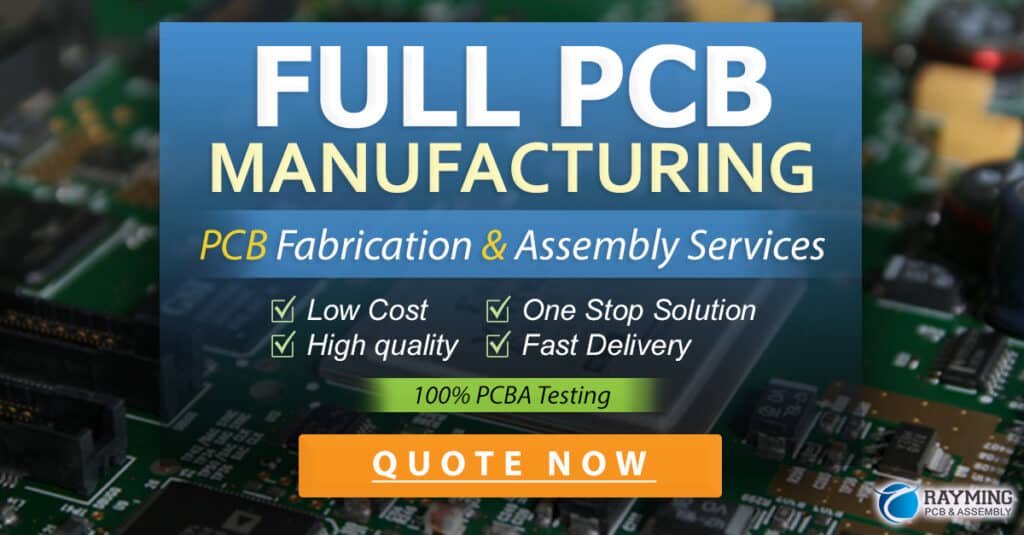
PCB Fabrication Techniques
Once the PCB design is finalized, it moves to the fabrication stage. The most common PCB fabrication techniques include:
Etching
In this process, a copper-clad substrate is selectively etched to remove unwanted copper, leaving behind the desired conductive traces. Photoresist and chemical etchants are used to achieve the precise patterns.
Drilling
Holes are drilled through the PCB substrate to accommodate through-hole components and provide interconnections between layers in multi-layer boards.
Plating
Copper plating is applied to the drilled holes and the surface of the PCB to improve conductivity and protect the copper traces from oxidation.
Solder Mask Application
A protective layer of solder mask is applied to the PCB surface, covering the copper traces while leaving the pads and other areas that require soldering exposed.
Silkscreen Printing
Text, logos, and component outlines are printed on the PCB surface using silkscreen printing to aid in assembly and identification.
PCB Assembly Methods
After fabrication, the PCB undergoes the assembly process, where electronic components are attached to the board. The two primary PCB assembly methods are:
Through-Hole Assembly (THA)
In THA, components with long leads are inserted through holes in the PCB and soldered to pads on the opposite side. This method is suitable for larger components and provides strong mechanical connections.
Surface Mount Assembly (SMA)
SMA involves placing components directly onto pads on the PCB surface and soldering them in place. This method allows for smaller components and higher component density compared to THA.
The choice between THA and SMA depends on factors such as component availability, board size constraints, and production volume.
Quality Control in PCB Production
To ensure the reliability and performance of PCBs, strict quality control measures are implemented throughout the production process. Some key quality control techniques include:
Visual Inspection
PCBs are visually inspected for defects such as incorrect component placement, solder bridges, or damaged components.
Automated Optical Inspection (AOI)
AOI systems use high-resolution cameras and image processing algorithms to detect assembly defects and ensure proper component placement.
X-Ray Inspection
X-ray imaging is used to inspect hidden solder joints, such as those under Ball Grid Array (BGA) components, for defects like voids or insufficient solder.
Electrical Testing
PCBs undergo various electrical tests, including continuity testing, insulation resistance testing, and functional testing, to verify that they meet the specified electrical requirements.
Environmental Testing
PCBs may be subjected to environmental tests, such as temperature cycling, humidity exposure, or vibration testing, to assess their durability and reliability under different operating conditions.
Advancements in PCB Production Technology
PCB production technology continues to evolve, driven by the demand for smaller, faster, and more complex electronic devices. Some notable advancements include:
High-Density Interconnect (HDI) PCBs
HDI PCBs feature finer trace widths, smaller vias, and higher component density, enabling the creation of more compact and sophisticated electronic devices.
Flexible and Rigid-Flex PCBs
Flexible PCBs use thin, flexible substrates that allow for bending and folding, making them suitable for applications where conformity to irregular shapes is required. Rigid-flex PCBs combine rigid and flexible sections, offering both stability and flexibility.
Embedded Components
Embedding components within the PCB substrate, rather than placing them on the surface, can further reduce board size and improve signal integrity.
3D Printing of PCBs
Advancements in 3D printing technology have opened up the possibility of printing PCBs with complex geometries and integrated components, potentially revolutionizing PCB production in the future.
PCB Production and Environmental Considerations
As with any manufacturing process, PCB production has environmental implications that must be addressed. Some key considerations include:
Material Selection
Choosing environmentally friendly PCB materials, such as halogen-free laminates and lead-free solders, can help reduce the environmental impact of PCB production.
Waste Management
Proper handling and disposal of waste materials, including etchants, spent solvents, and scrap PCBs, is essential to minimize environmental pollution.
Energy Efficiency
Implementing energy-efficient practices, such as optimizing equipment usage and utilizing renewable energy sources, can help reduce the carbon footprint of PCB production facilities.
Recycling and Re-use
Encouraging the recycling and re-use of PCBs and electronic components can help conserve resources and reduce electronic waste.
Frequently Asked Questions (FAQ)
- What is the difference between a single-layer and a multi-layer PCB?
-
A single-layer PCB has conductive traces on only one side of the substrate, while a multi-layer PCB has multiple layers of conductive traces separated by insulating layers, allowing for more complex routing and higher component density.
-
What are the common materials used for PCB substrates?
-
The most common PCB substrate materials are FR-4 (a glass-reinforced epoxy laminate), polyimide (for flexible PCBs), and ceramic (for high-frequency applications).
-
What is the purpose of a solder mask on a PCB?
-
A solder mask is a protective layer applied to the PCB surface that covers the copper traces while leaving the pads and other areas that require soldering exposed. It helps prevent short circuits, protects the traces from oxidation, and provides electrical insulation.
-
What are the advantages of surface mount assembly (SMA) over through-hole assembly (THA)?
-
SMA allows for smaller components and higher component density, resulting in more compact PCBs. It also enables faster and more automated assembly processes compared to THA.
-
How can PCB designers ensure signal integrity in high-speed PCB designs?
- To ensure signal integrity in high-speed PCB designs, designers can use techniques such as impedance matching, proper trace routing, minimizing crosstalk, and implementing ground planes and shielding. They may also utilize simulation tools to analyze and optimize the PCB design for high-speed performance.
Conclusion
PCB production is a crucial process in the electronics industry, enabling the creation of reliable, compact, and customizable electronic devices. From the initial design stages to the final assembly and quality control, each step in the PCB production process plays a critical role in ensuring the functionality and performance of the end product. As technology continues to advance, innovations in PCB production techniques, materials, and design tools will drive the development of even more sophisticated and efficient electronic devices. By understanding the fundamentals of PCB production and staying up-to-date with the latest advancements, engineers and manufacturers can create PCBs that meet the ever-increasing demands of the modern electronics landscape while considering environmental sustainability.