The automotive industry is undergoing a transformation, driven by advancements in autonomous driving, advanced driver-assistance systems (ADAS), and vehicle-to-everything (V2X) communication. At the heart of these technologies lies radar systems, particularly 77 GHz radar, which has become the gold standard for automotive applications due to its high resolution, accuracy, and ability to operate in adverse weather conditions. However, designing printed circuit boards (PCBs) for 77 GHz radar systems presents unique challenges, particularly in terms of routing and signal integrity.
In this article, we will explore the intricacies of designing PCBs for 77 GHz radar systems, focusing on routing strategies and signal integrity considerations. We will cover the key challenges, best practices, and design techniques to ensure optimal performance and reliability in automotive radar applications.
1. Introduction to 77 GHz Radar
What is 77 GHz Radar?
77 GHz radar is a high-frequency radar system used in automotive applications for object detection, collision avoidance, and adaptive cruise control. Operating in the millimeter-wave (mmWave) frequency range, it offers several advantages over lower-frequency radar systems:
- High Resolution: The shorter wavelength (approximately 3.9 mm) enables precise detection of small objects and fine details.
- Long Range: 77 GHz radar can detect objects at distances of up to 200 meters or more.
- Compact Size: The high frequency allows for smaller antennas and compact system designs.
Applications of 77 GHz Radar in Automotive:
- Adaptive Cruise Control (ACC): Maintains a safe distance from the vehicle ahead.
- Autonomous Emergency Braking (AEB): Detects potential collisions and applies the brakes automatically.
- Blind Spot Detection (BSD): Monitors the vehicle’s blind spots and alerts the driver.
- Lane Change Assist (LCA): Assists the driver during lane changes by detecting nearby vehicles.
2. Challenges in 77 GHz Radar PCB Design
Designing PCBs for 77 GHz radar systems is inherently challenging due to the high frequency and sensitivity of the signals. Key challenges include:
1. Signal Integrity
At 77 GHz, even minor imperfections in the PCB layout can cause signal degradation, leading to reduced performance and reliability. Issues such as impedance mismatches, crosstalk, and reflections must be carefully managed.
2. Routing Complexity
The high frequency and short wavelength of 77 GHz signals require precise routing to minimize losses and ensure proper signal propagation. This includes maintaining controlled impedance, minimizing vias, and avoiding sharp bends.
3. Material Selection
The choice of PCB material is critical for 77 GHz radar systems. The material must have low dielectric loss, stable dielectric constant, and good thermal properties to ensure reliable performance.
4. Thermal Management
High-frequency circuits generate significant heat, which can affect the performance and lifespan of the components. Effective thermal management is essential to maintain signal integrity and reliability.
5. Manufacturing Tolerances
The small wavelength of 77 GHz signals means that manufacturing tolerances must be extremely tight. Any deviations in trace width, spacing, or layer alignment can significantly impact performance.
3. Routing Strategies for 77 GHz Radar PCBs
Routing is one of the most critical aspects of 77 GHz radar PCB design. The following strategies can help ensure optimal signal integrity and performance:
1. Controlled Impedance Routing
- Impedance Matching: Ensure that the traces are designed to match the characteristic impedance of the system (typically 50Ω for single-ended signals and 100Ω for differential pairs).
- Trace Width and Spacing: Use precise calculations to determine the appropriate trace width and spacing based on the PCB material and layer stackup.
- Simulation Tools: Use electromagnetic simulation tools to verify impedance and optimize the routing.
2. Minimize Vias
- Via Stubs: Avoid long via stubs, which can cause signal reflections and degrade performance.
- Via Placement: Place vias strategically to minimize their impact on signal integrity. Use blind or buried vias for high-frequency signals.
- Via Size: Use small vias with controlled impedance to reduce parasitic inductance and capacitance.
3. Avoid Sharp Bends
- 45-Degree Bends: Use 45-degree bends instead of 90-degree bends to minimize signal reflections and losses.
- Curved Traces: For critical high-frequency signals, consider using curved traces to further reduce reflections.
4. Differential Pair Routing
- Length Matching: Ensure that the lengths of differential pairs are matched to avoid skew and maintain signal integrity.
- Spacing: Maintain consistent spacing between the traces of a differential pair to ensure proper coupling and impedance control.
5. Shielding and Grounding
- Ground Planes: Use solid ground planes to provide a low-impedance return path for high-frequency signals.
- Shielding: Add shielding around sensitive traces to reduce crosstalk and electromagnetic interference (EMI).
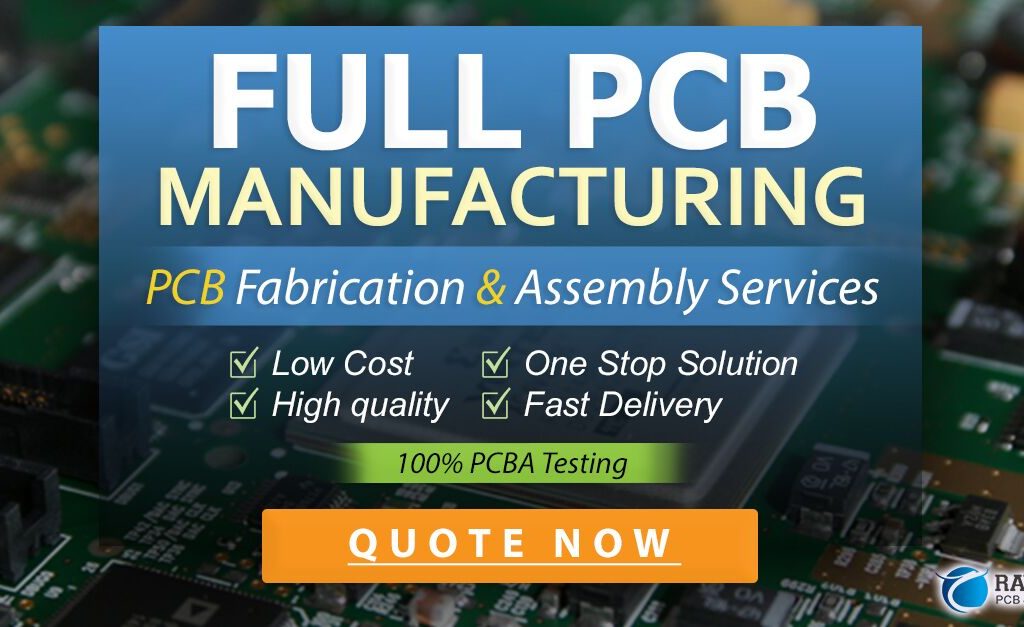
4. Signal Integrity Considerations
Signal integrity is paramount in 77 GHz radar PCB design. The following considerations can help ensure reliable signal transmission:
1. Impedance Control
- Consistent Impedance: Maintain consistent impedance throughout the signal path to minimize reflections and signal loss.
- Impedance Discontinuities: Avoid impedance discontinuities, such as changes in trace width or layer transitions, which can cause signal reflections.
2. Crosstalk Mitigation
- Trace Separation: Increase the separation between high-frequency traces to reduce crosstalk.
- Guard Traces: Use guard traces or ground traces between sensitive signals to provide additional isolation.
3. Reflection Management
- Termination: Use proper termination techniques, such as series or parallel termination, to minimize signal reflections.
- Stub Lengths: Keep stub lengths as short as possible to reduce the impact of reflections.
4. Power Integrity
- Decoupling Capacitors: Place decoupling capacitors close to power pins to reduce noise and ensure stable power delivery.
- Power Plane Design: Use dedicated power planes with low impedance to minimize voltage drops and noise.
5. Thermal Management
- Heat Dissipation: Use thermal vias, heat sinks, and proper PCB layout to dissipate heat effectively.
- Thermal Relief: Add thermal relief pads for components to reduce thermal stress during soldering.
5. Material Selection for 77 GHz Radar PCBs
The choice of PCB material is critical for 77 GHz radar systems. Key considerations include:
1. Dielectric Constant (Dk)
- Stability: Choose a material with a stable dielectric constant over a wide frequency range to ensure consistent performance.
- Low Dk: Materials with a low dielectric constant (e.g., Rogers RO3003) are preferred for high-frequency applications.
2. Loss Tangent (Df)
- Low Loss: Select a material with a low loss tangent to minimize signal attenuation at 77 GHz.
3. Thermal Properties
- Thermal Conductivity: Choose a material with good thermal conductivity to dissipate heat effectively.
- Thermal Expansion: Ensure that the material has a low coefficient of thermal expansion (CTE) to prevent warping and delamination.
4. Manufacturability
- Compatibility: Ensure that the material is compatible with standard PCB manufacturing processes.
- Cost: Balance performance requirements with cost considerations, as high-frequency materials can be expensive.
6. Best Practices for 77 GHz Radar PCB Design
To ensure optimal performance and reliability, follow these best practices:
1. Use Simulation Tools
- Electromagnetic Simulation: Use simulation tools to analyze signal integrity, impedance, and crosstalk.
- Thermal Simulation: Perform thermal simulations to identify hot spots and optimize heat dissipation.
2. Follow Design Guidelines
- Manufacturer Guidelines: Adhere to the PCB manufacturer’s guidelines for trace width, spacing, and layer stackup.
- Industry Standards: Follow industry standards and best practices for high-frequency PCB design.
3. Prototype and Test
- Prototype Fabrication: Fabricate a prototype PCB to validate the design and identify any issues.
- Testing: Perform thorough testing, including signal integrity, power integrity, and thermal performance.
4. Collaborate with Manufacturers
- Early Involvement: Involve the PCB manufacturer early in the design process to ensure manufacturability.
- Feedback Loop: Establish a feedback loop with the manufacturer to address any issues and optimize the design.
Conclusion
Designing PCBs for 77 GHz radar systems is a complex and challenging task, but with the right strategies and considerations, it is possible to achieve optimal performance and reliability. By focusing on routing, signal integrity, material selection, and thermal management, you can create robust and efficient PCBs for automotive radar applications.
For your boss or team, understanding the intricacies of 77 GHz radar PCB design can lead to better decision-making, improved product performance, and a competitive edge in the automotive industry. Whether you’re working on ADAS, autonomous driving, or V2X communication, these insights will help you navigate the challenges of high-frequency PCB design and deliver cutting-edge solutions.