Introduction to 6 Layer PCB Stackup
A 6 layer PCB stackup is a popular choice for complex electronic designs that require higher density and better signal integrity. The six layers provide ample space for routing traces, power planes, and ground planes, allowing for more efficient and reliable PCB designs. In this article, we will discuss the essential guidelines for designing a 6 layer PCB stackup, including layer arrangement, material selection, and via placement.
Understanding the Layers in a 6 Layer PCB Stackup
A typical 6 layer PCB stackup consists of the following layers:
- Top Layer (Signal)
- Ground Plane
- Signal Layer 1
- Power Plane
- Signal Layer 2
- Bottom Layer (Signal)
Each layer serves a specific purpose in the overall PCB design. The top and bottom layers are primarily used for component placement and signal routing, while the inner layers are dedicated to power and ground planes, as well as additional signal routing.
Signal Layers
The signal layers in a 6 layer PCB stackup are responsible for carrying the electrical signals between components. These layers are typically the top, bottom, and two inner layers (layers 3 and 5). When designing the signal layers, consider the following guidelines:
- Route high-speed signals on the top or bottom layer to minimize the distance between the signal trace and the reference plane.
- Use appropriate trace widths and spacing to maintain signal integrity and minimize crosstalk.
- Avoid routing signals over split planes or gaps in the reference plane to prevent discontinuities and reflections.
Power and Ground Planes
The power and ground planes in a 6 layer PCB stackup provide a stable reference for the signal layers and help distribute power to the components. The power plane is typically located on layer 4, while the ground plane is on layer 2. When designing the power and ground planes, consider the following guidelines:
- Use solid planes instead of gridded planes to minimize impedance and provide better shielding.
- Place decoupling capacitors close to the power pins of ICs to minimize noise and ensure stable power delivery.
- Use appropriate via placement and sizes to connect the power and ground planes to the components on the top and bottom layers.
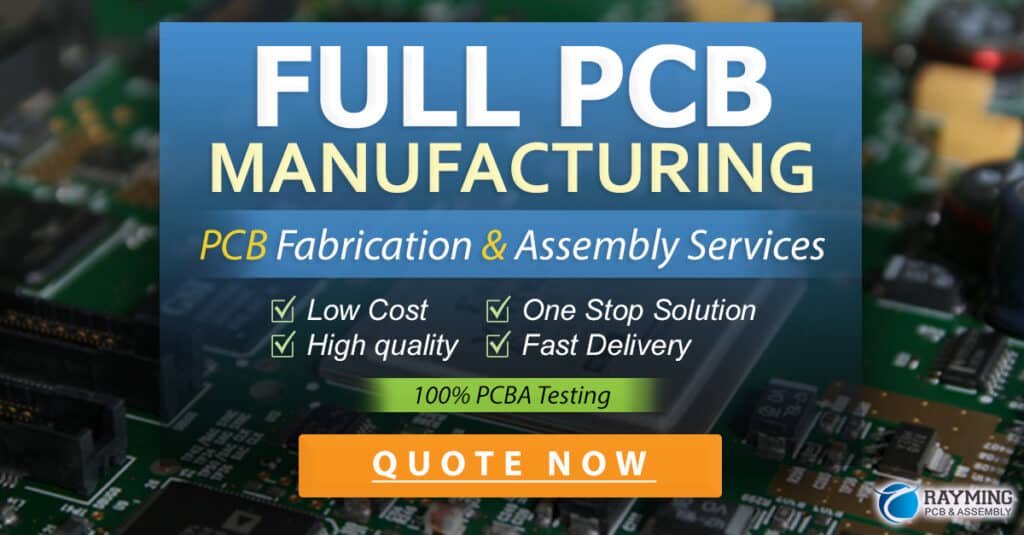
Selecting Materials for a 6 Layer PCB Stackup
The choice of materials for a 6 layer PCB stackup can significantly impact the performance and reliability of the final product. The most common materials used in PCB fabrication are FR-4, Rogers, and Isola.
FR-4
FR-4 is a popular choice for 6 layer PCB stackups due to its low cost and good mechanical properties. However, FR-4 has a relatively high dielectric constant and loss tangent, which can limit its performance at high frequencies.
Rogers
Rogers materials, such as RO4003C and RO4350B, offer superior high-frequency performance compared to FR-4. These materials have lower dielectric constants and loss tangents, making them suitable for high-speed digital and RF applications. However, Rogers materials are more expensive than FR-4 and require specialized processing.
Isola
Isola materials, such as IS410 and IS640, provide a balance between cost and performance. These materials have lower dielectric constants and loss tangents compared to FR-4, making them suitable for high-speed digital applications. Isola materials are less expensive than Rogers materials and are easier to process.
Via Placement and Optimization in a 6 Layer PCB Stackup
Vias are essential components in a 6 layer PCB stackup, as they provide electrical connections between layers. However, vias can also introduce signal integrity issues if not placed and optimized properly.
Via Types
There are three main types of vias used in a 6 layer PCB stackup:
- Through Vias: These vias extend through all layers of the PCB and are used for connecting components on the top and bottom layers to the inner layers.
- Blind Vias: These vias start from either the top or bottom layer and terminate at an inner layer. Blind vias are used for connecting components to the inner layers without going through the entire PCB.
- Buried Vias: These vias are located between the inner layers and do not extend to the top or bottom layer. Buried vias are used for connecting traces on different inner layers.
Via Placement Guidelines
When placing vias in a 6 layer PCB stackup, consider the following guidelines:
- Place vias as close to the component pads as possible to minimize the length of the connecting trace.
- Avoid placing vias in the middle of signal traces, as this can cause impedance discontinuities and reflections.
- Use appropriate via sizes and pad sizes to ensure reliable connections and minimize the impact on signal integrity.
- Consider using via-in-pad design for high-density layouts, where the via is placed directly on the component pad.
Via Optimization Techniques
To optimize the performance of vias in a 6 layer PCB stackup, consider the following techniques:
- Use differential vias for differential signals to maintain signal integrity and minimize crosstalk.
- Implement via shielding by placing ground vias around signal vias to reduce crosstalk and improve signal integrity.
- Use microvias for high-density designs, as they have smaller diameters and can be placed more closely together.
- Optimize via stub length by backdrilling or using blind vias to minimize the unused portion of the via that can cause reflections.
6 Layer PCB Stackup Design Considerations for High-Speed Applications
Designing a 6 layer PCB stackup for high-speed applications requires careful consideration of signal integrity, power integrity, and electromagnetic compatibility (EMC).
Signal Integrity
To maintain signal integrity in a high-speed 6 layer PCB stackup, consider the following guidelines:
- Use controlled impedance design for critical signals to ensure consistent impedance along the trace.
- Implement differential routing for high-speed differential signals to minimize noise and crosstalk.
- Use appropriate termination techniques, such as series termination or parallel termination, to minimize reflections and improve signal quality.
- Minimize the use of vias on high-speed signal traces to reduce discontinuities and reflections.
Power Integrity
Maintaining power integrity is crucial for ensuring reliable operation of high-speed circuits. Consider the following guidelines when designing power distribution in a 6 layer PCB stackup:
- Use dedicated power and ground planes to provide low-impedance power distribution and minimize noise.
- Place decoupling capacitors close to the power pins of high-speed ICs to minimize power supply noise and ensure stable operation.
- Use appropriate via placement and sizes to minimize the impedance of the power distribution network.
- Consider using split planes or isolated power domains for noise-sensitive circuits.
Electromagnetic Compatibility (EMC)
Ensuring electromagnetic compatibility is essential for preventing interference and complying with regulatory requirements. Consider the following EMC guidelines when designing a 6 layer PCB stackup:
- Use proper grounding techniques, such as a solid ground plane and low-impedance ground connections, to minimize electromagnetic emissions.
- Implement shielding techniques, such as via shielding or metal shields, to reduce electromagnetic interference (EMI) and crosstalk.
- Route high-speed signals away from the edges of the PCB to minimize fringing fields and reduce EMI.
- Use appropriate filtering techniques, such as ferrite beads or common-mode chokes, to suppress high-frequency noise and improve EMC performance.
6 Layer PCB Stackup Design Tools and Resources
Designing a 6 layer PCB stackup can be a complex task, but various tools and resources are available to assist designers in creating reliable and high-performance layouts.
PCB Design Software
Many PCB design software packages offer built-in tools for creating and managing PCB stackups. Some popular options include:
- Altium Designer
- Cadence Allegro
- Mentor Graphics PADS
- KiCad
- Eagle
These software packages often include features such as automatic layer assignment, impedance calculation, and Design Rule Checking (DRC) to help designers create accurate and reliable stackups.
Stackup Calculators
Online stackup calculators are useful tools for quickly determining the optimal layer arrangement and material selection for a 6 layer PCB stackup. Some popular stackup calculators include:
- Saturn PCB Toolkit
- EEWeb PCB Stackup Calculator
- Polar Instruments Speedstack
These calculators allow designers to input various parameters, such as layer thicknesses, material properties, and target impedances, and generate a stackup that meets the specified requirements.
Reference Designs and Application Notes
Manufacturers of PCB materials and components often provide reference designs and application notes that demonstrate best practices for designing 6 layer PCB stackups. These resources can be valuable for learning about specific materials, components, or applications. Some notable sources include:
- Rogers Corporation
- Isola Group
- Texas Instruments
- Analog Devices
- Xilinx
By leveraging these reference designs and application notes, designers can gain insights into proven stackup strategies and avoid common pitfalls.
Conclusion
Designing a 6 layer PCB stackup requires careful consideration of layer arrangement, material selection, via placement, and signal integrity. By following the guidelines discussed in this article and utilizing the available tools and resources, designers can create reliable and high-performance 6 layer PCB stackups for a wide range of applications.
Frequently Asked Questions (FAQ)
-
What is the typical layer arrangement in a 6 layer PCB stackup?
A typical 6 layer PCB stackup consists of the following layers: Top Layer (Signal), Ground Plane, Signal Layer 1, Power Plane, Signal Layer 2, and Bottom Layer (Signal). -
What are the main differences between FR-4, Rogers, and Isola materials for 6 layer PCB stackups?
FR-4 is a low-cost material with good mechanical properties but has a relatively high dielectric constant and loss tangent. Rogers materials offer superior high-frequency performance but are more expensive and require specialized processing. Isola materials provide a balance between cost and performance, with lower dielectric constants and loss tangents compared to FR-4. -
What are the three main types of vias used in a 6 layer PCB stackup?
The three main types of vias used in a 6 layer PCB stackup are through vias, blind vias, and buried vias. Through vias extend through all layers of the PCB, blind vias start from either the top or bottom layer and terminate at an inner layer, and buried vias are located between the inner layers and do not extend to the top or bottom layer. -
Why is maintaining power integrity important in high-speed 6 layer PCB stackups?
Maintaining power integrity is crucial for ensuring reliable operation of high-speed circuits. Proper power distribution, decoupling, and via placement help minimize power supply noise and ensure stable operation of high-speed components. -
What are some popular PCB design software packages that offer tools for creating 6 layer PCB stackups?
Some popular PCB design software packages that offer tools for creating 6 layer PCB stackups include Altium Designer, Cadence Allegro, Mentor Graphics PADS, KiCad, and Eagle. These software packages often include features such as automatic layer assignment, impedance calculation, and Design Rule Checking (DRC) to help designers create accurate and reliable stackups.