Introduction
In the world of electronics, voltage regulation is a critical aspect of ensuring the proper functioning of devices. One common challenge designers face is stepping down a high voltage, such as 48V, to a much lower voltage, like 3.3V, which is commonly used in microcontrollers, sensors, and other low-power components. This article provides an in-depth exploration of a 48V to 3.3V Regulators Design Project, covering the design process, component selection, circuit topologies, simulation, and practical considerations. Whether you’re an experienced engineer or a hobbyist, this guide will equip you with the knowledge to design an efficient and reliable voltage regulator.
Understanding the Requirements
Why 48V to 3.3V?
- 48V Systems:
- 48V is a common voltage in industrial, automotive, and telecommunications applications. It is used in Power over Ethernet (PoE), electric vehicles, and data centers due to its efficiency in power distribution.
- 3.3V Systems:
- 3.3V is a standard voltage for modern microcontrollers, sensors, and digital logic circuits. Stepping down 48V to 3.3V is essential for powering these low-voltage components.
Key Design Requirements
- Input Voltage: 48V (with a tolerance range, e.g., 36V to 60V).
- Output Voltage: 3.3V (regulated with low ripple).
- Output Current: Depends on the load (e.g., 100mA for low-power devices or 1A+ for more demanding applications).
- Efficiency: High efficiency is critical to minimize heat dissipation and power loss.
- Size and Cost: Compact design and cost-effective components are often prioritized.
- Safety and Reliability: Overcurrent, overvoltage, and thermal protection are essential.
Voltage Regulation Techniques
There are several approaches to stepping down 48V to 3.3V, each with its advantages and trade-offs. The most common methods include:
- Linear Regulators:
- Simple and low-cost but inefficient for large voltage drops.
- Dissipates excess power as heat, making it unsuitable for high-power applications.
- Switching Regulators (DC-DC Converters):
- Highly efficient and capable of handling large voltage differences.
- More complex but ideal for 48V to 3.3V conversion.
- Transformer-Based Isolated Converters:
- Provides electrical isolation between input and output.
- Suitable for applications requiring isolation but bulkier and more expensive.
For this project, we will focus on switching regulators, specifically buck converters, due to their efficiency and compact design.
Buck Converter Basics
How a Buck Converter Works
A buck converter is a type of DC-DC converter that steps down a higher input voltage to a lower output voltage. It operates by rapidly switching a transistor (usually a MOSFET) to control the energy flow through an inductor. The key components of a buck converter include:
- Switching MOSFET: Controls the energy flow.
- Diode or Synchronous Rectifier: Provides a path for current during the off-state of the MOSFET.
- Inductor: Stores and releases energy to smooth the output voltage.
- Capacitor: Filters the output voltage to reduce ripple.
- Control Circuit: Regulates the switching to maintain the desired output voltage.
Advantages of Buck Converters
- High Efficiency: Typically 85-95% for well-designed circuits.
- Compact Size: Suitable for space-constrained applications.
- Wide Input Voltage Range: Can handle large voltage drops like 48V to 3.3V.
Designing the 48V to 3.3V Buck Converter
Step 1: Define Specifications
- Input Voltage (Vin): 48V (36V to 60V range).
- Output Voltage (Vout): 3.3V.
- Output Current (Iout): 1A (adjustable based on load requirements).
- Switching Frequency (fsw): 500 kHz (common for compact designs).
Step 2: Select the Buck Converter IC
Choosing the right buck converter IC is critical. Key considerations include:
- Input Voltage Range: Must support up to 60V.
- Output Current: Must handle at least 1A.
- Efficiency: Look for ICs with high efficiency at low output voltages.
- Package Size: Smaller packages save space.
Example ICs:
- LM5164 (Texas Instruments): 100V input, 1A output, synchronous buck converter.
- LT8640 (Analog Devices): 65V input, 8A output, high-efficiency buck converter.
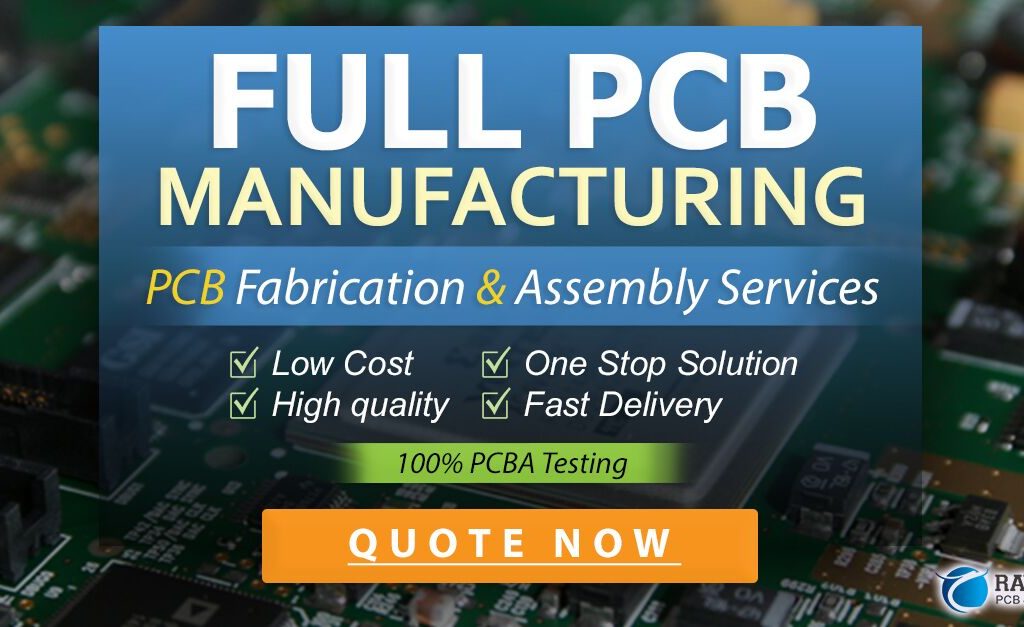
Step 3: Calculate Inductor Value
The inductor value is determined by the desired ripple current and switching frequency. Use the following formula:
[
L = \frac{(Vin – Vout) \cdot Vout}{Vin \cdot \Delta I_L \cdot fsw}
]
Where:
- ( \Delta I_L ) = Ripple current (typically 20-40% of Iout).
For example:
- ( Vin = 48V ), ( Vout = 3.3V ), ( Iout = 1A ), ( fsw = 500 kHz ), ( \Delta I_L = 0.3A ).
- ( L = \frac{(48 – 3.3) \cdot 3.3}{48 \cdot 0.3 \cdot 500000} \approx 6.8 \mu H ).
Step 4: Select Output Capacitor
The output capacitor smooths the output voltage and reduces ripple. Use the following formula to estimate the required capacitance:
[
Cout = \frac{\Delta I_L}{8 \cdot fsw \cdot \Delta Vout}
]
Where:
- ( \Delta Vout ) = Desired output voltage ripple (e.g., 30mV).
For example:
- ( Cout = \frac{0.3}{8 \cdot 500000 \cdot 0.03} \approx 2.5 \mu F ).
Choose a low-ESR ceramic capacitor for best performance.
Step 5: Design Feedback Network
The feedback network sets the output voltage. Use a voltage divider to feed a fraction of the output voltage back to the IC’s feedback pin:
[
Vout = Vref \cdot \left(1 + \frac{R1}{R2}\right)
]
Where:
- ( Vref ) = Reference voltage (typically 0.8V for many ICs).
For ( Vout = 3.3V ):
- Choose ( R2 = 10k\Omega ).
- ( R1 = 10k\Omega \cdot \left(\frac{3.3}{0.8} – 1\right) \approx 31.25k\Omega ).
Step 6: Select Input Capacitor
The input capacitor reduces input voltage ripple and provides stable power to the converter. Choose a capacitor with low ESR and sufficient voltage rating (e.g., 100V).
Step 7: Thermal Considerations
High input-to-output voltage differences can lead to significant power dissipation. Ensure proper heat sinking and thermal management for the IC and other components.
Simulation and Testing
Simulation Tools
Use simulation tools like LTspice, PSpice, or Multisim to verify the design before prototyping. Simulate the circuit under various load conditions to ensure stability and efficiency.
Prototyping and Testing
- Build the Circuit: Assemble the components on a PCB or breadboard.
- Measure Output Voltage: Verify that the output is stable at 3.3V.
- Check Efficiency: Measure input and output power to calculate efficiency.
- Test Under Load: Ensure the regulator can handle the required current without overheating or voltage drop.
Practical Considerations
Component Selection
- Inductor: Choose a high-quality inductor with low DC resistance (DCR) to minimize losses.
- Capacitors: Use ceramic capacitors with low ESR for input and output filtering.
- Diode: If using a non-synchronous buck converter, select a fast-recovery diode.
PCB Layout
- Minimize Trace Lengths: Keep high-current paths short to reduce resistance and inductance.
- Ground Plane: Use a solid ground plane to minimize noise and improve thermal performance.
- Thermal Management: Place heat-generating components (e.g., MOSFET, inductor) away from sensitive parts.
Safety Features
- Overcurrent Protection: Add a fuse or current-limiting circuit.
- Overvoltage Protection: Use a Zener diode or transient voltage suppressor (TVS).
- Thermal Shutdown: Ensure the IC has built-in thermal protection.
Applications of 48V to 3.3V Regulators
- Industrial Automation: Powering sensors and controllers in 48V systems.
- Electric Vehicles: Stepping down battery voltage for low-power electronics.
- Telecommunications: Powering PoE devices and network equipment.
- Renewable Energy: Regulating voltage in solar or wind power systems.
Conclusion
Designing a 48V to 3.3V regulator is a challenging but rewarding project that requires careful consideration of component selection, circuit topology, and thermal management. By using a buck converter, you can achieve high efficiency and compact size, making it ideal for a wide range of applications. Simulation and prototyping are essential steps to ensure the design meets all requirements and performs reliably under real-world conditions.
This project not only enhances your understanding of voltage regulation but also equips you with practical skills in power electronics design. Whether you’re working on industrial systems, automotive electronics, or renewable energy projects, the knowledge gained from this project will be invaluable in your engineering journey.