Introduction
The world of electronics manufacturing is undergoing a transformative shift with the advent of 3D printing technology. Traditionally, the production of Printed Circuit Boards (PCBs) has been a complex, multi-step process involving etching, drilling, and soldering. However, 3D printing is poised to revolutionize this industry by enabling the direct fabrication of PCBs and the generation of intricate printing models. This article delves into the intricacies of 3D printing PCBs, the generation of printing models, and the potential impact of this technology on the electronics manufacturing landscape.
Understanding PCBs and Their Traditional Manufacturing Process
What Are PCBs?
Printed Circuit Boards (PCBs) are the backbone of modern electronics. They provide the mechanical support and electrical connections necessary for electronic components to function. PCBs consist of a non-conductive substrate, typically made of fiberglass, with conductive pathways etched or printed onto the surface. These pathways, known as traces, connect various components such as resistors, capacitors, and integrated circuits.
Traditional PCB Manufacturing
The traditional PCB manufacturing process involves several steps:
- Design and Layout: Engineers use specialized software to design the PCB layout, specifying the placement of components and the routing of traces.
- Printing the Design: The design is printed onto a transparent film, which is then used to create a photomask.
- Etching: The photomask is placed over a copper-clad substrate, and UV light is used to transfer the design onto the substrate. The exposed copper is then etched away, leaving behind the desired traces.
- Drilling: Holes are drilled into the substrate to accommodate through-hole components and vias.
- Plating and Soldering: The holes are plated with conductive material, and components are soldered onto the board.
- Testing and Inspection: The finished PCB is tested for functionality and inspected for defects.
While this process is well-established, it is time-consuming, requires specialized equipment, and generates significant waste. This is where 3D printing comes into play.
3D Printing PCBs: A New Paradigm
What is 3D Printing?
3D printing, also known as additive manufacturing, is a process of creating three-dimensional objects by depositing material layer by layer based on a digital model. This technology has been widely adopted in various industries, from aerospace to healthcare, due to its ability to produce complex geometries with high precision and minimal waste.
3D Printing PCBs: The Concept
3D printing PCBs involves using additive manufacturing techniques to directly fabricate circuit boards. Instead of etching copper traces onto a substrate, 3D printers can deposit conductive materials in precise patterns to create the necessary electrical connections. This approach offers several advantages over traditional methods:
- Rapid Prototyping: 3D printing allows for quick iteration and testing of PCB designs, significantly reducing development time.
- Complex Geometries: 3D printers can create intricate and multi-layered circuits that would be difficult or impossible to achieve with traditional methods.
- Customization: Each PCB can be customized without the need for expensive tooling or setup changes.
- Reduced Waste: Additive manufacturing generates less waste compared to subtractive methods like etching.
- Integration with Other Components: 3D printing can integrate PCBs with other mechanical or structural components, enabling the creation of fully functional devices in a single print.
Materials for 3D Printed PCBs
The success of 3D printing PCBs depends on the availability of suitable materials. Key materials include:
- Conductive Inks and Pastes: These materials contain conductive particles (e.g., silver, copper, or graphene) suspended in a binder. They are deposited by the 3D printer to form the conductive traces.
- Substrate Materials: The base material of the PCB must be compatible with the 3D printing process. Common choices include thermoplastics like ABS and PLA, as well as specialized materials like polyimide.
- Dielectric Materials: These insulating materials are used to separate conductive layers in multi-layer PCBs. They must have good thermal and electrical insulation properties.
3D Printing Technologies for PCBs
Several 3D printing technologies are being explored for PCB fabrication:
- Fused Deposition Modeling (FDM): FDM printers extrude thermoplastic filaments layer by layer. Conductive filaments can be used to create traces, while non-conductive filaments form the substrate.
- Direct Ink Writing (DIW): DIW printers deposit conductive inks or pastes in precise patterns. This method offers high resolution and the ability to print on various substrates.
- Aerosol Jet Printing: This advanced technique uses a focused aerosol stream to deposit conductive materials with high precision. It is capable of creating fine features and multi-layer circuits.
- Stereolithography (SLA): SLA printers use UV light to cure liquid resin layer by layer. Conductive resins can be used to create traces, while non-conductive resins form the substrate.
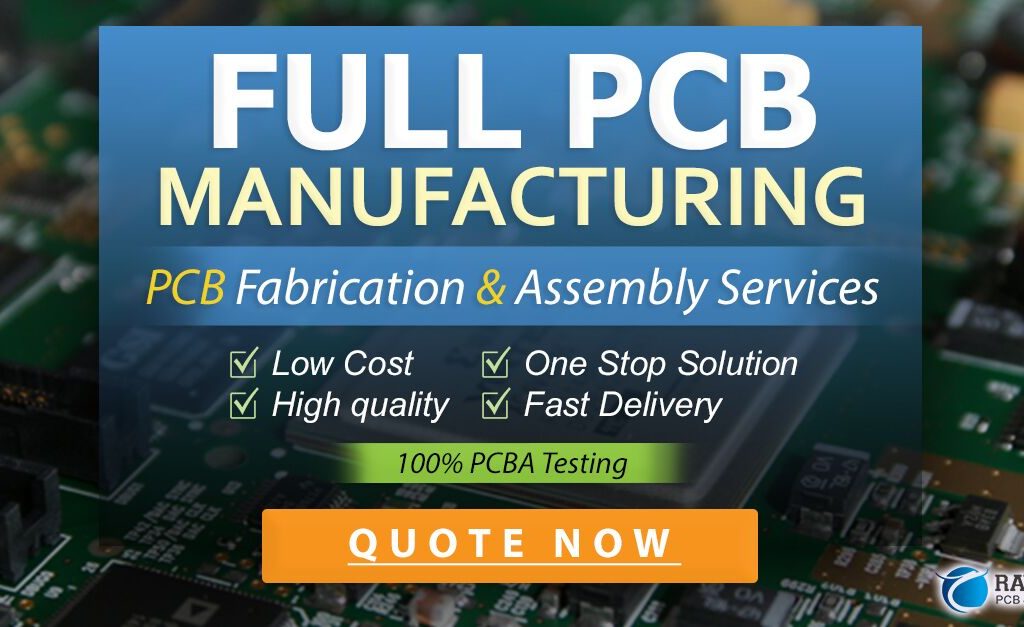
Generating 3D Printing Models for PCBs
The Role of CAD Software
Computer-Aided Design (CAD) software plays a crucial role in generating 3D printing models for PCBs. Engineers use CAD tools to design the PCB layout, including the placement of components and the routing of traces. The software then converts the design into a digital model that can be interpreted by the 3D printer.
Key Considerations in Model Generation
- Layer Thickness: The thickness of each printed layer affects the resolution and strength of the PCB. Thinner layers allow for finer details but may increase printing time.
- Support Structures: Complex geometries may require support structures to prevent sagging or collapsing during printing. These supports must be carefully designed and removed after printing.
- Material Properties: The digital model must account for the properties of the materials being used, such as conductivity, thermal expansion, and adhesion between layers.
- Multi-Layer Designs: For multi-layer PCBs, the model must specify the arrangement of conductive and dielectric layers, as well as the placement of vias (inter-layer connections).
Exporting and Preparing the Model
Once the design is complete, the CAD software exports the model in a format compatible with the 3D printer, such as STL or OBJ. The model is then imported into the printer’s software, where it is sliced into layers and prepared for printing. This step involves setting parameters like print speed, temperature, and material flow rate.
Challenges and Limitations of 3D Printing PCBs
While 3D printing PCBs offers numerous advantages, there are several challenges and limitations that need to be addressed:
- Material Limitations: The availability of high-quality conductive materials with good electrical properties is still limited. Researchers are actively working on developing new materials to overcome this hurdle.
- Resolution and Precision: Achieving the fine features and high precision required for modern PCBs can be challenging with current 3D printing technologies.
- Multi-Layer Complexity: Printing multi-layer PCBs with precise alignment of conductive and dielectric layers is complex and requires advanced printing techniques.
- Thermal Management: 3D printed PCBs may have different thermal properties compared to traditional boards, affecting heat dissipation and component performance.
- Cost: While 3D printing can reduce costs for prototyping and small-scale production, the initial investment in equipment and materials can be high.
Applications of 3D Printed PCBs
Despite the challenges, 3D printed PCBs are finding applications in various fields:
- Prototyping and R&D: 3D printing enables rapid prototyping, allowing engineers to quickly test and iterate on new designs.
- Custom Electronics: Customized PCBs can be produced for niche applications, such as wearable devices, medical implants, and IoT sensors.
- Education and Hobbyists: 3D printing lowers the barrier to entry for students and hobbyists interested in electronics design and fabrication.
- Aerospace and Defense: The ability to create lightweight, complex PCBs is valuable in aerospace and defense applications, where weight and space are critical factors.
- On-Demand Manufacturing: 3D printing allows for on-demand production of PCBs, reducing inventory costs and lead times.
Future Prospects and Innovations
The future of 3D printing PCBs is promising, with ongoing research and development aimed at overcoming current limitations and expanding the technology’s capabilities. Some key areas of innovation include:
- Advanced Materials: The development of new conductive and dielectric materials with improved electrical, thermal, and mechanical properties will enhance the performance of 3D printed PCBs.
- Hybrid Manufacturing: Combining 3D printing with traditional manufacturing techniques, such as CNC machining or pick-and-place assembly, can leverage the strengths of both approaches.
- Multi-Material Printing: The ability to print with multiple materials simultaneously will enable the creation of more complex and functional PCBs.
- AI and Machine Learning: AI-driven design tools can optimize PCB layouts for 3D printing, improving performance and reducing material usage.
- Scalability: Advances in 3D printing technology will make it more scalable, enabling larger production runs and reducing costs.
Conclusion
3D printing PCBs and generating printing models represent a significant leap forward in electronics manufacturing. This technology offers the potential to streamline the production process, reduce waste, and enable the creation of highly customized and complex circuits. While challenges remain, ongoing research and innovation are paving the way for a future where 3D printed PCBs are commonplace. As the technology continues to evolve, it will undoubtedly play a pivotal role in shaping the next generation of electronic devices.
In conclusion, 3D printing is not just a tool for creating physical objects; it is a transformative technology that is redefining the way we design, prototype, and manufacture electronic components. The integration of 3D printing into PCB fabrication is a testament to the power of innovation and its ability to drive progress in even the most established industries. As we look to the future, the possibilities are endless, and the impact of 3D printing on electronics manufacturing will only continue to grow.